- お役立ち記事
- “Improvement ideas for inventory management” for mid-level employees—How the purchasing department can help reduce inventory costs
“Improvement ideas for inventory management” for mid-level employees—How the purchasing department can help reduce inventory costs
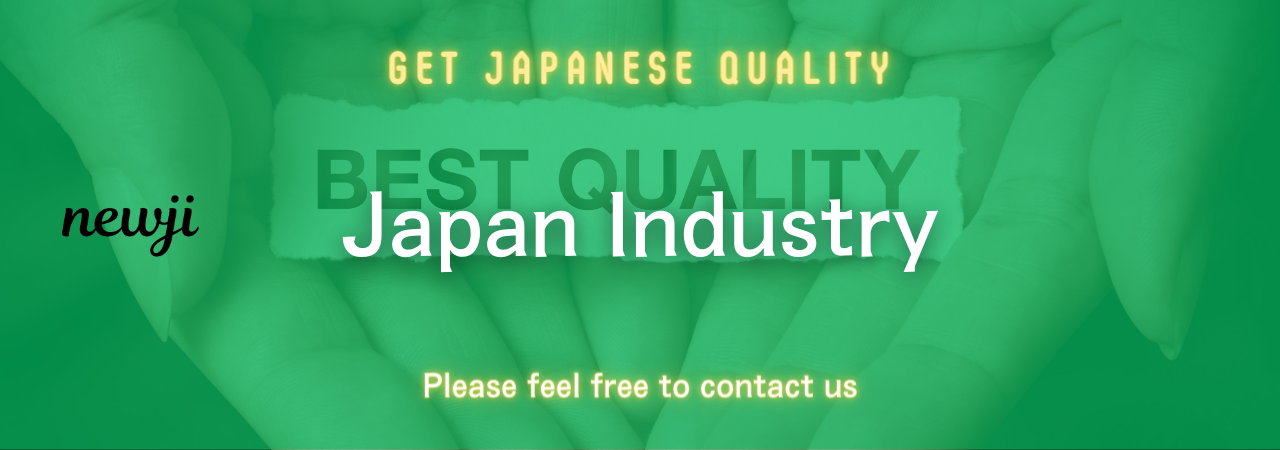
目次
Understanding Inventory Management
Inventory management is a crucial aspect of any business, particularly in companies that deal with physical products.
It’s the process of overseeing and controlling the order, storage, and use of components that a company will use in the production of items it sells, as well as overseeing and controlling quantities of finished products for sale.
Good inventory management means less capital tied up in inventory, reduced warehousing costs, and, ultimately, an improved bottom line.
The Role of the Purchasing Department
The purchasing department plays a pivotal role in inventory management.
It is responsible for acquiring the materials and products that the company needs in order to operate efficiently.
An effective purchasing department sources reliable suppliers, negotiates favorable prices, and ensures timely delivery of materials.
Improving inventory management involves the purchasing department working collaboratively with other departments to forecast demand and analyze inventory levels.
Their role is essential in maintaining a balance between too much inventory, which ties up capital, and too little inventory, which can lead to stockouts and lost sales.
Improvement Idea 1: Implementing Just-In-Time Inventory
One of the most effective ways to manage inventory is by adopting a Just-In-Time (JIT) inventory system.
JIT is a strategy that aligns raw-material orders from suppliers directly with production schedules.
This approach can significantly reduce costs associated with storing excess inventory.
By implementing a JIT system, businesses only keep inventory on hand that will be used in the near future, thus minimizing holding costs.
For the purchasing department, this means establishing strong relationships with suppliers who can deliver quickly and consistently.
It may also require investment in advanced ordering systems that can accurately forecast when stock will be needed based on sales data and production schedules.
Improvement Idea 2: Utilizing Inventory Management Software
In the digital age, using technology to track and manage inventory can greatly increase efficiency and accuracy.
Inventory management software can automate many of the processes involved in inventory control, reducing errors and saving time.
