- お役立ち記事
- For new employees in the equipment management department of the steel industry! Key points for blast furnace temperature control and abnormality detection
For new employees in the equipment management department of the steel industry! Key points for blast furnace temperature control and abnormality detection
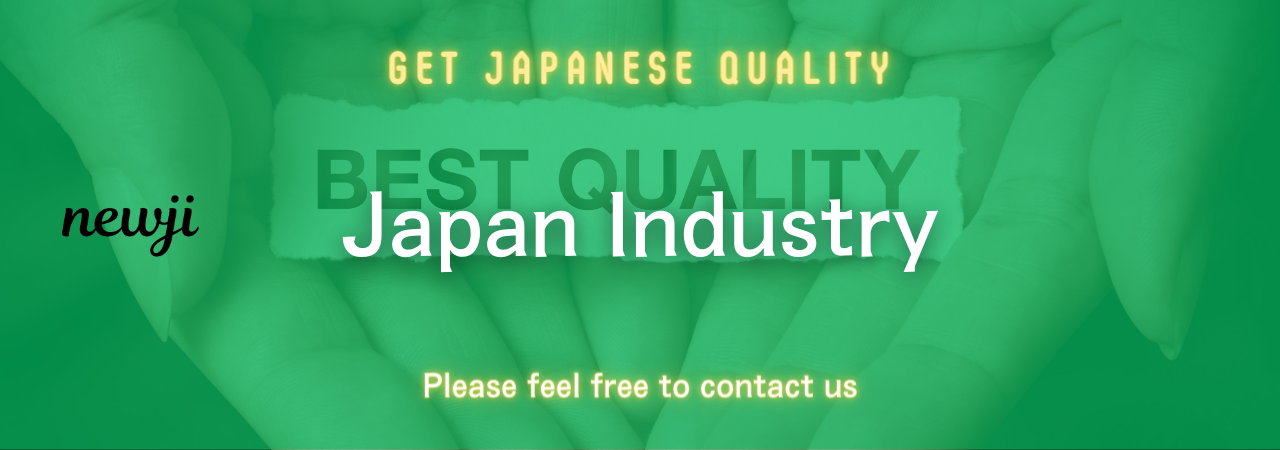
目次
Understanding Blast Furnace Operations
To effectively control the temperature of a blast furnace and detect abnormalities, it’s crucial to first understand how a blast furnace operates.
Blast furnaces play a vital role in the steel manufacturing process, as they transform raw materials into molten iron, which is then processed into steel.
The process involves several materials, including iron ore, coke, and limestone, which are layered in the furnace and chemically reacted with hot air.
The end goal is to produce high-quality molten iron, and temperature control is paramount in achieving this.
Importance of Temperature Control
Temperature control in a blast furnace is essential for several reasons.
Firstly, maintaining optimal temperature ensures efficient chemical reactions.
This not only improves the quality of the molten iron but also optimizes fuel consumption, making the process more cost-effective.
Secondly, precise temperature management helps in the reduction of pollutants and ensures that the furnace operates within environmental regulations.
Proper control also minimizes wear and tear on the equipment, reducing downtime and maintenance costs.
Key Techniques for Temperature Control
Understanding the techniques for controlling temperature in a blast furnace is critical for new employees in the equipment management department.
Input Material Management
The quality and consistency of the input materials, such as iron ore and coke, directly affect furnace temperature.
Ensuring these materials meet specified standards is crucial.
Moisture content in the raw materials can cause fluctuations in temperature, so they should be kept as consistent as possible.
Blast Temperature Regulation
Regulating the temperature of the blast air (hot air blown into the furnace) is one of the most effective ways to control furnace temperature.
This can be achieved by adjusting the combustion parameters or using heat exchangers to preheat the air to the desired temperature before it enters the furnace.
Real-time Monitoring Systems
Installing real-time temperature monitoring sensors inside the blast furnace provides instant feedback.
These sensors help track temperature changes accurately, allowing operators to make timely adjustments.
Advanced systems may include predictive analytics, which can forecast potential issues based on current data trends.
Detecting Abnormalities in Blast Furnace Operations
Detecting abnormalities early can prevent larger operational issues and ensure smooth production processes.
Here are a few strategies for effective abnormality detection.
Monitoring Sensor Data
Regularly monitoring data from sensors can help detect abnormalities such as sudden temperature spikes or drops.
Operators should be trained to understand what the normal operating ranges are and be able to recognize deviations quickly.
Analyzing Pressure Changes
Sudden changes in the internal pressure of the furnace can indicate potential problems, such as blockages or leaks.
By maintaining optimal pressure levels, you can ensure consistent temperature and efficient operation.
Regular Equipment Inspection
Routine inspections of the furnace and associated equipment can prevent failures.
It’s important to establish a regular inspection schedule, including checking for signs of wear or damage that might affect performance.
This can include reviewing refractory linings, checking for cracks, or other physical damages.
Best Practices for New Employees
As a new employee in the equipment management department, here are some best practices to keep in mind.
Comprehensive Training
Engage in any training opportunities provided by your employer to understand better the specifics of the equipment you’ll be working with.
This knowledge will help you interpret sensor data and understand when it’s necessary to take action.
Team Communication
Open communication with your team members is vital.
Discuss any abnormalities or insights you notice with experienced colleagues.
Their feedback can be invaluable in learning how to resolve issues effectively.
Continuous Learning
Stay informed about the latest advancements in furnace technology and temperature control methodologies.
Reading industry publications and attending workshops can enhance your understanding and skill set.
Conclusion
Temperature control and anomaly detection in blast furnace operations are critical responsibilities for anyone in the steel industry.
Understanding how a furnace works, combined with employing effective monitoring and management strategies, ensures seamless production.
By following these key techniques and best practices, new employees can become proficient in their roles and contribute significantly to their team’s success.
資料ダウンロード
QCD調達購買管理クラウド「newji」は、調達購買部門で必要なQCD管理全てを備えた、現場特化型兼クラウド型の今世紀最高の購買管理システムとなります。
ユーザー登録
調達購買業務の効率化だけでなく、システムを導入することで、コスト削減や製品・資材のステータス可視化のほか、属人化していた購買情報の共有化による内部不正防止や統制にも役立ちます。
NEWJI DX
製造業に特化したデジタルトランスフォーメーション(DX)の実現を目指す請負開発型のコンサルティングサービスです。AI、iPaaS、および先端の技術を駆使して、製造プロセスの効率化、業務効率化、チームワーク強化、コスト削減、品質向上を実現します。このサービスは、製造業の課題を深く理解し、それに対する最適なデジタルソリューションを提供することで、企業が持続的な成長とイノベーションを達成できるようサポートします。
オンライン講座
製造業、主に購買・調達部門にお勤めの方々に向けた情報を配信しております。
新任の方やベテランの方、管理職を対象とした幅広いコンテンツをご用意しております。
お問い合わせ
コストダウンが利益に直結する術だと理解していても、なかなか前に進めることができない状況。そんな時は、newjiのコストダウン自動化機能で大きく利益貢献しよう!
(Β版非公開)