- お役立ち記事
- For production engineers in the pharmaceutical manufacturing industry! Technology that maximizes drug stability through the freeze-drying process
For production engineers in the pharmaceutical manufacturing industry! Technology that maximizes drug stability through the freeze-drying process
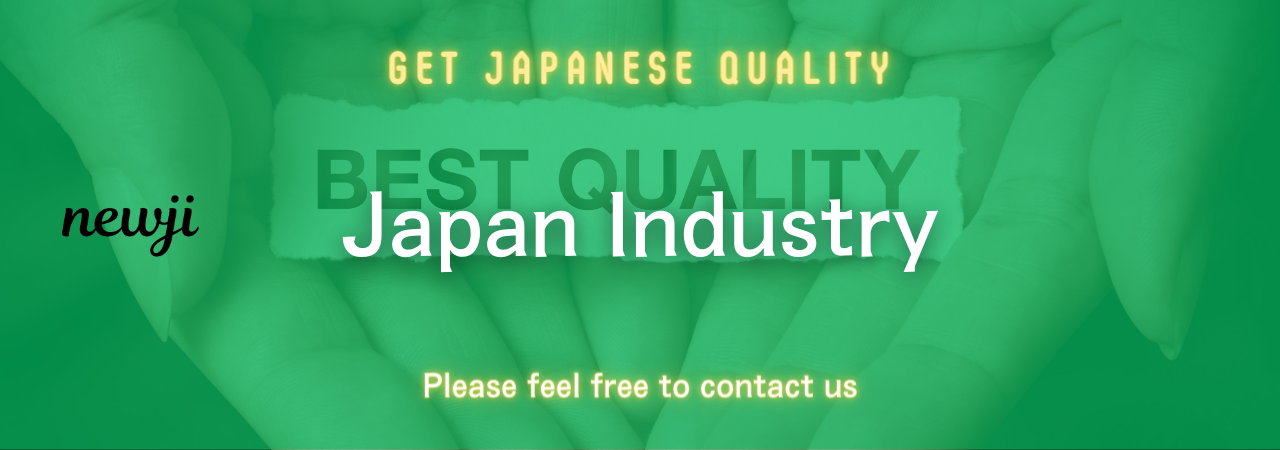
目次
Understanding the Freeze-Drying Process
Freeze-drying, also known as lyophilization, is a process used extensively within the pharmaceutical manufacturing industry to enhance the stability and shelf life of drugs.
This process involves removing water from a product after it has been frozen and placed under a vacuum, allowing the ice to change from a solid to a vapor without passing through a liquid phase.
This transformation process is pivotal as it helps to maintain the structural integrity and effectiveness of the pharmaceutical compounds, ensuring safety and potency for extended periods.
The primary goal of freeze-drying in the pharmaceutical realm is to produce stable, solid formulations of sensitive drug substances.
These substances would otherwise be prone to degradation in a liquid state or when exposed to air.
Through lyophilization, pharmaceuticals can be stored and transported easily, reducing the likelihood of requiring cold chain logistics, which can be challenging and costly.
The Science Behind Freeze-Drying
At the core of freeze-drying technology is the principle of sublimation.
This is the process whereby ice is transformed directly into water vapor without transitioning into liquid form.
For pharmaceuticals, this sublimation occurs in a primary drying phase within the freeze-drying cycle, characterized by controlled low temperature and pressure conditions.
During the initial freezing phase, the product is frozen rapidly to anchor the solute molecules with a rigid ice structure.
Next, in the primary drying phase, under reduced pressure, the ice inside the product sublimates while the structure of the solid solute remains intact.
Following this is the secondary drying phase, aimed at eliminating unfrozen water molecules through desorption, ensuring the maximum reduction of moisture content in the product.
This thorough removal of water content is crucial in ensuring stability, as the absence of water minimizes hydrolytic and microbial degradation of the drug.
Benefits of Freeze-Drying for Drug Stability
Freeze-drying offers several remarkable advantages in the pharmaceutical manufacturing sector.
The resultant freeze-dried product is characterized by reduced weight and minimized water content, which are essential for increased stability and shelf life.
One significant benefit lies in the preservation of efficacy for complex drug formulations.
By preventing water-induced degradation, pharmaceuticals maintain their therapeutic effectiveness over time, ensuring they meet stringent efficacy standards upon administration.
