- お役立ち記事
- Specific methods for achieving zero errors using poka-yoke techniques that mid-level employees in the equipment maintenance department should master
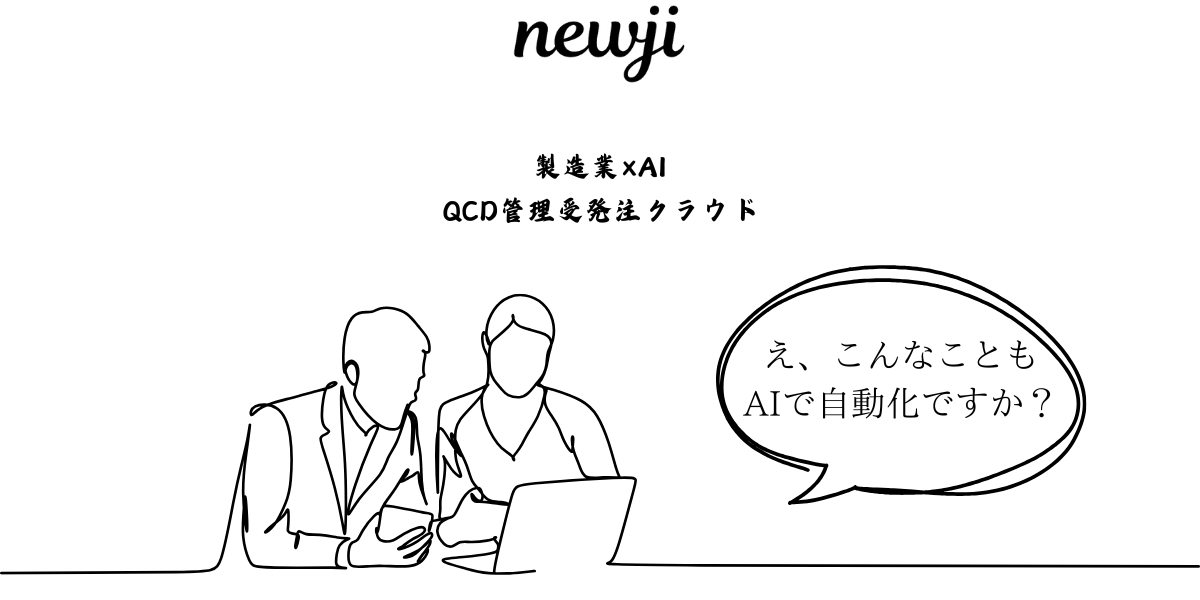
Specific methods for achieving zero errors using poka-yoke techniques that mid-level employees in the equipment maintenance department should master
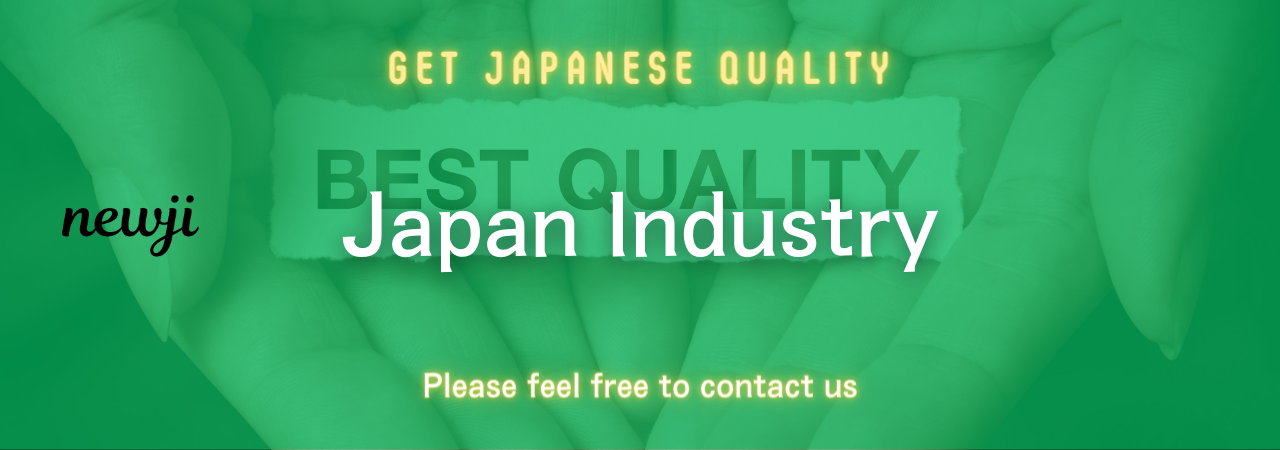
目次
Understanding Poka-Yoke
Poka-yoke is a Japanese term that means “mistake-proofing” or “inadvertent error prevention.”
It is a technique used to eliminate errors by designing a process that is incapable of producing a defect.
In the context of equipment maintenance, this means creating steps and systems that help mid-level employees perform their tasks accurately and efficiently, minimizing the likelihood of errors.
The Importance of Poka-Yoke in Maintenance
In equipment maintenance, even minor errors can lead to significant problems, such as equipment breakdowns, increased costs, and safety hazards.
Implementing poka-yoke methods helps ensure that maintenance tasks are performed correctly the first time.
By adopting these techniques, employees can focus more on preventing errors rather than fixing them after they occur, leading to a more efficient and safe working environment.
Types of Poka-Yoke Techniques
There are several types of poka-yoke techniques that can be applied individually or in combination to prevent errors during maintenance activities.
Understanding and mastering these techniques can greatly enhance the quality of work performed by maintenance staff.
