- お役立ち記事
- A must-see for new employees in the equipment management department of the precision machinery industry! Basics of lubrication management and wear diagnosis of mechanical parts
A must-see for new employees in the equipment management department of the precision machinery industry! Basics of lubrication management and wear diagnosis of mechanical parts
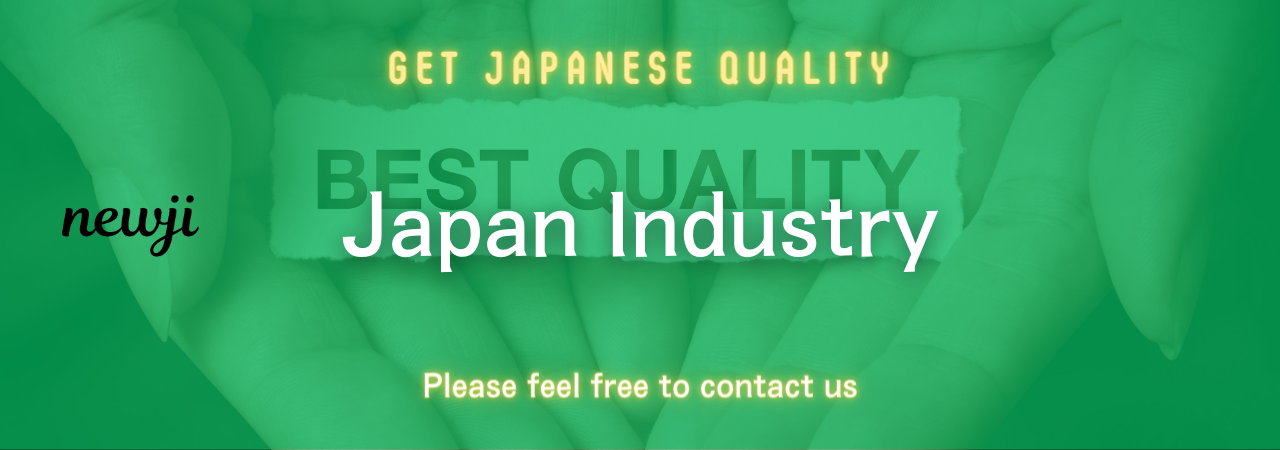
Welcome to the equipment management department of the precision machinery industry! It’s an exciting place to be and an area that plays an essential role in ensuring the smooth operation of the company’s machinery.
In this article, we will explore two significant aspects of your job: lubrication management and wear diagnosis of mechanical parts.
These concepts are crucial for maintaining machinery efficiency and preventing costly downtime.
Whether you’re fresh on the job or looking to refine your understanding, this guide will provide you with the foundational knowledge you need.
目次
Understanding Lubrication Management
Lubrication management is key to keeping machines running efficiently.
Essentially, it involves the controlled application of lubricants like oils and greases onto mechanical parts.
The goal is to minimize friction and wear, ensuring that machinery operates smoothly.
Proper lubrication can extend the lifespan of equipment and reduce maintenance costs.
The Importance of Choosing the Right Lubricant
Choosing the appropriate lubricant is crucial.
Not all lubricants are created equal, and each is designed for specific applications.
Key considerations include viscosity, operating temperature range, and the nature of the machine’s environment.
For example, high-temperature machinery will require a lubricant that can maintain its properties under heat stress, whereas a wet environment might necessitate a water-resistant option.
Regular Lubrication Schedules
Creating and adhering to a lubrication schedule is paramount.
This schedule outlines when each machine part should be lubricated, ensuring consistent application and optimal performance.
Missed lubrication can lead to increased friction and, subsequently, wear and tear on components.
Conversely, over-lubrication is wasteful and can cause operating problems.
Basics of Wear Diagnosis
Wear diagnosis helps in identifying when equipment parts are deteriorating.
Regular diagnosis ensures early detection of wear-related issues, allowing for intervention before they lead to machine failure.
Types of Mechanical Wear
Understanding different types of wear can aid in accurate diagnosis.
Common wear types include abrasive, adhesive, fatigue, and corrosive wear.
Abrasive wear occurs when hard particles scratch or cut the surface of softer materials.
Adhesive wear happens when material transfers from one surface to another.
Fatigue wear is the cracking and flaking of surfaces due to repeated stress, and corrosive wear is the result of chemical reactions with the material.
Techniques for Wear Diagnosis
Several techniques can be used to diagnose wear.
Visual inspection is a straightforward method, allowing you to observe and identify visible signs of wear.
However, it involves careful observation and might not detect underlying issues.
Other advanced techniques include vibration analysis, ultrasonic testing, and infrared thermography.
These require specific tools and expertise but can provide early detection of potential problems, allowing for proactive maintenance.
Implementing Best Practices
By integrating effective lubrication management and wear diagnosis practices, you can significantly enhance the longevity and efficiency of mechanical equipment.
Setting up a robust maintenance plan that encompasses these practices is crucial.
Training and Skill Development
Continuous learning and skill development are vital.
Participate in workshops, attend seminars, and keep abreast of industry advancements.
Stay informed about the latest lubrication technologies and diagnostic tools that can improve your department’s performance.
Collaborative Approach
Involve team members in the lubrication management and wear diagnosis processes.
A collaborative approach can lead to improved outcomes as different perspectives enhance problem-solving and creativity.
Moreover, shared responsibility ensures that tasks are not overlooked and allows for skill transfer among team members.
Documentation and Record Keeping
Maintaining accurate records of lubrication schedules and wear diagnosis results is essential.
This documentation helps track maintenance history and recognize patterns over time.
It can be useful for predictive maintenance, allowing you to anticipate future failures and prepare accordingly.
Moreover, it aids in compliance with industry standards and ensures accountability within the team.
Conclusion
As a new employee in the equipment management department of the precision machinery industry, understanding the basics of lubrication management and wear diagnosis is indispensable.
These processes contribute substantially to the reliable operation and longevity of machinery.
With the right approach and continuous learning, you will be well-equipped to handle the challenges that come your way.
Welcome aboard, and may your tenure be marked by efficient machines and minimal downtime.
資料ダウンロード
QCD調達購買管理クラウド「newji」は、調達購買部門で必要なQCD管理全てを備えた、現場特化型兼クラウド型の今世紀最高の購買管理システムとなります。
ユーザー登録
調達購買業務の効率化だけでなく、システムを導入することで、コスト削減や製品・資材のステータス可視化のほか、属人化していた購買情報の共有化による内部不正防止や統制にも役立ちます。
NEWJI DX
製造業に特化したデジタルトランスフォーメーション(DX)の実現を目指す請負開発型のコンサルティングサービスです。AI、iPaaS、および先端の技術を駆使して、製造プロセスの効率化、業務効率化、チームワーク強化、コスト削減、品質向上を実現します。このサービスは、製造業の課題を深く理解し、それに対する最適なデジタルソリューションを提供することで、企業が持続的な成長とイノベーションを達成できるようサポートします。
オンライン講座
製造業、主に購買・調達部門にお勤めの方々に向けた情報を配信しております。
新任の方やベテランの方、管理職を対象とした幅広いコンテンツをご用意しております。
お問い合わせ
コストダウンが利益に直結する術だと理解していても、なかなか前に進めることができない状況。そんな時は、newjiのコストダウン自動化機能で大きく利益貢献しよう!
(Β版非公開)