- お役立ち記事
- A must-see for managers of equipment technology departments in the semiconductor industry! How to improve line utilization by introducing automation technology
月間76,176名の
製造業ご担当者様が閲覧しています*
*2025年3月31日現在のGoogle Analyticsのデータより
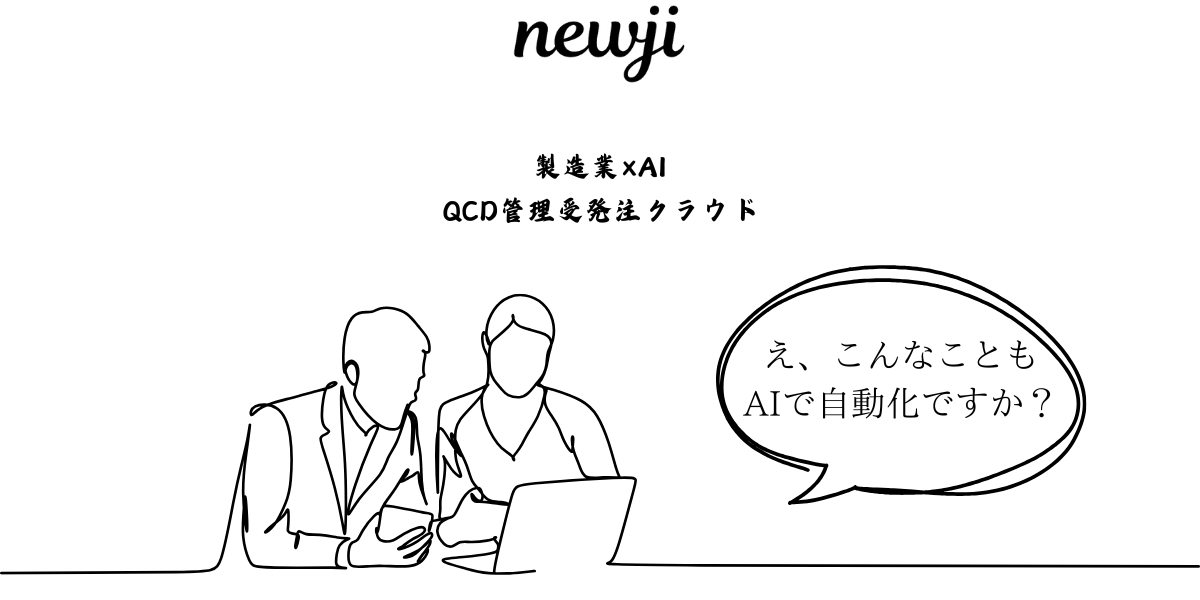
A must-see for managers of equipment technology departments in the semiconductor industry! How to improve line utilization by introducing automation technology
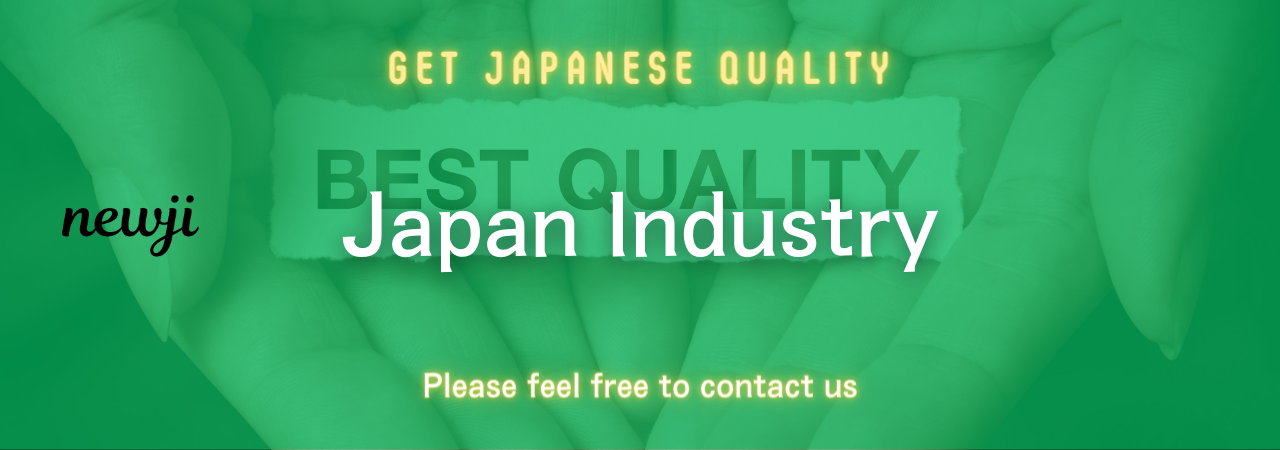
目次
Introduction to Line Utilization in the Semiconductor Industry
The semiconductor industry has always been at the forefront of technological advancement.
As the demand for more sophisticated and efficient devices increases, so too does the need for more efficient production processes.
One critical aspect that significantly influences the profitability and productivity of semiconductor manufacturing is line utilization.
In simple terms, line utilization refers to how effectively a semiconductor production line is used during manufacturing processes.
Every manager in the equipment technology department is constantly looking for ways to optimize line utilization while maintaining the quality and throughput of the production process.
