- お役立ち記事
- For process engineers in the semiconductor manufacturing industry! Dry etching plasma density control and yield improvement
For process engineers in the semiconductor manufacturing industry! Dry etching plasma density control and yield improvement
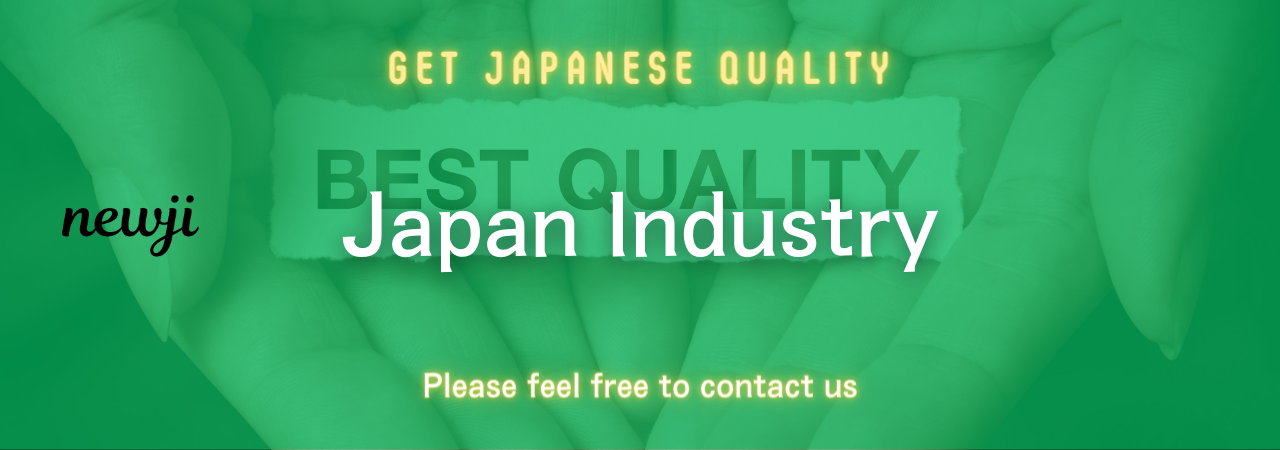
目次
Understanding Plasma Density in Dry Etching
Semiconductor manufacturing is a complex process that involves numerous critical stages, each contributing to the overall quality and functionality of the final product.
One such stage is dry etching, a crucial process for creating patterns on semiconductor wafers.
At the heart of dry etching is the use of plasma, a highly ionized gas that assists in removing material from the wafer surface.
For process engineers, controlling the plasma density is fundamental to ensuring the efficiency and success of the etching process.
Plasma density directly affects the etching rate and uniformity.
If not properly regulated, it can lead to defects and variations that impact the semiconductor’s performance and yield.
Therefore, a deep understanding of the factors influencing plasma density is essential for optimizing dry etching processes.
The Role of Plasma in Dry Etching
Plasma in dry etching serves several important functions.
It provides ions and radicals necessary for breaking the bonds of the material being etched, thus enabling the selective removal of material from the wafer.
The plasma is generated through radio frequency (RF) energy, which excites the gas molecules in the etching chamber, producing a soup of ions, electrons, and neutral particles.
The characteristics of the plasma, such as its density and energy distribution, are influenced by numerous parameters, including RF power, chamber pressure, gas flow rate, and the composition of the gases used.
Process engineers must carefully control these parameters to maintain the desired plasma density and ensure precise etching.
Challenges in Plasma Density Control
One of the primary challenges in controlling plasma density is its sensitivity to variations in process parameters.
For instance, a slight change in RF power or gas flow can significantly alter the plasma characteristics.
Moreover, the complex interactions between different variables make it difficult to predict the exact effect of changes in one parameter on the plasma.
Another issue is maintaining uniform plasma density across the wafer.
Non-uniformity can result in uneven etching, leading to features with varying depths and potentially causing defects.
