- お役立ち記事
- Shorten logistics lead time by streamlining the import/export process Measures that purchasing departments should know
Shorten logistics lead time by streamlining the import/export process Measures that purchasing departments should know
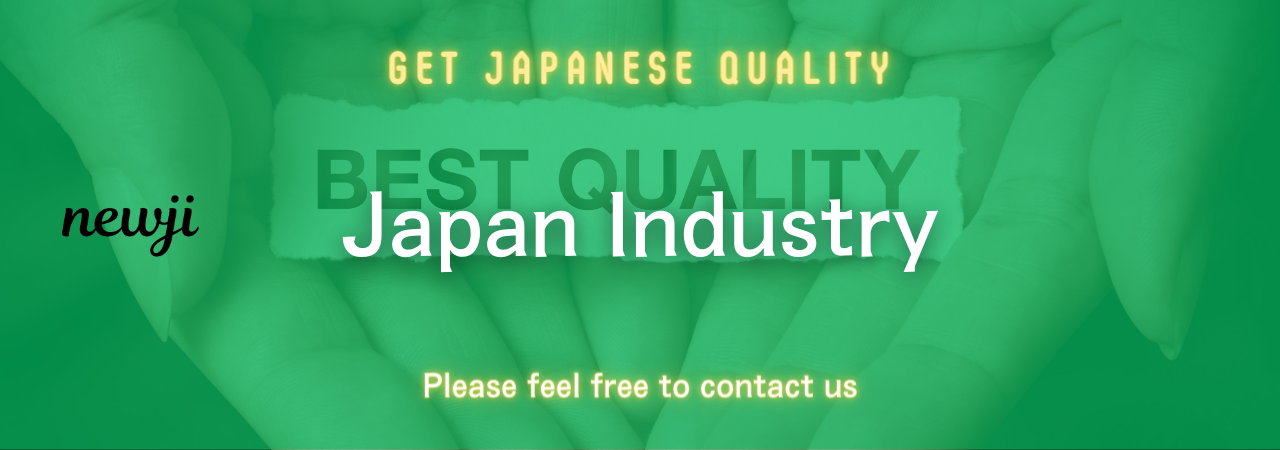
目次
Understanding Logistics Lead Time
In the world of logistics, lead time refers to the period from when an order is placed until it is delivered to its final destination.
For businesses involved in import and export, managing and reducing logistics lead time is crucial.
Fast and efficient delivery can enhance customer satisfaction and offer a competitive edge in the market.
However, long lead times can delay product availability, disrupt supply chains, and increase costs.
It is essential for purchasing departments to be aware of and implement strategies to streamline this process, thereby reducing lead time.
Streamlining the Import/Export Process
To effectively shorten logistics lead time, businesses must focus on streamlining their import and export processes.
A streamlined process ensures that goods move faster through various steps, from production to transportation and finally to delivery.
This can be achieved through various measures that purchasing departments should be familiar with.
Embrace Technology and Automation
One of the most effective ways to reduce lead time is by integrating technology and automation into the logistics process.
Implementing software solutions like Warehouse Management Systems (WMS) or Transportation Management Systems (TMS) can significantly enhance efficiency.
These systems automate routine tasks, such as inventory tracking and shipment scheduling, which reduces errors and saves time.
Moreover, automation can expedite customs documentation and clearance processes, eliminating manual inefficiencies.
Build Strong Relationships with Suppliers
Fostering strong relationships with suppliers is key to streamlining logistics.
By collaborating closely, businesses can ensure that information flows smoothly and that both parties are aligned in terms of expectations and timelines.
Strategic partnerships allow for better negotiation of terms and conditions, which can include faster processing times or priority handling during peak seasons.
Reliable communication with suppliers also helps in quick resolution of any issues that might arise.
Optimize Inventory Management
Understanding and optimizing inventory management is critical for reducing logistics lead time.
Purchasing departments should ensure they have accurate data on stock levels and demand forecasts to prevent overstocking or stockouts.
