- お役立ち記事
- Preventing equipment breakdowns with “planned maintenance”—How to create a maintenance system that management requires on-site
Preventing equipment breakdowns with “planned maintenance”—How to create a maintenance system that management requires on-site
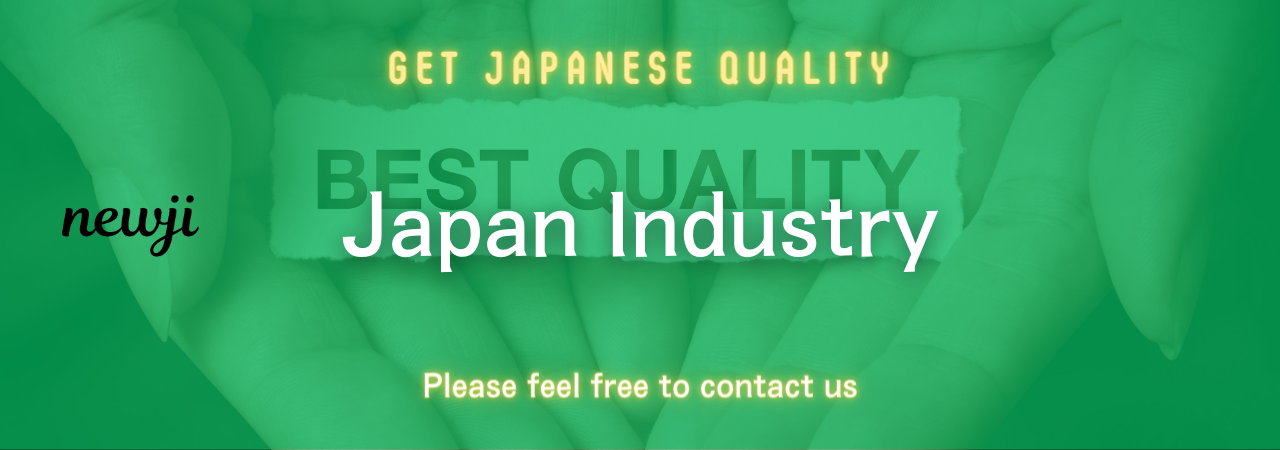
目次
Understanding Planned Maintenance
Planned maintenance is a strategic approach aimed at preventing equipment breakdowns and ensuring smooth operations on-site.
This method involves scheduling regular maintenance tasks based on time intervals or equipment usage levels.
By doing so, companies can avoid unexpected failures and costly repairs.
The concept of planned maintenance revolves around meticulous planning and scheduling.
It requires identifying critical equipment, determining maintenance needs, and assigning resources to carry out the tasks.
This proactive approach not only prolongs the life of machinery but also enhances productivity and safety.
Benefits of Planned Maintenance
Implementing a planned maintenance system offers numerous benefits for businesses across industries.
Firstly, it reduces downtime significantly by catching potential issues before they become major problems.
This results in increased productivity and improved operational efficiency.
Secondly, planned maintenance extends the lifespan of equipment.
Regular checks and timely repairs prevent wear and tear, allowing machines to function optimally for longer periods.
This saves costs in the long run as the need for replacements or extensive repairs diminishes.
Another advantage is enhanced safety.
Planned maintenance ensures that all equipment is in good working condition, minimizing the chances of accidents or malfunctions that could harm employees.
Additionally, it aids in compliance with industry regulations.
By adhering to scheduled maintenance, companies can meet safety and quality standards, avoiding penalties or lawsuits.
Steps to Create an Effective Maintenance System
Creating a maintenance system that aligns with management’s requirements involves several key steps.
Understanding your organization’s needs and equipment is crucial in developing a successful maintenance plan.
1. Assess Equipment and Resources
Begin by assessing all the equipment used in your operations.
Identify critical machinery that directly affects production.
Evaluate the condition, age, and previous maintenance history of each piece of equipment.
Consider the resources available, including manpower, budget, and tools.
These factors will influence the scope and frequency of maintenance tasks.
2. Develop a Maintenance Schedule
Once you have assessed the equipment, develop a comprehensive maintenance schedule.
This schedule should include routine inspections, lubrication, calibration, cleaning, and replacement of worn-out parts.
