- お役立ち記事
- For managers of research and development departments in the medical device manufacturing industry! Evaluation method for mechanical strength and biocompatibility of biomaterials
For managers of research and development departments in the medical device manufacturing industry! Evaluation method for mechanical strength and biocompatibility of biomaterials
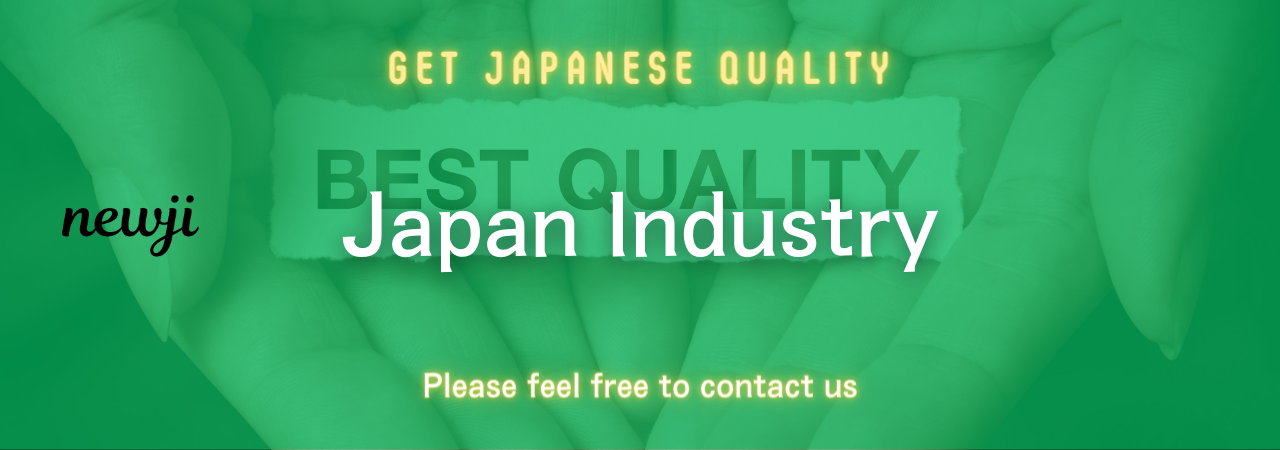
目次
Understanding Mechanical Strength Evaluation
In the medical device manufacturing industry, the research and development departments are tasked with ensuring that biomaterials meet rigorous standards for mechanical strength.
Mechanical strength is an essential characteristic of biomaterials used in medical devices.
It determines how well a material can withstand forces without deforming or breaking.
Assessing mechanical strength involves a plethora of tests that simulate the conditions a biomaterial might face during its application.
Common methods include tension, compression, and bending tests.
These tests are crucial for understanding how materials will perform under mechanical stress.
Tensile testing, for instance, measures a material’s elongation and breaking point when subjected to pulling forces.
This test is pivotal for materials intended for sutures or orthopedic devices, which experience extensive stretching and pulling forces.
Compression testing is used to evaluate how materials behave under compressive forces.
This test is especially relevant for biomaterials utilized in implants or supportive devices, where they must maintain shape and functionality under substantial compressive loads.
Lastly, bending tests help identify the flexibility and rigidity of materials.
This is important for materials used in catheters or stents, which need to navigate the anatomy without compromising structural integrity.
Understanding and applying these methods allow researchers to accurately evaluate the mechanical properties of biomaterials and ensure they meet the necessary standards for medical use.
The Importance of Biocompatibility in Biomaterials
While mechanical strength is vital, biocompatibility cannot be overlooked when evaluating biomaterials.
Biocompatibility refers to the material’s ability to perform in a biological environment without eliciting harmful responses.
A biocompatible material should not cause adverse effects like inflammation, allergic reactions, or toxicity.
The evaluation of biocompatibility involves a series of biological tests to ascertain how biomaterials interact with living tissues.
In vitro tests, such as cytotoxicity screenings, are conducted to identify any toxic substances the material may release.
These tests help researchers determine the initial safety profile of the biomaterial.
In vivo tests, which are carried out on animal models, are more comprehensive evaluations that consider the body’s response to the material over time.
These tests are crucial for identifying any long-term adverse effects or immune responses.
Additionally, clinical trials on human subjects may also be conducted to ensure absolute biocompatibility before a product reaches the market.
These tests ensure that when implanted or introduced into the body, biomaterials function safely without compromising patient health.
Incorporating comprehensive biocompatibility assessments during the R&D phase is essential for developing safe medical devices.
