- お役立ち記事
- Basics of application and development of nanocomposite materials that new employees in the R&D department of the precision machinery industry should know
Basics of application and development of nanocomposite materials that new employees in the R&D department of the precision machinery industry should know
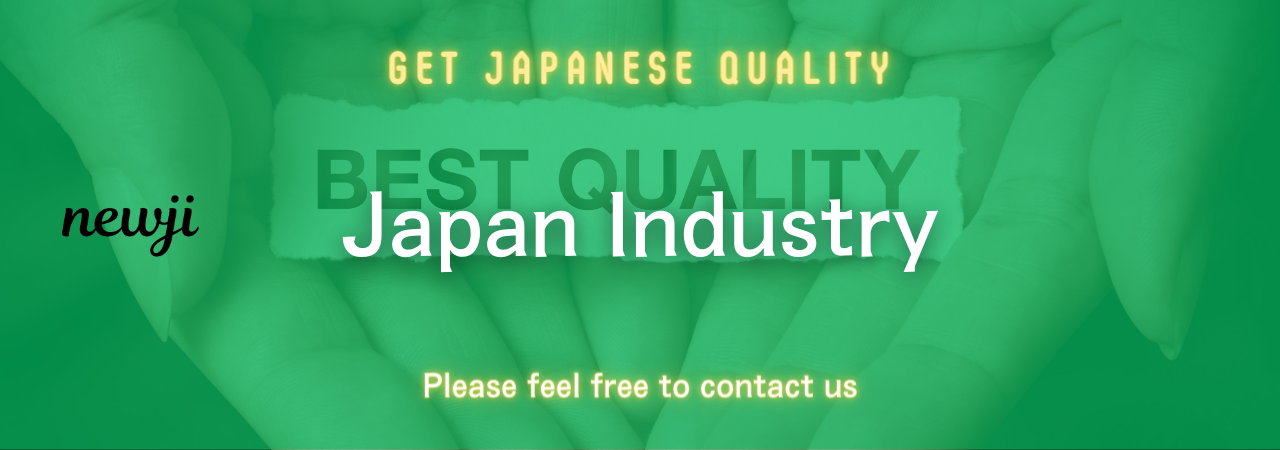
Nanocomposite materials are an exciting and rapidly evolving field in the precision machinery industry.
For new employees in the research and development (R&D) department, understanding the basics of these materials is crucial for advancing technology and creating innovative solutions.
In this article, we will explore what nanocomposite materials are, their applications, and the development process to give you a solid foundation in this area.
目次
What Are Nanocomposite Materials?
Nanocomposite materials are composites where one of the phases has at least one dimension in the nanometer range (1-100 nm).
These materials combine nanoparticles with traditional materials to enhance their properties.
The integration at the nanoscale can lead to significant improvements in mechanical, thermal, electrical, and barrier properties.
Nanocomposites are made by integrating materials like polymers, metals, and ceramics with nanoparticles such as carbon nanotubes, clay, silica, and metal oxides.
This combination can yield materials with superior performance compared to their traditional counterparts.
Types of Nanocomposite Materials
Nanocomposite materials can be classified into three main categories based on their matrix materials:
1. **Polymer Nanocomposites**: These are composites where nanosized fillers like nanoclays, carbon nanotubes, or nanoparticles are embedded in polymer matrices.
2. **Metal Matrix Nanocomposites (MMNCs)**: Here, metal matrices are reinforced with nanoscale materials to improve mechanical properties and strength-to-weight ratio.
3. **Ceramic Matrix Nanocomposites (CMNCs)**: These involve ceramics embedded with nanoparticles to enhance toughness and thermal resistance.
Applications of Nanocomposite Materials in the Precision Machinery Industry
Nanocomposite materials have diverse applications in the precision machinery industry.
Their ability to improve properties and performance makes them suitable for several critical uses.
Enhanced Mechanical Properties
Nanocomposites can significantly enhance mechanical properties such as strength, stiffness, and toughness.
For instance, in the automotive sector, polymer nanocomposites are used to create lightweight yet strong components.
This can lead to fuel efficiency and reduced emissions.
Improved Thermal Stability
In high-temperature applications, nanocomposites provide excellent thermal stability.
Ceramic matrix nanocomposites are commonly used in cutting tools, furnace parts, and engine components, where heat resistance is vital.