Adopting techniques such as Just-In-Time (JIT) inventory can minimize holding costs while ensuring products are available exactly when needed.
This practice reduces warehouse storage time and accelerates the overall supply chain process.
Improve Customs Procedures
For businesses engaged in international trade, customs clearance can be a major bottleneck in the logistics process.
To tackle this, companies should ensure all necessary documentation is prepared well in advance.
This includes invoices, bills of lading, certificates of origin, and compliance documentation.
Furthermore, hiring customs brokers can be beneficial, as they are experts in navigating and speeding up customs clearance.
Investing in Authorized Economic Operator (AEO) status can also facilitate smoother customs operations.
Enhance Logistics Network Planning
Effective logistics network planning can drastically reduce overall lead time.
Purchasing departments should assess the current transportation routes and look for ways to improve them.
Considerations include choosing reliable carriers, optimizing delivery routes, and identifying strategic distribution centers near key markets.
Adopting multi-modal transport solutions can also offer flexibility and reduce dependency on a single mode of transport.
Implement Continuous Monitoring and Analysis
Continuous monitoring and analysis of the logistics process allows businesses to identify bottlenecks and areas for improvement.
Using data analytics tools, companies can track shipment progress, measure on-time deliveries, and pinpoint recurring issues.
This data-driven approach helps in making informed decisions and refinements in the logistics process.
Regular reviews and process audits ensure that any changes lead to the desired outcome of reduced lead time.
The Role of Purchasing Departments
Purchasing departments play a crucial role in minimizing logistics lead time.
They are responsible for coordinating with suppliers, managing procurement strategies, and facilitating smooth information exchange.
These departments can implement effective supply chain practices and adopt technologies that visually map the logistics process, identifying weak links or delays.
Coordinating with Stakeholders
Purchasing departments must work closely with stakeholders throughout the supply chain.
This collaboration ensures that everyone, from suppliers to transport providers, is on the same page.
When there is a unified effort from all participants, streamlining the logistics process becomes more manageable and effective.
Adopting Risk Management Practices
Another key responsibility of purchasing departments is to foresee and mitigate potential risks that could cause delays.
They need to anticipate challenges and have contingency plans in place.
Risk management practices could include having backup suppliers, maintaining safety stocks, or exploring alternative transport methods in case of disruptions.
Conclusion
Reducing logistics lead time is essential for businesses involved in import and export.
By streamlining the logistics process, companies can ensure faster deliveries, improve customer satisfaction, and remain competitive.
Purchasing departments play a pivotal role by adopting technologies, optimizing processes, and fostering collaborations.
When these practices are effectively executed, businesses can not only reduce lead time but also achieve greater efficiency and cost-effectiveness in their supply chain operations.
資料ダウンロード
QCD調達購買管理クラウド「newji」は、調達購買部門で必要なQCD管理全てを備えた、現場特化型兼クラウド型の今世紀最高の購買管理システムとなります。
ユーザー登録
調達購買業務の効率化だけでなく、システムを導入することで、コスト削減や製品・資材のステータス可視化のほか、属人化していた購買情報の共有化による内部不正防止や統制にも役立ちます。
NEWJI DX
製造業に特化したデジタルトランスフォーメーション(DX)の実現を目指す請負開発型のコンサルティングサービスです。AI、iPaaS、および先端の技術を駆使して、製造プロセスの効率化、業務効率化、チームワーク強化、コスト削減、品質向上を実現します。このサービスは、製造業の課題を深く理解し、それに対する最適なデジタルソリューションを提供することで、企業が持続的な成長とイノベーションを達成できるようサポートします。
オンライン講座
製造業、主に購買・調達部門にお勤めの方々に向けた情報を配信しております。
新任の方やベテランの方、管理職を対象とした幅広いコンテンツをご用意しております。
お問い合わせ
コストダウンが利益に直結する術だと理解していても、なかなか前に進めることができない状況。そんな時は、newjiのコストダウン自動化機能で大きく利益貢献しよう!
(Β版非公開)