Achieving uniform plasma distribution requires precise tuning of process parameters and chamber design.
Techniques for Optimizing Plasma Density
There are several approaches process engineers can employ to optimize plasma density in dry etching and enhance yield quality.
Parameter Calibration
Regular calibration of the etching equipment is essential for maintaining consistent process parameters.
This includes checking and adjusting RF power settings, gas flow rates, and chamber pressure to ensure they remain within specified tolerances.
Calibration helps minimize variations in plasma density across different production runs.
Plasma Diagnostics
Advanced diagnostic tools, such as Langmuir probes and optical emission spectroscopy, provide real-time monitoring of plasma characteristics.
These tools allow engineers to measure plasma density, electron temperature, and chemical composition.
By analyzing this data, engineers can make informed adjustments to the process to achieve optimal plasma conditions.
Closed-Loop Control Systems
Implementing closed-loop control systems can enhance plasma density regulation.
These systems use feedback from plasma diagnostics to automatically adjust process parameters, helping maintain a stable and uniform plasma environment.
Closed-loop systems reduce human error and improve process reliability, ultimately leading to better yield outcomes.
Improving Yield through Plasma Density Control
Monitored and optimized plasma density directly contributes to yield improvement in semiconductor manufacturing.
When plasma density is well-controlled, the etching process produces features with precise dimensions and smooth surfaces, reducing the likelihood of defects such as micro-masking or pattern distortion.
Enhanced Process Consistency
By maintaining a uniform plasma density, process engineers ensure consistent etching rates across the entire wafer.
This consistency is crucial for producing semiconductors that meet stringent quality standards and are free from variations that could affect performance.
Reduced Defects and Rework
Effective plasma density control minimizes defects related to over-etching or under-etching.
This reduction in defects decreases the need for rework, which can be costly and time-consuming.
Lower defect rates also improve throughput, as more wafers successfully pass quality control checks on the first attempt.
Scalability and Flexibility
When plasma density control is finely managed, manufacturing processes can be more easily scaled to meet increasing demand.
This scalability ensures that production facilities can handle larger volumes without compromising quality.
Additionally, well-controlled plasma processes can adapt to new product designs and materials, offering manufacturers the flexibility to innovate without significant retooling efforts.
Conclusion
For process engineers in the semiconductor industry, understanding and controlling plasma density in dry etching is crucial for achieving high yield and quality.
With the right strategies and tools, plasma density can be optimized to ensure consistent and defect-free etching processes.
Through careful parameter calibration, advanced diagnostics, and closed-loop control systems, plasma density becomes a manageable factor rather than a source of uncertainty.
As semiconductor technologies continue to evolve, proficient plasma density management will remain a key contributor to successful manufacturing and competitive advantage.
資料ダウンロード
QCD調達購買管理クラウド「newji」は、調達購買部門で必要なQCD管理全てを備えた、現場特化型兼クラウド型の今世紀最高の購買管理システムとなります。
ユーザー登録
調達購買業務の効率化だけでなく、システムを導入することで、コスト削減や製品・資材のステータス可視化のほか、属人化していた購買情報の共有化による内部不正防止や統制にも役立ちます。
NEWJI DX
製造業に特化したデジタルトランスフォーメーション(DX)の実現を目指す請負開発型のコンサルティングサービスです。AI、iPaaS、および先端の技術を駆使して、製造プロセスの効率化、業務効率化、チームワーク強化、コスト削減、品質向上を実現します。このサービスは、製造業の課題を深く理解し、それに対する最適なデジタルソリューションを提供することで、企業が持続的な成長とイノベーションを達成できるようサポートします。
オンライン講座
製造業、主に購買・調達部門にお勤めの方々に向けた情報を配信しております。
新任の方やベテランの方、管理職を対象とした幅広いコンテンツをご用意しております。
お問い合わせ
コストダウンが利益に直結する術だと理解していても、なかなか前に進めることができない状況。そんな時は、newjiのコストダウン自動化機能で大きく利益貢献しよう!
(Β版非公開)