Investing in robust inventory management software allows businesses to track stock levels in real time, receive alerts when stock is running low, and generate reports that help in decision-making.
For purchasing departments, such software can provide critical insights into spending patterns and supplier performance, aiding in negotiations and planning.
Selecting the Right Software
Selecting the right inventory management software is important.
Not all systems are created equal, and the best choice will depend on the specific needs of your business.
Consider factors such as ease of use, cost, scalability, and the specific functionalities offered, such as integration with other systems and comprehensive reporting capabilities.
Improvement Idea 3: Training and Development
An often overlooked but highly impactful way to improve inventory management is through training and development of staff.
Employees should be well-versed in the company’s inventory management practices and procedures.
Regular training sessions can help ensure that all team members understand their role in the inventory management process.
For purchasing departments, this might mean training in negotiation techniques, vendor management, and the use of any new technology or systems.
Additionally, fostering a culture of continuous improvement and encouraging employees to offer suggestions can lead to innovative ideas for further enhancing inventory management practices.
Improvement Idea 4: Analyzing Supplier Performance
Analyzing supplier performance is crucial for effective inventory management.
Reliable suppliers who deliver quality materials on time allow businesses to maintain optimal inventory levels without holding excess stock.
Purchasing departments should evaluate their suppliers regularly, looking at factors such as delivery time, quality of goods, and pricing stability.
This analysis will help determine which suppliers are dependable partners and which might be contributing to inventory inefficiencies.
Switching to more reliable suppliers or renegotiating terms with existing suppliers can lead to better inventory management and cost savings.
Improvement Idea 5: Optimizing Stock Levels
The optimization of stock levels is vital in reducing inventory carrying costs.
Carrying too much stock ties up resources and can increase the risk of obsolescence, while too little stock can lead to missed sales and diminished customer satisfaction.
To find the right balance, businesses should utilize tools such as Economic Order Quantity (EOQ) and safety stock calculations.
These methods help in determining the ideal order size and when to reorder, ensuring that stock levels are maintained without excess.
The purchasing department should collaborate with sales and analytics teams to access accurate sales forecasts and adjust purchasing strategies accordingly.
This collaborative approach ensures that stock levels are optimized in line with demand patterns.
Conclusion
Effective inventory management is essential for reducing costs and optimizing a company’s operational efficiency.
By implementing strategies like Just-In-Time inventory, leveraging technology, investing in staff training, analyzing supplier performance, and optimizing stock levels, mid-level employees in the purchasing department can significantly contribute to better inventory management.
Each strategy requires an understanding of both the immediate needs of the business and the long-term objectives.
By focusing on these areas, the purchasing department can play a crucial role in aligning inventory management practices with the broader goals of the organization, ultimately leading to improved profitability and competitiveness.
資料ダウンロード
QCD調達購買管理クラウド「newji」は、調達購買部門で必要なQCD管理全てを備えた、現場特化型兼クラウド型の今世紀最高の購買管理システムとなります。
ユーザー登録
調達購買業務の効率化だけでなく、システムを導入することで、コスト削減や製品・資材のステータス可視化のほか、属人化していた購買情報の共有化による内部不正防止や統制にも役立ちます。
NEWJI DX
製造業に特化したデジタルトランスフォーメーション(DX)の実現を目指す請負開発型のコンサルティングサービスです。AI、iPaaS、および先端の技術を駆使して、製造プロセスの効率化、業務効率化、チームワーク強化、コスト削減、品質向上を実現します。このサービスは、製造業の課題を深く理解し、それに対する最適なデジタルソリューションを提供することで、企業が持続的な成長とイノベーションを達成できるようサポートします。
オンライン講座
製造業、主に購買・調達部門にお勤めの方々に向けた情報を配信しております。
新任の方やベテランの方、管理職を対象とした幅広いコンテンツをご用意しております。
お問い合わせ
コストダウンが利益に直結する術だと理解していても、なかなか前に進めることができない状況。そんな時は、newjiのコストダウン自動化機能で大きく利益貢献しよう!
(Β版非公開)