- お役立ち記事
- A must-see for production engineers who manufacture rotary tables for automobile production lines! Material selection for precision and durability
A must-see for production engineers who manufacture rotary tables for automobile production lines! Material selection for precision and durability
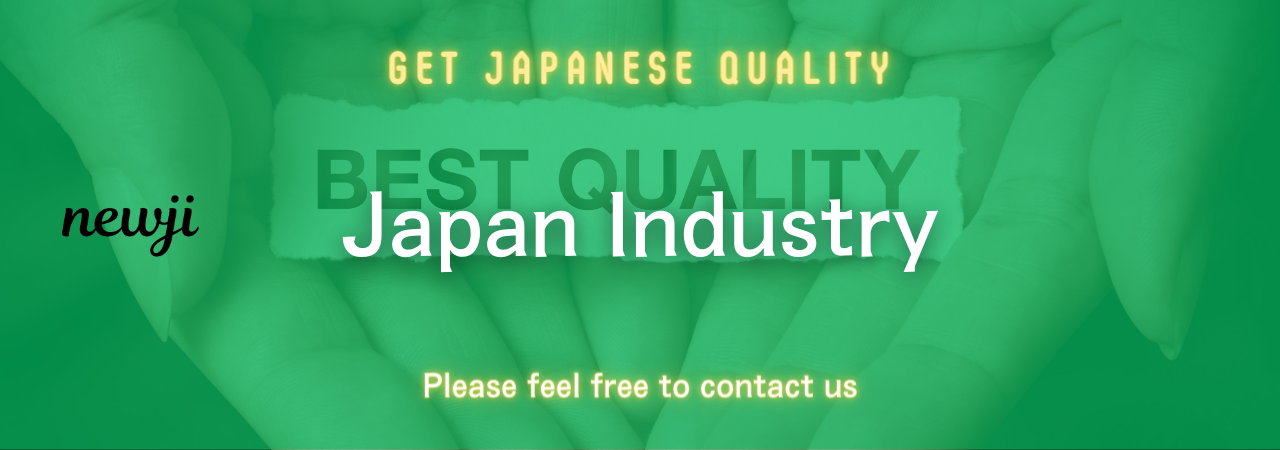
目次
Understanding Rotary Tables in Automobile Production
Rotary tables play a crucial role in automobile production lines.
They are essential for precise machining and assembling various car parts.
Production engineers must ensure that these tables are both accurate and durable to withstand the rigorous demands of manufacturing.
Rotary tables allow components to move and rotate efficiently during the assembly or machining process.
In doing so, they help to streamline operations and enhance productivity.
Given their importance, selecting the right material for constructing rotary tables is a critical decision.
It impacts their performance, longevity, and overall efficiency in production work.
Why Material Selection Matters
Choosing the right material for rotary tables is not just about finding something that is sturdy.
It involves considering several factors including temperature resistance, stress tolerance, and wear resistance.
The material must be able to maintain its shape and function over repeated cycles and extended periods.
Improper material selection can lead to increased downtime, maintenance costs, and reduced precision in the manufacturing process.
This can ultimately affect the quality of the automobiles being produced.
Key Factors in Material Selection
Precision and Accuracy
Precision in rotary tables is paramount.
Achieving high levels of accuracy means that the material must have dimensional stability and low thermal expansion.
Materials that maintain their shape and size even under high temperatures are ideal for ensuring rotary tables function smoothly.
Durability and Wear Resistance
Wear resistance refers to the material’s ability to withstand erosion or degradation over time.
Durable materials reduce the frequency of replacements and repairs, which is essential for maintaining continual production.
Materials like hardened steel or tungsten carbide are known for their exceptional wear resistance.
These materials can handle the high-speed interfaces and friction that occurs during operations, making them excellent choices for rotary tables.
Corrosion Resistance
In environments where exposure to lubricants or cooling liquids is common, corrosion resistance is another key consideration.
Materials that are prone to rust or corrosion can compromise the rotary table’s precision and function.
Stainless steel and other corrosion-resistant alloys are often used to address such issues.
Weight Considerations
The weight of the rotary table affects the ease of handling and the speed at which it can be moved during production.
Lighter materials such as aluminum or certain composites can be considered for applications where rapid motion is necessary.
However, they must also balance the trade-off between weight and strength.
Common Materials Used in Rotary Tables
Cast Iron
Cast iron has traditionally been used in the manufacture of rotary tables because of its excellent damping properties.
It reduces vibrations during machining, enhancing precision.
However, it is heavier and may not be suitable for applications requiring rapid movement.
Steel
Steel, particularly hardened steel, provides a robust option due to its strength and durability.
It is relatively resistant to wear and can be treated to resist corrosion.
Steel offers a good balance between weight and resilience, making it a popular choice in various applications.
Aluminum
Aluminum is valued for its lightweight properties, which make it ideal for rotary tables that require swift maneuverability.
It offers good corrosion resistance but might not provide the durability needed for heavy-duty applications without proper treatment or reinforcement.
Composites
Newer composite materials combine different elements to achieve high-strength, lightweight properties.
These materials are designed to withstand specific stresses encountered in the production environment, although they often come at a higher cost.
Balancing Cost and Performance
While it can be tempting to opt for the most durable and advanced material available, cost is an important factor in production engineering.
The goal is to find a material that meets performance requirements while also fitting within budget constraints.
Evaluating the total cost of ownership is essential.
This includes considering the cost of materials, maintenance, and potential downtime caused by material failure.
In some cases, investing in higher-quality materials upfront can translate into long-term savings.
Conclusion: Making the Right Choice
Material selection for rotary tables in automobile production lines is a critical decision that affects both production efficiency and product quality.
By taking into account factors such as precision, durability, corrosion resistance, and weight, production engineers can make informed choices that ensure reliable and efficient operations.
Ultimately, the right material is one that aligns with the specific needs and conditions of the manufacturing process.
As technology advances, ongoing research and development may continue to introduce new materials that can further optimize the performance of rotary tables in automobile production.
資料ダウンロード
QCD調達購買管理クラウド「newji」は、調達購買部門で必要なQCD管理全てを備えた、現場特化型兼クラウド型の今世紀最高の購買管理システムとなります。
ユーザー登録
調達購買業務の効率化だけでなく、システムを導入することで、コスト削減や製品・資材のステータス可視化のほか、属人化していた購買情報の共有化による内部不正防止や統制にも役立ちます。
NEWJI DX
製造業に特化したデジタルトランスフォーメーション(DX)の実現を目指す請負開発型のコンサルティングサービスです。AI、iPaaS、および先端の技術を駆使して、製造プロセスの効率化、業務効率化、チームワーク強化、コスト削減、品質向上を実現します。このサービスは、製造業の課題を深く理解し、それに対する最適なデジタルソリューションを提供することで、企業が持続的な成長とイノベーションを達成できるようサポートします。
オンライン講座
製造業、主に購買・調達部門にお勤めの方々に向けた情報を配信しております。
新任の方やベテランの方、管理職を対象とした幅広いコンテンツをご用意しております。
お問い合わせ
コストダウンが利益に直結する術だと理解していても、なかなか前に進めることができない状況。そんな時は、newjiのコストダウン自動化機能で大きく利益貢献しよう!
(Β版非公開)