- お役立ち記事
- For processing engineers in the precision machinery industry! High-precision machining techniques using multi-axis machining centers
For processing engineers in the precision machinery industry! High-precision machining techniques using multi-axis machining centers
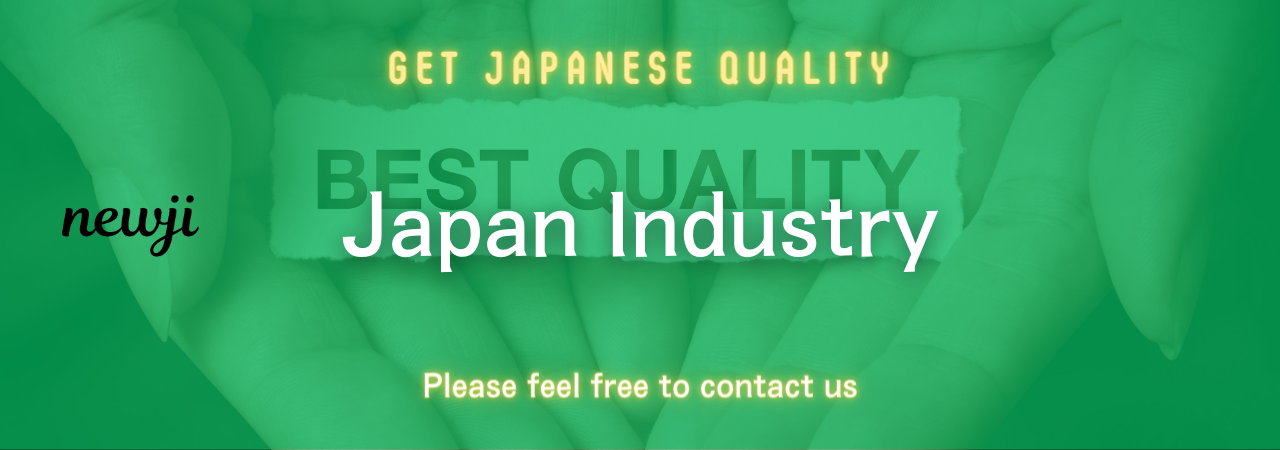
目次
Understanding Multi-Axis Machining Centers
Multi-axis machining centers are powerful tools in the precision machinery industry, allowing for the creation of complex and intricate components with remarkable accuracy.
These advanced machines have multiple axes of motion, which means they can move in various directions simultaneously.
This capability significantly enhances the machining process, providing engineers with the flexibility to produce parts with complex geometries that would be difficult or impossible to achieve with traditional machining methods.
The precision and efficiency offered by multi-axis machining centers make them indispensable in industries such as aerospace, automotive, and medical device manufacturing.
The Basic Concepts
Before diving into high-precision machining techniques, it’s crucial to understand the basic concepts of multi-axis machining centers.
A typical setup may include three to five axes of motion, with some machines boasting even more.
The axes involved often include the traditional X, Y, and Z axes, with additional rotational axes such as A, B, and C.
These additional axes allow the machining center to tilt and rotate the workpiece or tool, providing even greater versatility.
The ability to manipulate the workpiece or tool from multiple angles allows for continuous machining without needing to reposition the component manually.
This saves time and improves accuracy, as there is less chance for human error during the repositioning process.
High-Precision Machining Techniques
Incorporating high-precision machining techniques is vital for maximizing the benefits of multi-axis machining centers.
These techniques help ensure that the final product meets stringent quality standards and requirements.
1. Tool Selection and Management
Choosing the right tools is crucial for achieving high-precision results.
Different materials and machining tasks require specific tools to ensure optimal performance and longevity.
Managing these tools effectively is also essential, and it requires regular inspection and maintenance to keep them in peak condition.
Implementing a proper tool management system can help minimize tool wear and reduce the risk of tool failure during the machining process.
2. Advanced CAD/CAM Software
The use of advanced CAD/CAM software is integral to multi-axis machining.
These software tools enable engineers to design complex components and generate detailed machining instructions.
By simulating the machining process, CAD/CAM software can identify potential issues and optimize the tool path for maximum efficiency and precision.