One effective strategy is the introduction of automation technology, which not only enhances the efficiency of production lines but also reduces human error and operational costs.
The Role of Automation in Semiconductor Manufacturing
Automation technology plays a pivotal role in the semiconductor manufacturing process.
It involves using machinery and technology systems to perform tasks that would traditionally be completed by humans.
Incorporating automation in production lines can lead to remarkable improvements in efficiency and reliability.
In the context of the semiconductor industry, automation can encompass numerous applications.
These include robotics for handling and processing wafers, automated testing equipment for ensuring product quality, and software solutions for scheduling and workflow management.
Each of these applications can contribute significantly to better line utilization when implemented correctly.
Benefits of Automation in Improving Line Utilization
Enhancing Production Speed
One of the primary benefits of automation in semiconductor manufacturing is the increase in production speed.
Automation systems can operate continuously without breaks, unlike human workers who require downtime, rest, and shift changes.
This continuous operation drastically increases throughput, allowing semiconductor companies to meet increasing demand without compromising on delivery timelines.
Reducing Errors and Rework
In manual processes, human error is often unavoidable but can lead to costly rework and material waste.
By implementing automation, companies can significantly reduce such errors.
Automated systems are designed to perform repetitive tasks with high precision and consistency, minimizing the need for rework and ensuring high-quality output from the start.
This reduction in errors not only saves time but also conserves resources, contributing positively to line utilization.
Optimizing Resource Management
Automation also aids in better resource management.
With advanced software, production lines can be scheduled efficiently, raw materials can be utilized optimally, and the workforce can be allocated according to demand.
This optimized resource allocation ensures that every segment of the production line is used to its full potential, thereby improving overall line utilization.
Improving Data Collection and Analysis
Modern automation technologies are equipped with sophisticated sensors and software that gather a wealth of data during operation.
This data can be analyzed to provide valuable insights into the performance of different processes and equipment.
Managers can use this information to identify bottlenecks, predict maintenance needs, and implement process improvements.
The ability to quickly address issues based on real-time data significantly enhances the efficiency and effectiveness of production lines.
Steps to Implement Automation for Improved Line Utilization
Assess Current Production Processes
The first step towards implementing automation is to thoroughly assess the current production processes.
Managers should identify areas where automation can replace or augment manual operations.
Understanding the current pain points and challenges will help prioritize automation projects that offer the greatest impact on line utilization.
Select the Right Automation Technologies
Once potential areas for automation have been identified, the next step is to choose the appropriate technologies.
Given the varied tasks in semiconductor manufacturing, it’s important to select automation solutions that are specifically tailored to the needs of the operation.
Consulting with automation experts or vendors can provide insights into the best options available.
Integrate Automation with Existing Systems
Successful implementation of automation requires seamless integration with existing systems and processes.
This integration may involve updating software to be compatible with new hardware, training staff to operate and monitor automated systems, and setting up communication protocols for smooth operation.
A well-integrated system ensures minimal disruption during the transition phase and maximizes the efficiency of the production line.
Monitor and Evaluate Automation Performance
Post-implementation, it is crucial to continuously monitor the performance of the automated systems.
Gathering performance data will help managers evaluate whether the automation is effectively improving line utilization.
Ongoing analysis also provides opportunities for continuous improvement, ensuring that the automation remains aligned with the changing demands of semiconductor manufacturing.
Conclusion
In the competitive landscape of semiconductor manufacturing, effective line utilization is indispensable for maintaining an edge.
Automation technology presents a significant opportunity to optimize production processes, enhance efficiency, and reduce errors.
By incorporating automation, equipment technology departments can ensure that their production lines are not only productive but also adaptable to future technological advancements.
While the transition to automation requires careful planning and execution, the long-term benefits undoubtedly justify the effort.
Managers who embrace these changes are likely to see considerable improvements in their operation’s productivity and overall bottom line.
資料ダウンロード
QCD管理受発注クラウド「newji」は、受発注部門で必要なQCD管理全てを備えた、現場特化型兼クラウド型の今世紀最高の受発注管理システムとなります。
ユーザー登録
受発注業務の効率化だけでなく、システムを導入することで、コスト削減や製品・資材のステータス可視化のほか、属人化していた受発注情報の共有化による内部不正防止や統制にも役立ちます。
NEWJI DX
製造業に特化したデジタルトランスフォーメーション(DX)の実現を目指す請負開発型のコンサルティングサービスです。AI、iPaaS、および先端の技術を駆使して、製造プロセスの効率化、業務効率化、チームワーク強化、コスト削減、品質向上を実現します。このサービスは、製造業の課題を深く理解し、それに対する最適なデジタルソリューションを提供することで、企業が持続的な成長とイノベーションを達成できるようサポートします。
製造業ニュース解説
製造業、主に購買・調達部門にお勤めの方々に向けた情報を配信しております。
新任の方やベテランの方、管理職を対象とした幅広いコンテンツをご用意しております。
お問い合わせ
コストダウンが利益に直結する術だと理解していても、なかなか前に進めることができない状況。そんな時は、newjiのコストダウン自動化機能で大きく利益貢献しよう!
(β版非公開)