- お役立ち記事
- Data analysis to discover supply chain bottlenecks from a purchasing department perspective
Data analysis to discover supply chain bottlenecks from a purchasing department perspective
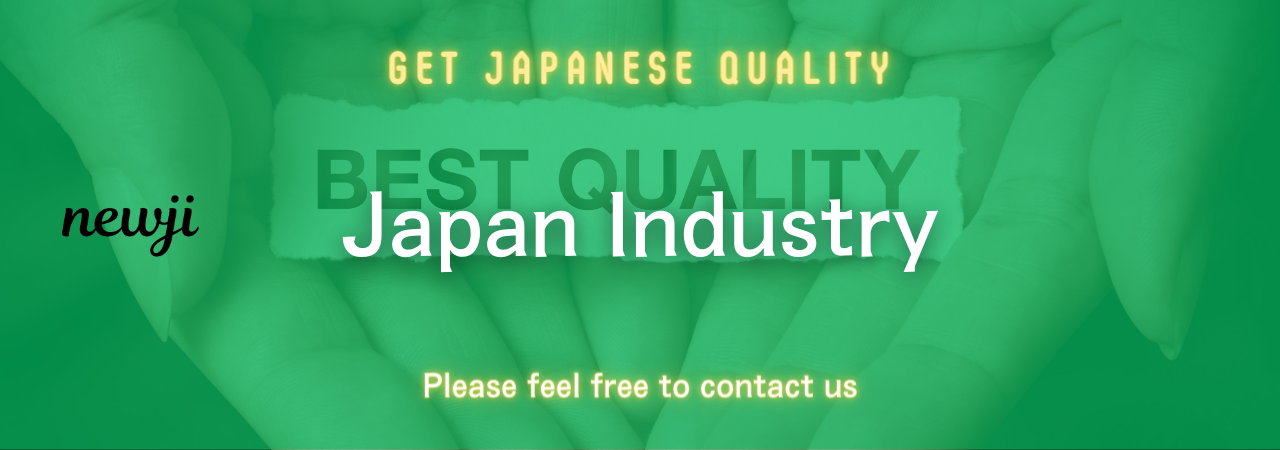
目次
Understanding Supply Chain Bottlenecks
Supply chains are complex networks that involve the flow of goods and services from suppliers to customers.
In this intricate system, bottlenecks can occur, causing delays and inefficiencies.
Identifying these bottlenecks is essential, especially from the viewpoint of a purchasing department.
By using data analysis, organizations can pinpoint bottlenecks, streamline operations, and enhance overall efficiency.
The Role of the Purchasing Department
The purchasing department plays a crucial role in supply chain management.
It is responsible for sourcing materials, negotiating contracts, and ensuring timely delivery of goods and services.
The department acts as a bridge between suppliers and other departments, facilitating smooth operations.
For the purchasing department, identifying where bottlenecks occur and understanding their impact is vital.
This knowledge allows for strategic decision-making and improved supplier relationships.
Data Analysis Techniques for Identifying Bottlenecks
Data analysis provides powerful tools for uncovering supply chain bottlenecks.
Several techniques can be employed to identify and address these issues.
Supply Chain Mapping
Supply chain mapping involves documenting each step in the supply chain process.
This helps visualize where materials come from, how they move through the system, and where delays might occur.
By mapping the supply chain, organizations can identify potential bottlenecks and areas for improvement.
Descriptive Analytics
Descriptive analytics involves analyzing historical data to understand what has happened in the supply chain.
This could include tracking lead times, fill rates, and order accuracy.
With these insights, the purchasing department can identify recurring issues and patterns that may indicate underlying bottlenecks.
Predictive Analytics
Predictive analytics uses statistical models and forecasts to predict future supply chain behaviors.
By examining trends and patterns, the purchasing department can anticipate potential disruptions and bottlenecks.
Predictive analytics enhances planning and enables proactive measures to mitigate risks before they escalate.
Prescriptive Analytics
Prescriptive analytics goes a step further by recommending specific actions based on predictive data.
It suggests optimal strategies for managing supply chain disruptions and improving efficiency.
