- お役立ち記事
- For leaders in equipment management departments in the electronics manufacturing industry! Cleanroom Airflow Design and Optimization Guide
For leaders in equipment management departments in the electronics manufacturing industry! Cleanroom Airflow Design and Optimization Guide
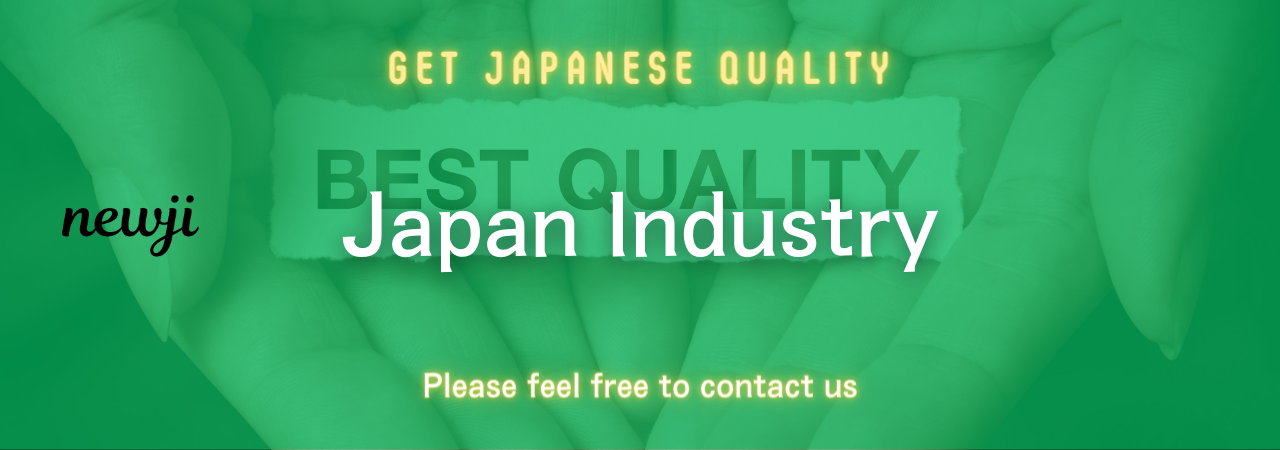
目次
Understanding Cleanroom Airflow
Cleanrooms are controlled environments where contamination, dust, airborne microbes, and particulates are regulated to very low levels.
They are critical in the electronics manufacturing industry, especially in semiconductor production, where even the tiniest contaminant can ruin an entire batch of products.
The importance of cleanroom airflow design cannot be overstated as it directly impacts the cleanliness and efficiency of the manufacturing process.
The airflow in a cleanroom is typically either laminar or turbulent.
Laminar airflow moves at the same speed and in parallel layers, creating a streamlined movement that helps prevent particles from being disrupted and released into the air.
This type of airflow is often used in areas that require the highest level of cleanliness.
In contrast, turbulent airflow mixes the air, which can increase the potential for contamination but is easier to control and manage in larger spaces.
Key Considerations in Airflow Design
To design an effective cleanroom airflow system, several key factors must be considered.
The primary goal is maintaining low particle counts while ensuring consistent temperature and humidity levels.
Air Volume and Velocity
The volume and velocity of air supplied to a cleanroom are critical in ensuring that airborne contaminants are quickly and effectively removed.
The air volume must be sufficient to dilute and remove particulates while maintaining the desired pressure differentials between cleanroom zones.
Air Changes Per Hour (ACH)
Air Changes Per Hour (ACH) refers to how many times the air within the cleanroom is replaced in an hour.
A higher ACH rate ensures more frequent removal of airborne contaminants.
The ACH rate varies depending on the cleanroom classification.
Higher classification cleanrooms may require 400–600 ACH, whereas lower classifications may suffice with 20–60 ACH.
Filter Selection
Filters play a crucial role in maintaining cleanroom air quality.
High-Efficiency Particulate Air (HEPA) filters are commonly used, capable of trapping particles as small as 0.3 microns with an efficiency of 99.97%.
For even more stringent requirements, Ultra-Low Penetration Air (ULPA) filters can capture particles down to 0.12 microns with 99.9995% efficiency.
Optimizing Cleanroom Airflow
Once the initial design is implemented, continual optimization ensures that the cleanroom remains effective and efficient.
Monitoring and Testing
Regular monitoring and testing are essential for maintaining the cleanroom’s integrity.
This includes measuring air velocity, particle counts, and pressure differentials.
Adjustments should be made based on these test results to maintain optimal environmental conditions.
Proper Maintenance
Routine maintenance of the HVAC system, including filter replacements and cleaning of ductwork, ensures effective airflow and prevents system inefficiencies.
Regular inspections help identify and resolve issues before they affect the cleanroom environment.
Personnel Training
Personnel should be trained in best practices for maintaining cleanroom standards.
This includes proper gowning procedures and understanding the impact of movements on airflow patterns.
Educated staff can significantly reduce the risk of contamination.
Designing for Future Growth
As technology evolves, the need for even cleaner environments may arise.
Designing cleanroom airflow systems with future scalability in mind can save time and resources.
Using modular designs and configurable systems can accommodate changes in production demands without significant infrastructure overhaul.
Conclusion
Cleanroom airflow design and optimization are critical components in the electronics manufacturing industry.
With careful planning and attention to detail, contamination can be minimized, ensuring high-quality production.
By understanding the principles of airflow, selecting appropriate filters, and committing to ongoing maintenance and training, leaders in equipment management can ensure that their facilities remain competitive and efficient.
When the airflow design is optimized, manufacturers are better equipped to produce at the highest standards, maintaining product integrity and customer satisfaction.
資料ダウンロード
QCD調達購買管理クラウド「newji」は、調達購買部門で必要なQCD管理全てを備えた、現場特化型兼クラウド型の今世紀最高の購買管理システムとなります。
ユーザー登録
調達購買業務の効率化だけでなく、システムを導入することで、コスト削減や製品・資材のステータス可視化のほか、属人化していた購買情報の共有化による内部不正防止や統制にも役立ちます。
NEWJI DX
製造業に特化したデジタルトランスフォーメーション(DX)の実現を目指す請負開発型のコンサルティングサービスです。AI、iPaaS、および先端の技術を駆使して、製造プロセスの効率化、業務効率化、チームワーク強化、コスト削減、品質向上を実現します。このサービスは、製造業の課題を深く理解し、それに対する最適なデジタルソリューションを提供することで、企業が持続的な成長とイノベーションを達成できるようサポートします。
オンライン講座
製造業、主に購買・調達部門にお勤めの方々に向けた情報を配信しております。
新任の方やベテランの方、管理職を対象とした幅広いコンテンツをご用意しております。
お問い合わせ
コストダウンが利益に直結する術だと理解していても、なかなか前に進めることができない状況。そんな時は、newjiのコストダウン自動化機能で大きく利益貢献しよう!
(Β版非公開)