- お役立ち記事
- A must-see for production engineers in the valve seat manufacturing industry for semiconductor manufacturing equipment! Selection of materials that improve airtightness and chemical resistance
A must-see for production engineers in the valve seat manufacturing industry for semiconductor manufacturing equipment! Selection of materials that improve airtightness and chemical resistance
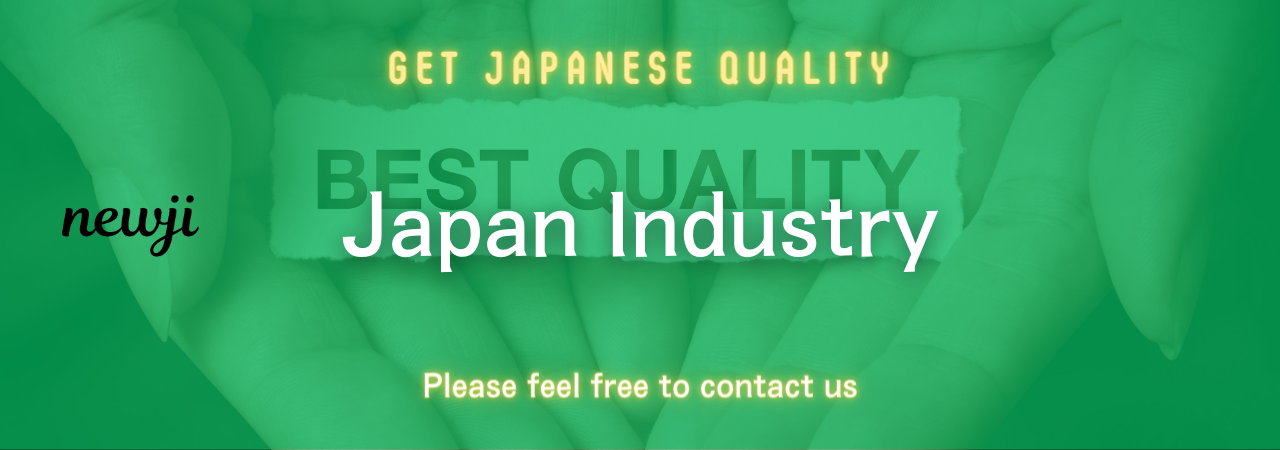
目次
Understanding Valve Seats in Semiconductor Manufacturing Equipment
Semiconductor manufacturing is an industry where precision and reliability are paramount.
One crucial component of the equipment used in this industry is the valve seat.
Valve seats are critical in ensuring that the equipment operates efficiently and accurately.
They play a significant role in maintaining airtight conditions and controlling the flow of gases and chemicals.
The Importance of Airtightness and Chemical Resistance
Airtightness is crucial when it comes to valve seats in semiconductor manufacturing equipment.
Leaks or breaks in airtightness can lead to contamination and inefficiencies in the production process.
As semiconductor devices continue to shrink and become more complex, even the smallest contaminants can cause significant issues.
Chemical resistance is another vital factor.
During semiconductor manufacturing, equipment is exposed to various chemicals that can be corrosive or reactive.
If the valve seat material does not withstand these chemicals, it can break down, leading to equipment failure or contamination.
Therefore, selecting the right material for valve seats is essential to ensure both airtightness and chemical resistance.
Materials Commonly Used for Valve Seats
When it comes to choosing materials for valve seats, there are several options each with their own unique properties.
The materials’ selection depends on several factors, including the type of chemicals used, the temperatures involved, and the desired lifespan of the equipment.
Polytetrafluoroethylene (PTFE)
PTFE, often known by the brand name Teflon, is a popular material for valve seats.
It is well-known for its excellent chemical resistance and non-stick properties.
PTFE can withstand exposure to a wide range of chemicals without degrading, making it suitable for semiconductor manufacturing where various corrosive substances are used.
Additionally, PTFE has a low friction coefficient, which reduces wear and extends the life of the valve seat.
PFA and FEP
Perfluoroalkoxy (PFA) and fluorinated ethylene propylene (FEP) are similar to PTFE but offer additional benefits.