This not only reduces the risk of errors but also shortens the production cycle times.
3. Workpiece Stabilization
Stabilizing the workpiece during machining is another critical factor in achieving high precision.
Proper workholding techniques ensure that the component remains firmly secured throughout the process, preventing vibrations and distortions.
This is especially important for delicate or intricate parts, where even minor movements can lead to significant deviations from intended specifications.
Utilizing high-quality fixtures and clamps can help maintain the stability of the workpiece, ensuring precise results.
4. Accurate Machine Calibration
Regular calibration is essential for maintaining the accuracy of a multi-axis machining center.
With time and use, machines may experience wear and tear, leading to potential deviations from desired specifications.
Conducting routine maintenance checks and calibrating the machine periodically helps prevent such issues.
This ensures the machine continues to function at optimal performance levels, delivering precise and accurate results consistently.
5. Monitoring and Quality Control
Implementing stringent monitoring and quality control measures throughout the machining process is vital for ensuring precision.
Using techniques like in-process quality control (IPQC) allows for real-time inspections and adjustments.
This helps identify any discrepancies early on and makes necessary corrections promptly.
Conducting post-process inspections further ensures that the finished component meets all design and quality requirements.
Benefits of High-Precision Machining with Multi-Axis Centers
High-precision machining with multi-axis centers offers numerous advantages to processing engineers.
The ability to produce highly complex parts with reduced manual intervention not only improves productivity but also enhances overall quality.
Here are some benefits that result from utilizing these techniques:
Enhanced Accuracy and Consistency
High-precision machining delivers components with extremely tight tolerances, meeting the demanding standards of various industries.
This level of precision enhances product functionality and performance, which is essential in applications like aerospace and medical devices, where precision is paramount.
Furthermore, the consistency achieved through high-precision machining ensures that each part adheres to the required specifications.
Increased Efficiency and Productivity
Multi-axis machining centers significantly reduce the need for manual interventions, eliminating potential sources of error and decreasing production cycle times.
The ability to complete multiple operations simultaneously minimizes downtime, leading to faster turnaround times and increased throughput.
This efficiency translates to cost savings and a competitive edge for manufacturers in the precision machinery industry.
Flexibility and Versatility
The advanced capabilities of multi-axis machining centers provide engineers with the flexibility to tackle complex projects that would be highly challenging with traditional machining methods.
These machines can handle a wide range of materials and designs, enabling production of intricate parts for diverse industries.
This versatility allows manufacturers to expand their service offerings and cater to a broader market.
Conclusion
In the precision machinery industry, high-precision machining techniques using multi-axis machining centers are essential for producing complex, high-quality components.
By incorporating best practices such as tool management, advanced software, and stringent quality control, processing engineers can ensure their machines deliver exceptional results.
As a result, manufacturers can benefit from improved accuracy, efficiency, and flexibility, ultimately achieving a competitive advantage in their respective fields.
資料ダウンロード
QCD調達購買管理クラウド「newji」は、調達購買部門で必要なQCD管理全てを備えた、現場特化型兼クラウド型の今世紀最高の購買管理システムとなります。
ユーザー登録
調達購買業務の効率化だけでなく、システムを導入することで、コスト削減や製品・資材のステータス可視化のほか、属人化していた購買情報の共有化による内部不正防止や統制にも役立ちます。
NEWJI DX
製造業に特化したデジタルトランスフォーメーション(DX)の実現を目指す請負開発型のコンサルティングサービスです。AI、iPaaS、および先端の技術を駆使して、製造プロセスの効率化、業務効率化、チームワーク強化、コスト削減、品質向上を実現します。このサービスは、製造業の課題を深く理解し、それに対する最適なデジタルソリューションを提供することで、企業が持続的な成長とイノベーションを達成できるようサポートします。
オンライン講座
製造業、主に購買・調達部門にお勤めの方々に向けた情報を配信しております。
新任の方やベテランの方、管理職を対象とした幅広いコンテンツをご用意しております。
お問い合わせ
コストダウンが利益に直結する術だと理解していても、なかなか前に進めることができない状況。そんな時は、newjiのコストダウン自動化機能で大きく利益貢献しよう!
(Β版非公開)