- お役立ち記事
- The importance of “planned maintenance”—The basics of preventive maintenance that equipment maintenance departments should thoroughly implement
The importance of “planned maintenance”—The basics of preventive maintenance that equipment maintenance departments should thoroughly implement
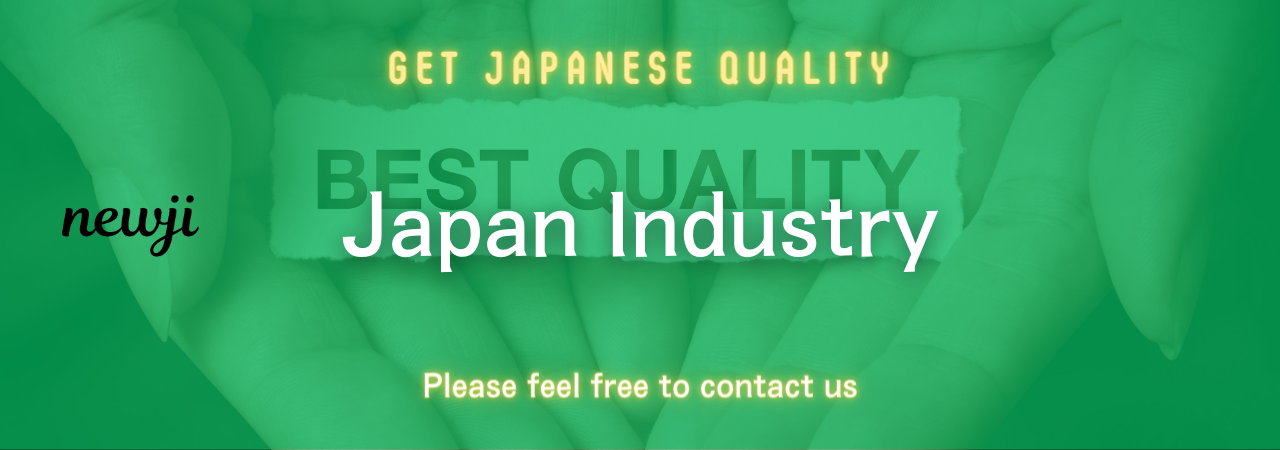
目次
Understanding Planned Maintenance
Planned maintenance, often referred to as preventive maintenance, is an approach that aims to keep equipment in good working order and prevent unexpected breakdowns.
The practice revolves around performing regular checks and maintenance tasks based on a pre-defined schedule.
This proactive strategy is vital for ensuring operational efficiency and longevity of equipment across various industries.
Unlike reactive maintenance, which occurs after equipment has failed, planned maintenance is executed before issues arise.
This makes it a smarter, more cost-effective approach.
Equipment maintenance departments, especially, should prioritize this method to minimize downtime and extend the life span of machinery.
Benefits of Planned Maintenance
Implementing a planned maintenance strategy brings numerous benefits.
Firstly, it significantly lowers the risk of unexpected equipment failures.
By detecting and resolving issues early, companies can avoid costly repairs and prolonged downtime.
Secondly, planned maintenance helps improve the efficiency and performance of equipment.
Regularly maintained machinery often operates more smoothly and uses energy more efficiently, providing savings on operational costs.
Moreover, this maintenance approach ensures safer working conditions.
Well-maintained equipment is less likely to pose safety risks to employees, reducing the chances of accidents and injuries.
This aspect alone makes it a crucial practice for any organization concerned about workplace safety.
Key Elements of Planned Maintenance
Effective planned maintenance involves several key elements.
These include identifying critical equipment, setting maintenance schedules, and having a dedicated team in place.
Identifying Critical Equipment
Not all equipment requires the same level of maintenance attention.
The first step in creating a planned maintenance schedule is identifying which machines are essential to your operations.
Focus on machinery that is critical to production or those that are expensive and difficult to replace.
Setting Maintenance Schedules
Once critical equipment is identified, the next step is to develop a maintenance schedule.
Consider factors like manufacturer recommendations, equipment age, usage patterns, and historical performance data.
Using this information helps tailor a maintenance plan that suits your specific needs.
Regular intervals for checks and servicing should be established, as well as guidelines for varying levels of maintenance.