Integrating Mechanical Strength and Biocompatibility Evaluations
While mechanical strength and biocompatibility assessments are conducted separately, their integration plays a vital role in the overall evaluation process of biomaterials.
Successful medical devices must exhibit both adequate mechanical properties and exceptional biocompatibility.
The challenge lies in balancing these attributes, as materials with high mechanical strength often compromise biocompatibility, and vice versa.
One effective strategy to integrate these evaluations is through the use of composite materials.
By combining materials with different properties, researchers can create biomaterials that excel in both mechanical performance and biocompatibility.
For example, incorporating biocompatible coatings on strong base materials can enhance the overall safety and functionality without sacrificing mechanical properties.
Moreover, advancing technologies such as 3D printing allow for precise fabrication of customized biomaterials.
This technology facilitates the creation of intricate designs that optimize both mechanical strength and biocompatibility.
Researchers can use 3D printing to experiment with material combinations and structures that historical manufacturing methods struggled to achieve.
As R&D departments continue developing innovative materials, understanding the synergy between mechanical strength and biocompatibility is crucial.
This integrated approach ensures the creation of cutting-edge medical devices that improve patient safety and treatment outcomes.
Importance of Standardized Testing Procedures
In the pursuit of reliable biomaterial evaluations, standardized testing procedures are paramount.
Such standardization ensures consistency in how mechanical strength and biocompatibility are assessed across the industry.
Organizations like the American Society for Testing and Materials (ASTM) and the International Organization for Standardization (ISO) have developed guidelines for testing biomaterials.
Following these standards is important to verify that the results are accurate and comparable.
Standardized testing procedures ensure physicians and regulators can trust the safety and effectiveness of medical devices.
This trust is crucial for gaining market approval from regulatory bodies like the U.S. Food and Drug Administration (FDA) or the European Medicines Agency (EMA).
Furthermore, adherence to standardized procedures streamlines the R&D process, allowing for more efficient development cycles and quicker time-to-market strategies.
Thus, for managers of R&D departments, implementing these standardized testing protocols is an investment in the project’s success and integrity.
Challenges and Future Directions
Despite the advancements in evaluating mechanical strength and biocompatibility, several challenges remain.
Emerging materials, such as bioresorbable polymers and smart biomaterials, present unique evaluation challenges due to their novel properties and functions.
Regulatory frameworks might need adjustments to accommodate the testing of these new materials.
Another challenge is ensuring that the evaluations mimic real-life scenarios as closely as possible.
It requires ongoing innovation in testing methodologies to account for the dynamic and complex nature of the human body.
The future of biomaterial evaluation lies in the development of more predictive and less invasive testing methods.
Computer simulations and predictive modeling are becoming increasingly valuable in understanding material behaviors and interactions without extensive physical testing.
Enhanced imaging techniques, such as micro-CT scans, provide detailed insights into material structure and integrity without destructive testing.
These emerging technologies offer a promising direction for improving how R&D departments assess the suitability of biomaterials for medical device applications.
In conclusion, a comprehensive understanding and integration of mechanical strength and biocompatibility evaluations are critical for developing successful medical devices in the evolving landscape of the healthcare industry.
資料ダウンロード
QCD調達購買管理クラウド「newji」は、調達購買部門で必要なQCD管理全てを備えた、現場特化型兼クラウド型の今世紀最高の購買管理システムとなります。
ユーザー登録
調達購買業務の効率化だけでなく、システムを導入することで、コスト削減や製品・資材のステータス可視化のほか、属人化していた購買情報の共有化による内部不正防止や統制にも役立ちます。
NEWJI DX
製造業に特化したデジタルトランスフォーメーション(DX)の実現を目指す請負開発型のコンサルティングサービスです。AI、iPaaS、および先端の技術を駆使して、製造プロセスの効率化、業務効率化、チームワーク強化、コスト削減、品質向上を実現します。このサービスは、製造業の課題を深く理解し、それに対する最適なデジタルソリューションを提供することで、企業が持続的な成長とイノベーションを達成できるようサポートします。
オンライン講座
製造業、主に購買・調達部門にお勤めの方々に向けた情報を配信しております。
新任の方やベテランの方、管理職を対象とした幅広いコンテンツをご用意しております。
お問い合わせ
コストダウンが利益に直結する術だと理解していても、なかなか前に進めることができない状況。そんな時は、newjiのコストダウン自動化機能で大きく利益貢献しよう!
(Β版非公開)