Additionally, transporting freeze-dried drugs is simplified due to their reduced weight, eliminating the need for specialized cold chain facilities.
This reduction in logistical complexities translates into cost savings and ensures the accessibility of vital medications in regions with inadequate refrigeration infrastructure.
Moreover, the freeze-drying process ensures uniformity in final product quality, making it easier to control and validate batches during manufacturing.
Consistency in potency and purity is imperative in meeting regulatory standards and in securing trust in pharmaceutical products amongst healthcare providers and patients.
Technological Innovations in Freeze-Drying
Recent technological advancements have enhanced and streamlined the freeze-drying process, achieving higher efficiency and precision in pharmaceutical manufacturing.
Modern lyophilizers are equipped with improved temperature and pressure control systems, enabling more accurate execution of drying cycles tailored to specific pharmaceutical products.
Advancements in software and control systems have also introduced product-tracking capabilities, offering real-time monitoring and recording of the freeze-drying conditions.
This data-driven approach facilitates quick adjustments and optimization of the operating parameters, resulting in enhanced productivity and reduced risk of batch failures.
Further innovations have yielded sophisticated freeze-drying process analytics, paving the way for predictive maintenance and troubleshooting capabilities.
This integration of data analytics in lyophilization allows manufacturers to anticipate and address potential issues proactively, reducing downtime and increasing overall equipment effectiveness.
Challenges of Freeze-Drying in Pharmaceutical Manufacturing
Despite its benefits, freeze-drying poses challenges that production engineers must overcome to maximize its potential.
One critical challenge is the high energy usage inherent in the freeze-drying process, leading to increased operational costs.
Efforts to optimize the energy consumption of freeze-dryers remain a key focus area for pharmaceutical manufacturers striving for cost-effective production.
Additionally, achieving scalable production capacity through freeze-drying can pose challenges.
Scaling up the lyophilization process without compromising product quality necessitates careful planning and investment in high-capacity equipment and facility infrastructure.
Lastly, the complexity of designing suitable formulations for freeze-drying can impede product development timelines.
The need to formulate pharmaceuticals that can withstand freezing and sublimation while maintaining potency complicates product formulation strategies.
The Future of Freeze-Drying in Pharmaceuticals
Going forward, the application of freeze-drying technology within the pharmaceutical industry is anticipated to expand further.
Innovation will likely focus on increasing the process’s efficiency, reducing costs, and enhancing scalability to meet growing demands.
Developments in digitalization, process automation, and machine learning are forecasted to revolutionize lyophilization.
These technologies promise unprecedented levels of precision and efficiency while providing deeper insights into machinery operation and maintenance.
Furthermore, the integration of eco-friendly practices within freeze-drying operations will become increasingly relevant as sustainability becomes a priority.
This shift will motivate pharmaceutical companies to adopt greener practices while balancing ethical responsibility and profitability.
In summary, as pharmaceutical manufacturers strive to maintain and enhance the stability of drug formulations, freeze-drying remains an indispensable technology.
By continuing to innovate and surmount challenges, production engineers in this sector will play a critical role in shaping the future of pharmaceutical manufacturing.
資料ダウンロード
QCD調達購買管理クラウド「newji」は、調達購買部門で必要なQCD管理全てを備えた、現場特化型兼クラウド型の今世紀最高の購買管理システムとなります。
ユーザー登録
調達購買業務の効率化だけでなく、システムを導入することで、コスト削減や製品・資材のステータス可視化のほか、属人化していた購買情報の共有化による内部不正防止や統制にも役立ちます。
NEWJI DX
製造業に特化したデジタルトランスフォーメーション(DX)の実現を目指す請負開発型のコンサルティングサービスです。AI、iPaaS、および先端の技術を駆使して、製造プロセスの効率化、業務効率化、チームワーク強化、コスト削減、品質向上を実現します。このサービスは、製造業の課題を深く理解し、それに対する最適なデジタルソリューションを提供することで、企業が持続的な成長とイノベーションを達成できるようサポートします。
オンライン講座
製造業、主に購買・調達部門にお勤めの方々に向けた情報を配信しております。
新任の方やベテランの方、管理職を対象とした幅広いコンテンツをご用意しております。
お問い合わせ
コストダウンが利益に直結する術だと理解していても、なかなか前に進めることができない状況。そんな時は、newjiのコストダウン自動化機能で大きく利益貢献しよう!
(Β版非公開)