- お役立ち記事
- For process engineers in the semiconductor industry! RIE (Reactive Ion Etching) process control and yield improvement
For process engineers in the semiconductor industry! RIE (Reactive Ion Etching) process control and yield improvement
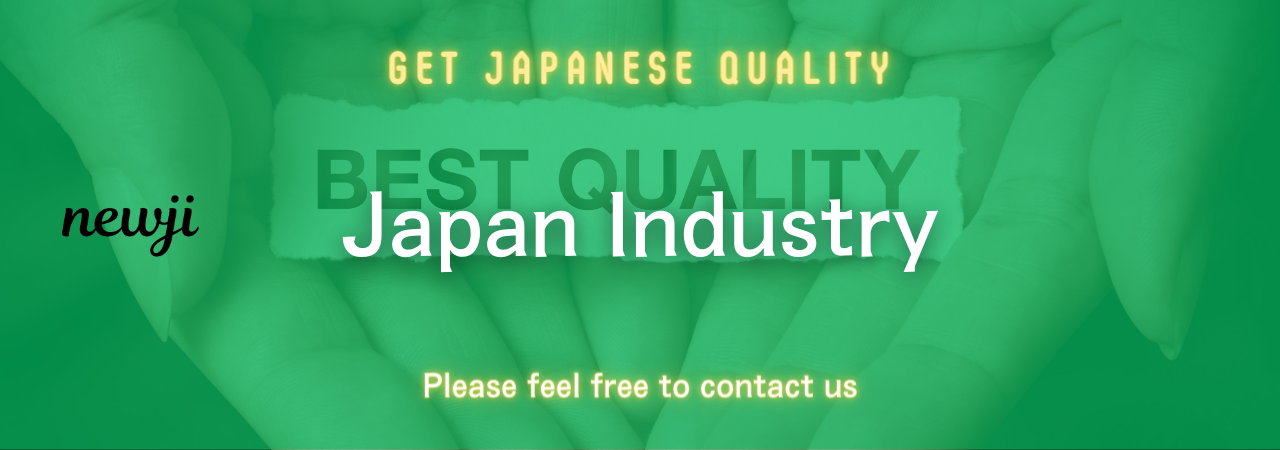
目次
Understanding the RIE Process
Reactive Ion Etching (RIE) stands as a critical technique in the semiconductor manufacturing industry, offering the precision necessary to craft complex electronic devices.
This process employs chemically reactive plasma to remove materials deposited on wafers, facilitating the creation of finely detailed and intricate patterns.
Its importance cannot be understated, as RIE helps in achieving the minute geometries that modern electronic components require.
By manipulating gaseous ions, RIE offers exceptional control over etching, making it indispensable for producing various semiconductor devices, from microprocessors to memory chips.
Understanding the fundamentals of the RIE process is essential for process engineers aiming to optimize manufacturing and ensure high yield.
The Importance of Process Control in RIE
Efficient process control in RIE is pivotal to achieving consistent quality and performance of electronic components.
Without precise control, variations in etching can lead to defects, affecting the yield and functionality of the devices.
This underscores the importance of maintaining close monitoring and adjustments during the RIE process.
Key aspects such as pressure, power input, gas flow rate, and etching time need to be meticulously controlled.
Even slight deviations can have a significant impact on the final product.
Engineers must familiarize themselves with how each parameter affects the process and its outcomes.
Challenges in RIE Process Control
One of the primary challenges in RIE process control is managing plasma conditions.
Plasma parameters are highly sensitive and can change rapidly, affecting the etching process.
Moreover, the intrinsic variability of wafers can introduce additional complexities.
This demands thorough knowledge and vigilance from engineers to swiftly address any anomalies that may arise.
Furthermore, developments in semiconductor technologies continually push the limits of miniaturization, necessitating even more precise control in RIE processes.
Adapting to these evolving requirements ensures that engineers remain at the forefront of technological innovation and production efficiency.
Strategies for Yield Improvement
Achieving high yield in semiconductor manufacturing is crucial for cost-effectiveness and meeting market demands.
RIE process optimization plays a significant role in enhancing yield.
Engineers can adopt several strategies to improve yield outcomes significantly.
Parametric Optimization
One effective method for yield improvement is the optimization of RIE process parameters.
Conducting experiments to determine the optimal combination of power, pressure, and gas composition can lead to significant enhancements.
Utilizing advanced data analytics and statistical methods can aid in identifying the most favorable conditions, reducing error margins significantly.
This proactive approach aids in minimizing defects, ensuring that the majority of manufactured devices meet quality standards.
Real-time Monitoring and Feedback
Incorporating real-time monitoring and feedback mechanisms is instrumental in ensuring consistent etching quality.
Advanced sensors and automated systems can track process parameters and immediately alert operators to any deviations.
Implementing machine learning algorithms can further improve these systems, enabling predictive maintenance and reducing downtime.
Consistent, timely feedback allows engineers to make prompt adjustments, enhancing the RIE process’s stability and robustness.
Materials and Equipment Upgrades
Investing in state-of-the-art equipment and exploring newer materials can also drive yield improvement.
Developments in technology can offer solutions that provide greater control over the RIE process, leading to better accuracy and efficiency.
Staying updated with the latest tools and techniques ensures that a manufacturing line is operating at optimal potential.
Engineers should make it a priority to evaluate and incorporate innovations that suit their specific processes and requirements.
The Role of Training and Communication
While technical adjustments and innovations are paramount, the human factor plays an equally crucial role in the RIE process’s success.
Ensuring that all personnel involved in the process are well-trained and informed can have a substantial impact on outcomes.
Regular training sessions and workshops enable staff to remain current with best practices and industry advancements.
Moreover, fostering a culture of open communication enables collaboration and problem-solving, leading to continuous improvement.
Feedback from operators can provide invaluable insights into areas for enhancement, further contributing to efficiency and yield.
Conclusion
For process engineers in the semiconductor industry, mastering RIE process control and yield improvement is essential.
By focusing on process parameters, adopting new technologies, and prioritizing training, yield can be substantially increased.
As semiconductor devices continue to evolve, so too must the strategies employed by engineers to ensure both quality and efficiency.
Through dedication to excellence, engineers can contribute significantly to the industry’s growth and innovation.
資料ダウンロード
QCD調達購買管理クラウド「newji」は、調達購買部門で必要なQCD管理全てを備えた、現場特化型兼クラウド型の今世紀最高の購買管理システムとなります。
ユーザー登録
調達購買業務の効率化だけでなく、システムを導入することで、コスト削減や製品・資材のステータス可視化のほか、属人化していた購買情報の共有化による内部不正防止や統制にも役立ちます。
NEWJI DX
製造業に特化したデジタルトランスフォーメーション(DX)の実現を目指す請負開発型のコンサルティングサービスです。AI、iPaaS、および先端の技術を駆使して、製造プロセスの効率化、業務効率化、チームワーク強化、コスト削減、品質向上を実現します。このサービスは、製造業の課題を深く理解し、それに対する最適なデジタルソリューションを提供することで、企業が持続的な成長とイノベーションを達成できるようサポートします。
オンライン講座
製造業、主に購買・調達部門にお勤めの方々に向けた情報を配信しております。
新任の方やベテランの方、管理職を対象とした幅広いコンテンツをご用意しております。
お問い合わせ
コストダウンが利益に直結する術だと理解していても、なかなか前に進めることができない状況。そんな時は、newjiのコストダウン自動化機能で大きく利益貢献しよう!
(Β版非公開)