- お役立ち記事
- Key points for implementing Kaizen activities for on-site managers—How to achieve the results that management expects
Key points for implementing Kaizen activities for on-site managers—How to achieve the results that management expects
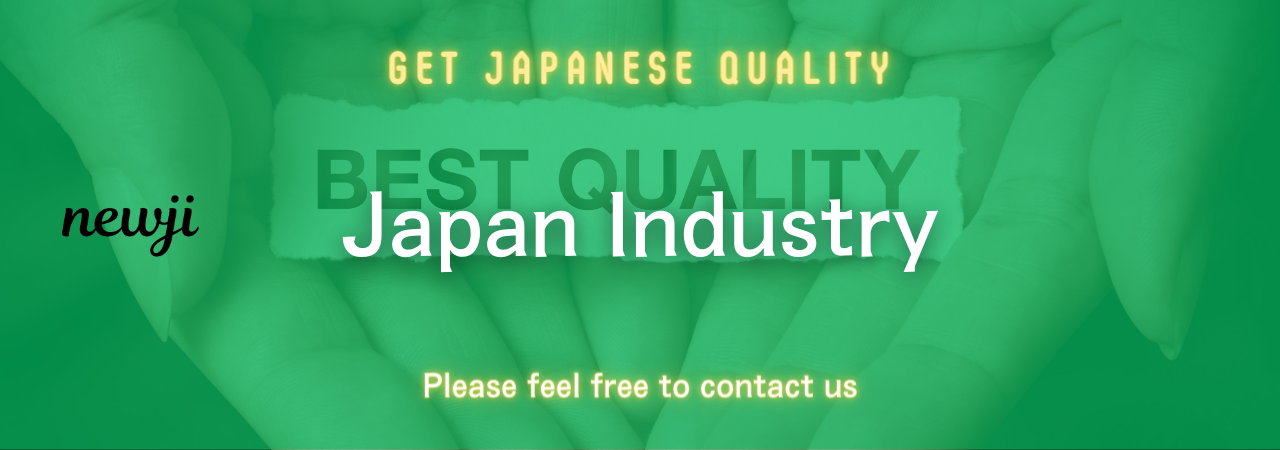
目次
Understanding Kaizen Activities
Kaizen is a Japanese term that means “continuous improvement.”
It’s a philosophy that aims for efficiency, productivity, and satisfaction in the workplace.
Kaizen activities focus on small, incremental changes that add up to significant improvements over time.
For on-site managers, implementing Kaizen activities can lead to enhanced operations and meet the expectations set by management.
The Importance of On-Site Managers in Kaizen
On-site managers play a crucial role in the success of Kaizen activities.
They are the ones who ensure that team members understand and execute these activities effectively.
Managers provide the support, resources, and encouragement needed for continuous improvement.
By fostering a culture of open communication and collaboration, they enable their teams to identify opportunities for improvement.
Key Steps for Implementing Kaizen Activities
1. Identify Areas for Improvement
Before any improvements can be made, it’s important to identify areas that need enhancement.
Managers should work with their teams to observe daily operations and gather feedback.
This will help in pinpointing inefficiencies or issues that can be corrected.
By focusing on these areas, the team can come up with practical solutions.
2. Set Clear Goals
Once areas for improvement are identified, it’s essential to set clear and achievable goals.
These goals should be aligned with the overall objectives of the organization.
Setting specific, measurable, and time-bound targets ensures that everyone knows what to aim for.
This clarity helps maintain focus and motivation during the Kaizen activities.
3. Encourage Employee Involvement
Kaizen is a team effort, and involving all employees is crucial to its success.
Encourage team members to share their ideas and suggestions for improvement.
Creating a culture where everyone feels valued and heard leads to increased engagement.
Managers should facilitate brainstorming sessions and discussions to gather input from the team.
4. Implement Small Changes
One of the core principles of Kaizen is implementing small, manageable changes.
Focus on making continuous, incremental improvements rather than large-scale transformations.
Small changes are easier to manage and adapt to, leading to better acceptance from the team.
As improvements are successfully implemented, they can build upon each other for greater impact.
5. Monitor and Measure Progress
To ensure the success of Kaizen activities, it is essential to monitor and measure progress consistently.
Develop key performance indicators (KPIs) to track improvements and assess the impact of changes.
Regularly review these metrics with the team to understand what’s working and what needs adjustment.
This ongoing evaluation helps maintain momentum and drives further enhancements.
6. Provide Training and Resources
For Kaizen activities to be effective, team members may require additional training or resources.
Equip employees with the necessary tools and knowledge to implement improvements.
Offering workshops, courses, or hands-on training sessions can enhance their skills and confidence.
A well-prepared team is more likely to succeed in achieving the set goals.
Overcoming Challenges in Kaizen Implementation
Resistance to Change
One of the challenges in implementing Kaizen is resistance to change.
Employees may be hesitant to adopt new methods or fear that changes might disrupt their workflow.
Managers can overcome this by clearly communicating the benefits and importance of Kaizen activities.
Regularly engaging with the team and addressing concerns can help ease the transition.
Lack of Commitment from Management
Successful Kaizen implementation requires commitment from top management.
Without their support, it can be difficult for on-site managers to allocate resources or push initiatives forward.
Managers should communicate the potential benefits of Kaizen to upper management and seek their endorsement.
This ensures that everyone is working towards the same objectives.
Insufficient Resources
Occasionally, limited resources can hinder the implementation of Kaizen activities.
Managers should work within their means to optimize available resources and prioritize the most impactful changes.
By demonstrating the value and results of Kaizen improvements, it may be possible to secure additional resources in the future.
Achieving Management’s Expectations with Kaizen
Kaizen activities can significantly impact an organization’s efficiency and productivity.
On-site managers need to align these activities with management’s expectations to demonstrate their value.
Regularly communicate progress and results to management to showcase the benefits of Kaizen.
By doing so, managers can gain management’s trust and support for future improvement initiatives.
In conclusion, implementing Kaizen activities requires careful planning and execution.
By following these key steps and involving the entire team, on-site managers can drive continuous improvement.
Overcoming challenges and communicating effectively with management ensures that Kaizen activities lead to the success that management expects.
Ultimately, Kaizen fosters a culture of innovation and excellence that benefits both employees and the organization.
資料ダウンロード
QCD調達購買管理クラウド「newji」は、調達購買部門で必要なQCD管理全てを備えた、現場特化型兼クラウド型の今世紀最高の購買管理システムとなります。
ユーザー登録
調達購買業務の効率化だけでなく、システムを導入することで、コスト削減や製品・資材のステータス可視化のほか、属人化していた購買情報の共有化による内部不正防止や統制にも役立ちます。
NEWJI DX
製造業に特化したデジタルトランスフォーメーション(DX)の実現を目指す請負開発型のコンサルティングサービスです。AI、iPaaS、および先端の技術を駆使して、製造プロセスの効率化、業務効率化、チームワーク強化、コスト削減、品質向上を実現します。このサービスは、製造業の課題を深く理解し、それに対する最適なデジタルソリューションを提供することで、企業が持続的な成長とイノベーションを達成できるようサポートします。
オンライン講座
製造業、主に購買・調達部門にお勤めの方々に向けた情報を配信しております。
新任の方やベテランの方、管理職を対象とした幅広いコンテンツをご用意しております。
お問い合わせ
コストダウンが利益に直結する術だと理解していても、なかなか前に進めることができない状況。そんな時は、newjiのコストダウン自動化機能で大きく利益貢献しよう!
(Β版非公開)