This includes everything from daily inspections to semi-annual overhauls.
Clear documentation and record-keeping are vital throughout this process to ensure that maintenance activities are correctly executed and monitored.
Having a Dedicated Maintenance Team
An essential component of planned maintenance is having a competent and dedicated maintenance team.
This team should be equipped with the necessary skills and resources to carry out the maintenance tasks outlined on the schedule.
Continuous training and development for the maintenance staff are crucial.
The team should be well-versed in the latest industry practices and technologies to ensure maintenance efficiency.
Challenges of Planned Maintenance
While planned maintenance offers numerous benefits, it does come with its own set of challenges.
Organizations might struggle with the upfront costs and time investment required to implement a comprehensive maintenance program.
Additionally, scheduling regular maintenance without disrupting operations can be tricky.
Another challenge lies in accurately predicting when maintenance is necessary.
Relying solely on scheduled intervals might not always be sufficient, as equipment wear can occur at unpredictable rates.
This is why combining other maintenance strategies, like condition-based maintenance, might sometimes be beneficial.
Condition-based maintenance involves monitoring the actual condition of equipment to determine maintenance needs, providing a more dynamic and responsive approach.
Implementing a Successful Planned Maintenance Program
To successfully implement a planned maintenance program, companies should start by conducting a thorough assessment of their current maintenance practices and equipment needs.
This evaluation will provide insights into what changes or adjustments are required.
Obtaining buy-in from all levels of the organization is crucial.
Management must be committed to the initiative, while maintenance staff and machine operators should be engaged and motivated to adhere to the new procedures.
Investing in the right tools and technology can greatly enhance the effectiveness of a planned maintenance program.
Using maintenance management software helps streamline scheduling, record-keeping, and provides valuable data analytics.
Regular evaluation and adjustment of the plan are necessary to ensure its continued relevance and effectiveness.
Feedback should be gathered from maintenance teams and machine operators to identify potential improvements or address any challenges.
The Role of Planned Maintenance in Future-Proofing
In today’s fast-paced industrial landscape, the importance of planned maintenance cannot be overstated.
As industries gear towards innovation and technological advancement, ensuring that equipment runs efficiently becomes ever more crucial.
Planned maintenance contributes to future-proofing businesses by safeguarding against unexpected failures and disruptions.
It supports sustainable practices by maximizing equipment life cycles and reducing waste from premature replacements.
Furthermore, as companies adopt more sophisticated technologies, integrating data-driven insights into maintenance programs will be key.
Predictive analytics and the Internet of Things (IoT) are technologies that will play a pivotal role in augmenting traditional preventive maintenance strategies.
In conclusion, the basics of planned maintenance provide an essential foundation for any equipment maintenance department.
By prioritizing preventive measures, companies can safeguard not only their machinery but also their productivity and workforce safety.
Maintenance departments that thoroughly implement these practices will be better positioned to face the challenges and opportunities of the future.
資料ダウンロード
QCD調達購買管理クラウド「newji」は、調達購買部門で必要なQCD管理全てを備えた、現場特化型兼クラウド型の今世紀最高の購買管理システムとなります。
ユーザー登録
調達購買業務の効率化だけでなく、システムを導入することで、コスト削減や製品・資材のステータス可視化のほか、属人化していた購買情報の共有化による内部不正防止や統制にも役立ちます。
NEWJI DX
製造業に特化したデジタルトランスフォーメーション(DX)の実現を目指す請負開発型のコンサルティングサービスです。AI、iPaaS、および先端の技術を駆使して、製造プロセスの効率化、業務効率化、チームワーク強化、コスト削減、品質向上を実現します。このサービスは、製造業の課題を深く理解し、それに対する最適なデジタルソリューションを提供することで、企業が持続的な成長とイノベーションを達成できるようサポートします。
オンライン講座
製造業、主に購買・調達部門にお勤めの方々に向けた情報を配信しております。
新任の方やベテランの方、管理職を対象とした幅広いコンテンツをご用意しております。
お問い合わせ
コストダウンが利益に直結する術だと理解していても、なかなか前に進めることができない状況。そんな時は、newjiのコストダウン自動化機能で大きく利益貢献しよう!
(Β版非公開)