They provide higher flexibility and a better thermal stability range.
PFA and FEP are preferred for applications that require a combination of flexibility and chemical resistance, particularly in high-temperature environments.
PCTFE
Polychlorotrifluoroethylene (PCTFE) offers exceptional moisture resistance and low gas permeability.
These properties make it an excellent option for valve seats used in environments requiring high levels of airtightness.
PCTFE maintains its mechanical properties even at cryogenic temperatures, providing durability across a wide range of conditions.
Elastomers
Elastomers, such as Viton and Kalrez, are versatile materials often used for valve seats.
These materials provide excellent chemical resistance and can create tight seals.
Elastomers are useful in applications where flexibility and the ability to conform to irregular surfaces are needed.
Factors to Consider When Selecting Materials
Choosing the right material for valve seats in semiconductor manufacturing equipment involves considering several factors.
Chemical Compatibility
The valve seat material must be compatible with the chemicals it will encounter in the manufacturing process.
Selecting a material that reacts with the chemicals can result in degradation and leaks.
Consulting chemical compatibility charts and conducting tests can help ensure the selected material will perform well.
Temperature Range
The manufacturing process may involve extreme temperatures, impacting the material’s performance.
Materials that become brittle at low temperatures or lose strength at high temperatures should be avoided.
Choose materials that maintain their properties across the expected temperature range.
Durability and Longevity
Valve seats should be durable and have a long service life to minimize downtime and maintenance costs.
Materials that resist wear and tear will contribute to the overall efficiency of the equipment.
Cost Considerations
While performance is critical, cost is also a factor.
Balancing between the material’s performance and budgetary constraints is important to achieve cost-effectiveness.
Innovations in Material Technology
The semiconductor industry is continuously evolving, and with it, the development of new materials for valve seats.
Advancements in polymer science and manufacturing technology are leading to materials with even better performance.
Composite Materials
Composite materials combine the best properties of different substances.
They offer improved strength, chemical resistance, and temperature stability.
These materials can provide innovative solutions to meet complex demands in semiconductor manufacturing.
Advanced Coatings
Applying advanced coatings to traditional materials can enhance their properties.
Coatings can improve surface smoothness, reduce friction, and increase resistance to chemicals and wear.
International collaborations and research initiatives are driving innovations, exploring eco-friendly and sustainable alternatives that maintain performance levels.
Conclusion
In the semiconductor manufacturing industry, selecting the right material for valve seats is crucial.
The choice impacts the equipment’s airtightness, chemical resistance, and overall performance.
By carefully considering chemical compatibility, temperature range, durability, and cost, production engineers can select materials that ensure reliable and efficient operations.
As the industry continues to advance, keeping abreast of new material technologies will provide opportunities for enhanced performance.
Understanding these factors and innovations will empower production engineers to make informed decisions, ultimately improving the effectiveness of semiconductor manufacturing processes.
資料ダウンロード
QCD調達購買管理クラウド「newji」は、調達購買部門で必要なQCD管理全てを備えた、現場特化型兼クラウド型の今世紀最高の購買管理システムとなります。
ユーザー登録
調達購買業務の効率化だけでなく、システムを導入することで、コスト削減や製品・資材のステータス可視化のほか、属人化していた購買情報の共有化による内部不正防止や統制にも役立ちます。
NEWJI DX
製造業に特化したデジタルトランスフォーメーション(DX)の実現を目指す請負開発型のコンサルティングサービスです。AI、iPaaS、および先端の技術を駆使して、製造プロセスの効率化、業務効率化、チームワーク強化、コスト削減、品質向上を実現します。このサービスは、製造業の課題を深く理解し、それに対する最適なデジタルソリューションを提供することで、企業が持続的な成長とイノベーションを達成できるようサポートします。
オンライン講座
製造業、主に購買・調達部門にお勤めの方々に向けた情報を配信しております。
新任の方やベテランの方、管理職を対象とした幅広いコンテンツをご用意しております。
お問い合わせ
コストダウンが利益に直結する術だと理解していても、なかなか前に進めることができない状況。そんな時は、newjiのコストダウン自動化機能で大きく利益貢献しよう!
(Β版非公開)