This data-driven approach allows purchasing departments to make informed decisions that reduce bottlenecks.
Key Indicators of Supply Chain Bottlenecks
Recognizing the signs of bottlenecks is fundamental in addressing supply chain issues effectively.
Several key indicators help identify these problem areas.
Increased Lead Times
Longer than usual lead times are a primary indicator of a supply chain bottleneck.
Lead times can increase due to production delays, transportation issues, or supplier constraints.
Monitoring lead times helps the purchasing department identify where delays are occurring.
Stock Shortages
Frequent stock shortages can signify a bottleneck at the supplier or transportation level.
When stock levels are consistently low, it may indicate inefficiencies in procurement or inventory management.
Addressing stock shortages requires analyzing the supply chain flow to locate the disruption source.
Order Backlogs
An accumulation of unfulfilled orders suggests a bottleneck.
Order backlogs can stem from insufficient capacity, slow processing times, or supplier delays.
Regularly reviewing order status allows purchasing departments to spot backlogs quickly.
High Order-to-Delivery Variability
When there is significant variability in the time it takes for orders to be delivered, a bottleneck may be present.
This variability makes it challenging to plan and forecast accurately.
Reducing variability requires analyzing the supply chain process for inconsistencies.
Strategies to Mitigate Supply Chain Bottlenecks
Once a bottleneck is identified, implementing strategies to mitigate its impact is crucial.
Collaboration with Suppliers
Strengthening relationships with suppliers can help alleviate bottlenecks.
Open communication ensures that suppliers understand the organization’s needs and can adjust their processes accordingly.
Collaborative approaches lead to better coordination and reduced delays.
Flexibility in Procurement
Implementing flexible procurement strategies allows organizations to respond quickly to changes or disruptions in the supply chain.
This might involve diversifying suppliers or having contingency plans in place.
Flexibility ensures minimal disruption when unexpected bottlenecks arise.
Improved Inventory Management
Efficient inventory management practices can prevent stock shortages and overstock situations.
By optimizing inventory levels, purchasing departments can ensure that the right amount of stock is available when needed.
This reduces the chance of bottlenecks and increases supply chain resilience.
Utilizing Technology
Leveraging technology such as supply chain management software and real-time tracking systems enhances visibility and control.
These tools provide accurate data on supply chain performance, allowing prompt identification of issues.
Technology streamlines processes and helps prevent bottlenecks before they occur.
Conclusion
Data analysis is a vital tool in discovering and addressing supply chain bottlenecks from a purchasing department perspective.
By using various analytics techniques, organizations can gain insights into their supply chain operations and identify problem areas.
Understanding key indicators and implementing strategic actions can significantly reduce the impact of bottlenecks.
With proactive management and data-driven decision-making, the purchasing department can enhance supply chain efficiency and contribute to the organization’s overall success.
資料ダウンロード
QCD調達購買管理クラウド「newji」は、調達購買部門で必要なQCD管理全てを備えた、現場特化型兼クラウド型の今世紀最高の購買管理システムとなります。
ユーザー登録
調達購買業務の効率化だけでなく、システムを導入することで、コスト削減や製品・資材のステータス可視化のほか、属人化していた購買情報の共有化による内部不正防止や統制にも役立ちます。
NEWJI DX
製造業に特化したデジタルトランスフォーメーション(DX)の実現を目指す請負開発型のコンサルティングサービスです。AI、iPaaS、および先端の技術を駆使して、製造プロセスの効率化、業務効率化、チームワーク強化、コスト削減、品質向上を実現します。このサービスは、製造業の課題を深く理解し、それに対する最適なデジタルソリューションを提供することで、企業が持続的な成長とイノベーションを達成できるようサポートします。
オンライン講座
製造業、主に購買・調達部門にお勤めの方々に向けた情報を配信しております。
新任の方やベテランの方、管理職を対象とした幅広いコンテンツをご用意しております。
お問い合わせ
コストダウンが利益に直結する術だと理解していても、なかなか前に進めることができない状況。そんな時は、newjiのコストダウン自動化機能で大きく利益貢献しよう!
(Β版非公開)