1. Physical Poka-Yoke
Physical poka-yoke involves the use of equipment or tools designed to prevent incorrect actions.
For instance, maintenance tools can be built with unique shapes or sizes that only fit specific parts of the equipment, reducing the chance of using the wrong tool for a task.
This method both guides the employee and restricts incorrect actions.
2. Visual Poka-Yoke
Visual poka-yoke uses clear labels, color coding, and simple visual cues to prompt correct actions.
In a maintenance setting, parts and tools can be color-coded based on their function or the equipment they are used on.
This makes it easier for employees to quickly identify the correct components, reducing mix-ups and ensuring that the right procedures are followed.
3. Procedural Poka-Yoke
Procedural poka-yoke involves establishing standard operating procedures that make it difficult to deviate from correct processes.
This can include checklists, step-by-step guides, and automated reminders that ensure each task is completed accurately.
For instance, a checklist can be used to verify that all maintenance steps have been performed before an equipment is put back into operation.
4. Sensory Poka-Yoke
Sensory poka-yoke makes use of signals like lights, sounds, or vibrations to alert workers when an error is about to occur.
In equipment maintenance, sensors can be installed that activate alarms if a part is not properly secured, prompting the employee to recheck their work before proceeding further.
Steps to Implement Poka-Yoke in Maintenance
To effectively implement poka-yoke in an equipment maintenance department, certain strategies should be followed.
These steps offer a structured approach to mastering mistake-proofing techniques.
1. Identify Common Errors
Before implementing poka-yoke, it’s crucial to identify the most frequent and impactful errors that occur during maintenance.
Analyze past incidents and gather feedback from employees to get a clear understanding of where the process breaks down.
This information will guide the selection of appropriate poka-yoke techniques.
2. Involve the Team
Mid-level employees should be actively involved in the development and integration of poka-yoke methods.
Their firsthand experience and insights are invaluable in identifying potential pitfalls and suggesting practical solutions.
Encouraging team participation fosters a culture of continuous improvement and accountability.
3. Design Poka-Yoke Solutions
Based on identified errors and team input, design practical poka-yoke solutions that align with the equipment and processes in use.
Prioritize simplicity to ensure that solutions are easy to understand and adopt, and consider creating prototypes to test their effectiveness before full-scale implementation.
4. Train and Educate
Once poka-yoke solutions are designed, provide thorough training to ensure that all employees understand how to use them effectively.
Ongoing education sessions should be held to reinforce the principles of poka-yoke and to share updates or improvements to the techniques.
5. Monitor and Evaluate
After implementing poka-yoke strategies, monitor their application and effectiveness regularly.
Collect data on error rates and the functionality of the new processes.
Feedback from the team can highlight areas for further refinement, allowing the system to evolve and remain efficient.
Benefits of Mastering Poka-Yoke Techniques
For mid-level employees in equipment maintenance, mastering poka-yoke techniques offers significant benefits.
These range from increased personal efficiency to broader organizational gains.
1. Enhanced Performance
By using poka-yoke techniques, employees become more adept at performing their tasks without errors.
This leads to a more smoothly running maintenance department, increased reliability of equipment, and a more satisfying work experience for employees.
2. Cost Reduction
Reducing errors can significantly lower maintenance costs.
Unplanned downtime due to mistakes can be costly in terms of repairs and lost productivity.
Poka-yoke helps ensure that equipment functions optimally, reducing the need for repeated fixes and minimizing costly downtime.
3. Improved Safety
Fewer errors in maintenance lead to a safer working environment.
Well-maintained equipment functions correctly, minimizing the risk of accidents.
Employees can focus on performing their tasks without the added stress of possible mistakes, knowing that poka-yoke methods are in place to support them.
4. Organizational Efficiency
By integrating poka-yoke techniques effectively, the entire organization benefits from streamlined processes and improved equipment reliability.
A maintenance department that operates without errors contributes to greater overall efficiency, enhancing the performance of all departments reliant on the equipment’s functionality.
Mastering the art of poka-yoke techniques in the equipment maintenance department empowers mid-level employees to contribute significantly to error-free operations.
With the right mindset and tools, these techniques help create a dependable maintenance process, ensuring equipment longevity, reducing costs, and prioritizing safety.
By continuing to learn and adapt, employees ensure that poka-yoke remains a core component of their work strategy.
資料ダウンロード
QCD調達購買管理クラウド「newji」は、調達購買部門で必要なQCD管理全てを備えた、現場特化型兼クラウド型の今世紀最高の購買管理システムとなります。
ユーザー登録
調達購買業務の効率化だけでなく、システムを導入することで、コスト削減や製品・資材のステータス可視化のほか、属人化していた購買情報の共有化による内部不正防止や統制にも役立ちます。
NEWJI DX
製造業に特化したデジタルトランスフォーメーション(DX)の実現を目指す請負開発型のコンサルティングサービスです。AI、iPaaS、および先端の技術を駆使して、製造プロセスの効率化、業務効率化、チームワーク強化、コスト削減、品質向上を実現します。このサービスは、製造業の課題を深く理解し、それに対する最適なデジタルソリューションを提供することで、企業が持続的な成長とイノベーションを達成できるようサポートします。
オンライン講座
製造業、主に購買・調達部門にお勤めの方々に向けた情報を配信しております。
新任の方やベテランの方、管理職を対象とした幅広いコンテンツをご用意しております。
お問い合わせ
コストダウンが利益に直結する術だと理解していても、なかなか前に進めることができない状況。そんな時は、newjiのコストダウン自動化機能で大きく利益貢献しよう!
(Β版非公開)