- お役立ち記事
- Increasing productivity by “improving bottlenecks”—Instructions from management that field managers should implement
Increasing productivity by “improving bottlenecks”—Instructions from management that field managers should implement
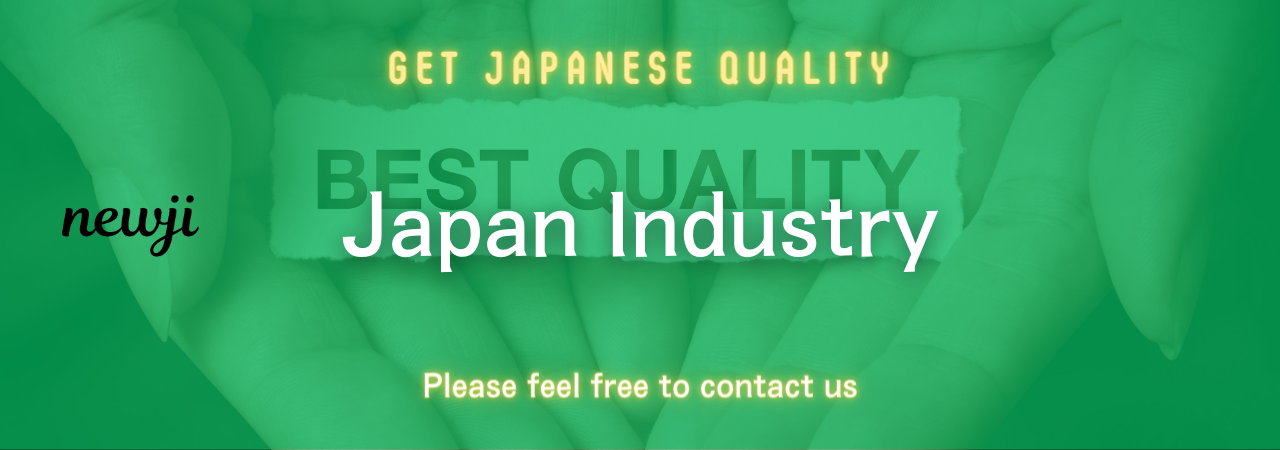
目次
Understanding Bottlenecks
In any organization, understanding bottlenecks is crucial for improving productivity.
Bottlenecks are the points in a workflow where progress is limited or stopped entirely.
These can occur in various forms, whether it’s a slow piece of machinery, a lack of skilled personnel, or inefficient processes.
Identifying and addressing bottlenecks can significantly enhance an organization’s overall productivity.
Field managers, those on the front lines of operations, are in a unique position to identify these constraints.
They have firsthand experience with operations and can provide valuable insights into where improvements are necessary.
When bottlenecks are ignored, they cause delays, decrease morale, and lead to increased costs.
Hence, field managers must be proactive in finding and fixing these inefficiencies.
Identifying Bottlenecks
The first step in resolving productivity issues is to identify where bottlenecks exist.
Field managers should regularly observe and analyze their team’s workflow, paying particular attention to places where work backs up or slows down.
Simple tools like workflow diagrams can help visualize processes and identify which areas require further investigation.
Another effective method is to solicit feedback from team members.
Workers often have valuable insights into what slows them down or causes frustration.
Regular meetings or suggestion boxes can encourage staff to voice concerns and provide constructive feedback.
It’s also beneficial to keep track of performance metrics, such as processing times and outputs.
By comparing these metrics to established benchmarks or historical data, field managers can pinpoint areas where performance lags behind expectations.
In some cases, employing software that tracks performance data can provide an in-depth look at where issues occur.
Strategies to Improve Bottlenecks
Once bottlenecks are identified, field managers can work on strategies to improve these areas.
The necessary approach may vary depending on the specific type of bottleneck but generally involves streamlining processes or reallocating resources.
Often, introducing new tools or technology can expedite tasks and reduce delays.
For example, upgrading equipment or implementing automation in simple, repetitive tasks can help speed up the workflow.
However, it is important to ensure that all new systems are user-friendly and that employees receive sufficient training.
Re-evaluating staffing levels and schedules can also help address human resource bottlenecks.
This might mean hiring additional staff during peak times or redistributing workloads among existing staff to balance productivity.
Process improvements, such as adopting lean manufacturing techniques or the Six Sigma methodology, can help refine workflows.
These methodologies focus on reducing waste, improving quality, and ensuring that every part of the process adds value.
Field managers can also encourage employees to come up with innovative solutions to enhance efficiency.
Involving Management in Bottleneck Solutions
Communication with upper management is crucial when addressing bottlenecks.
Field managers should present clear, data-backed analyses of productivity issues to convince upper-level management of the need for improvement.
The success of bottleneck solutions often hinges on obtaining resources, such as funding for new equipment or training sessions.
Therefore, presenting a cost-benefit analysis that forecasts the potential gains in productivity and the resulting financial savings can be persuasive.
Management buy-in will ensure that necessary changes are supported and prioritized.
Additionally, collaboration between field managers, their teams, and upper management encourages a sense of shared responsibility.
When everyone is invested in the successful resolution of bottlenecks, team members are more likely to embrace changes and work together to achieve common goals.
Monitoring and Adjusting Solutions
Implementing a solution for bottlenecks is not an endpoint but rather an ongoing process.
Once strategies are put in place, continued observation is necessary to ensure that the desired improvements are achieved.
Field managers should revisit performance metrics regularly to verify that the bottleneck has been effectively addressed.
Continuous improvement is key.
If the initial solutions do not entirely eliminate the bottleneck, adjustments should be made.
This iterative approach allows for adapting strategies as work processes and business objectives evolve.
Engaging in regular reviews also continues to motivate the team, reinforcing a commitment to productivity excellence.
Conclusion
Improving productivity by addressing bottlenecks is an essential part of efficient management.
Field managers play a crucial role in this process due to their direct involvement in daily operations.
By identifying bottlenecks, implementing effective solutions, and working closely with their teams and management, field managers can drive significant improvements.
Continual assessment and responsiveness to changes ensure that solutions remain relevant and effective.
Ultimately, by honing the ability to identify and improve bottlenecks, organizations can realize substantial gains in productivity, leading to enhanced competitiveness and long-term success.
資料ダウンロード
QCD調達購買管理クラウド「newji」は、調達購買部門で必要なQCD管理全てを備えた、現場特化型兼クラウド型の今世紀最高の購買管理システムとなります。
ユーザー登録
調達購買業務の効率化だけでなく、システムを導入することで、コスト削減や製品・資材のステータス可視化のほか、属人化していた購買情報の共有化による内部不正防止や統制にも役立ちます。
NEWJI DX
製造業に特化したデジタルトランスフォーメーション(DX)の実現を目指す請負開発型のコンサルティングサービスです。AI、iPaaS、および先端の技術を駆使して、製造プロセスの効率化、業務効率化、チームワーク強化、コスト削減、品質向上を実現します。このサービスは、製造業の課題を深く理解し、それに対する最適なデジタルソリューションを提供することで、企業が持続的な成長とイノベーションを達成できるようサポートします。
オンライン講座
製造業、主に購買・調達部門にお勤めの方々に向けた情報を配信しております。
新任の方やベテランの方、管理職を対象とした幅広いコンテンツをご用意しております。
お問い合わせ
コストダウンが利益に直結する術だと理解していても、なかなか前に進めることができない状況。そんな時は、newjiのコストダウン自動化機能で大きく利益貢献しよう!
(Β版非公開)