The frequency of maintenance tasks will depend on the usage intensity and manufacturer’s recommendations.
It is essential to balance the schedule so that it does not disrupt operations unnecessarily.
3. Allocate Responsibilities
Clearly define roles and responsibilities for each maintenance task.
Assign skilled personnel or teams dedicated to carrying out maintenance activities.
Provide proper training to the staff to ensure they understand the importance of planned maintenance and can execute their tasks efficiently.
4. Monitor and Record Maintenance Activities
Implement a system to monitor and record all maintenance activities.
Keeping detailed records allows you to track the performance and condition of each piece of equipment over time.
Use maintenance logs, software, or digital tools to store this information.
Analyzing these records will help you identify patterns, anticipate issues, and optimize maintenance strategies.
5. Evaluate and Adjust the Plan
Regularly review and evaluate the effectiveness of your maintenance system.
Seek feedback from employees and management to identify areas for improvement.
Be flexible in adjusting the maintenance plan based on the data collected and changing organizational needs.
Continuous improvement is vital to the success of planned maintenance.
Challenges in Implementing Planned Maintenance
While planned maintenance offers numerous benefits, there are challenges that organizations may face during implementation.
One challenge is the initial cost and resource allocation.
Setting up the system requires investment in training, tools, and possibly new hires.
However, these upfront costs are typically outweighed by savings in the long term.
Resistance to change is another common obstacle.
Employees might be accustomed to a reactive maintenance approach and skeptical about adopting a preventive strategy.
Effective communication and demonstrating the benefits of planned maintenance are crucial to overcoming this barrier.
Additionally, accurately forecasting maintenance needs can be difficult.
It requires a thorough understanding of equipment and may involve learning curves as the system is fine-tuned.
The Role of Technology in Planned Maintenance
Technology plays a significant role in enhancing planned maintenance systems.
With the advancement of digital tools and software, managing maintenance tasks has become more efficient and accurate.
Predictive Maintenance Tools
Predictive maintenance tools utilize data analytics, sensors, and machine learning to predict when equipment might fail.
These insights allow organizations to schedule maintenance activities before problems arise, minimizing downtime and maximizing efficiency.
Maintenance Management Software
Maintenance management software aids in scheduling, tracking, and documenting maintenance activities.
It provides a centralized platform for managing all tasks, streamlining communication, and ensuring accountability.
These technologies not only simplify maintenance management but also contribute to data-driven decision-making in maintenance strategies.
Conclusion
Planned maintenance is a vital component of modern business operations, ensuring that equipment runs efficiently while minimizing downtime and costs.
By understanding its benefits, implementing a well-structured system, and leveraging technology, organizations can develop a maintenance approach that meets management’s needs and maintains operational excellence on-site.
Proactive planning, regular evaluation, and adaptation to new techniques are keys to success in preventing equipment breakdowns and achieving a seamless production process.
資料ダウンロード
QCD調達購買管理クラウド「newji」は、調達購買部門で必要なQCD管理全てを備えた、現場特化型兼クラウド型の今世紀最高の購買管理システムとなります。
ユーザー登録
調達購買業務の効率化だけでなく、システムを導入することで、コスト削減や製品・資材のステータス可視化のほか、属人化していた購買情報の共有化による内部不正防止や統制にも役立ちます。
NEWJI DX
製造業に特化したデジタルトランスフォーメーション(DX)の実現を目指す請負開発型のコンサルティングサービスです。AI、iPaaS、および先端の技術を駆使して、製造プロセスの効率化、業務効率化、チームワーク強化、コスト削減、品質向上を実現します。このサービスは、製造業の課題を深く理解し、それに対する最適なデジタルソリューションを提供することで、企業が持続的な成長とイノベーションを達成できるようサポートします。
オンライン講座
製造業、主に購買・調達部門にお勤めの方々に向けた情報を配信しております。
新任の方やベテランの方、管理職を対象とした幅広いコンテンツをご用意しております。
お問い合わせ
コストダウンが利益に直結する術だと理解していても、なかなか前に進めることができない状況。そんな時は、newjiのコストダウン自動化機能で大きく利益貢献しよう!
(Β版非公開)