Electrical Conductivity
Metal matrix and polymer nanocomposites can be engineered to improve electrical conductivity.
This is useful for applications in electronics and communication devices, where efficient conductivity is required.
Environmental Barrier Properties
Nanocomposites can offer superior barrier properties, protecting components from environmental factors like moisture, gas, and chemicals.
This quality is particularly beneficial in protective coatings and packaging.
The Development Process of Nanocomposite Materials
Developing nanocomposite materials involves several key steps, from conceptualization to the final product.
Each phase requires careful attention to detail to achieve the desired material properties.
Research and Design
The first step in developing nanocomposites is understanding the specific requirements and constraints of the intended application.
This involves selecting appropriate matrix and nanoparticle materials and determining the desired enhancements.
Modelling and simulations can help predict how these materials will behave when combined.
Material Synthesis and Fabrication
Once the design is finalized, the synthesis of nanoparticles and matrix materials begins.
Common methods include sol-gel processing, melt compounding, and in situ polymerization.
Fabrication techniques, such as extrusion or injection molding, are employed to create the final nanocomposite.
Characterization and Testing
The next phase involves characterizing the nanocomposites to examine their structural and mechanical properties.
Techniques like scanning electron microscopy (SEM), transmission electron microscopy (TEM), and X-ray diffraction (XRD) are used to analyze the material’s structure and morphology.
Testing is conducted to determine whether the nanocomposite meets the initial design requirements.
Application and Performance Evaluation
After successful characterization and testing, the nanocomposite materials are applied to the intended areas or components.
Further testing is done to assess their real-world performance under operational conditions.
Feedback from this stage is crucial for making any necessary adjustments or improvements.
Challenges in Developing Nanocomposite Materials
While the benefits of nanocomposites are many, their development presents several challenges that new R&D employees should be aware of.
Dispersion of Nanoparticles
Achieving uniform dispersion of nanoparticles within the matrix is one of the key challenges.
Poor dispersion can lead to aggregation, which negatively affects the materials’ properties.
Research and experimentation with various dispersion techniques are essential to overcome this hurdle.
Cost and Scalability
The cost of producing nanocomposites can be high, mainly due to the expense of nanomaterials and complex manufacturing processes.
Scalability is another concern, as processes have to be efficiently scaled up from the lab to industrial levels without compromising quality.
Health and Safety Concerns
Working with nanoparticles poses potential health and safety risks, requiring stringent regulations and handling procedures in R&D environments.
Ensuring safe production and application of nanocomposites is essential for long-term industry and societal benefits.
Conclusion
Nanocomposite materials hold immense potential for transforming the precision machinery industry with their enhanced mechanical, thermal, and electrical properties.
For new R&D employees, understanding their basic principles, applications, and development processes is fundamental.
While the journey of creating nanocomposites comes with challenges, it is also filled with opportunities for innovation and technological advancement.
With the knowledge and insights gained from this foundational guide, you are well on your way to contributing to the exciting world of nanocomposite materials.
資料ダウンロード
QCD調達購買管理クラウド「newji」は、調達購買部門で必要なQCD管理全てを備えた、現場特化型兼クラウド型の今世紀最高の購買管理システムとなります。
ユーザー登録
調達購買業務の効率化だけでなく、システムを導入することで、コスト削減や製品・資材のステータス可視化のほか、属人化していた購買情報の共有化による内部不正防止や統制にも役立ちます。
NEWJI DX
製造業に特化したデジタルトランスフォーメーション(DX)の実現を目指す請負開発型のコンサルティングサービスです。AI、iPaaS、および先端の技術を駆使して、製造プロセスの効率化、業務効率化、チームワーク強化、コスト削減、品質向上を実現します。このサービスは、製造業の課題を深く理解し、それに対する最適なデジタルソリューションを提供することで、企業が持続的な成長とイノベーションを達成できるようサポートします。
オンライン講座
製造業、主に購買・調達部門にお勤めの方々に向けた情報を配信しております。
新任の方やベテランの方、管理職を対象とした幅広いコンテンツをご用意しております。
お問い合わせ
コストダウンが利益に直結する術だと理解していても、なかなか前に進めることができない状況。そんな時は、newjiのコストダウン自動化機能で大きく利益貢献しよう!
(Β版非公開)