- お役立ち記事
- Basics of continuous casting technology and yield management that new employees in the production technology department of the steel industry should know
Basics of continuous casting technology and yield management that new employees in the production technology department of the steel industry should know
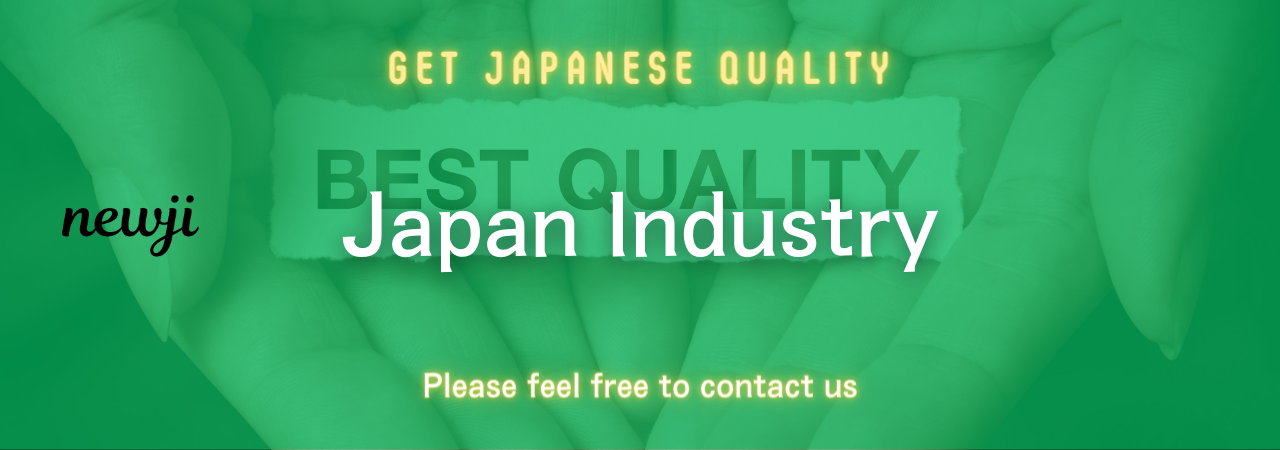
目次
Understanding Continuous Casting Technology
Continuous casting technology is a vital process within the steel industry, allowing for the efficient production of high-quality steel products.
In essence, this technology involves the solidification of molten steel into a semi-finished billet, bloom, or slab for further processing.
Continuous casting offers several advantages over traditional ingot casting, including improved yield, quality, and productivity.
The process begins when molten steel is poured into a mold, where it gradually cools and solidifies as it moves through a series of rollers.
New employees in the production technology department should familiarize themselves with key components of the continuous casting machine, including the tundish, mold, secondary cooling zone, and straightener.
Understanding how each part functions is crucial for maintaining the efficiency and quality of the casting operation.
The Tundish: Bridging the Gap
The role of the tundish is to act as an intermediary between the ladle, which contains the molten steel, and the mold.
It helps in controlling the flow of the steel and maintaining the desired temperature.
This control is essential to prevent turbulence, which can introduce impurities into the steel.
Moreover, the tundish allows for a smoother transition between ladle changes, which is important for continuous operations.
The Mold: Shaping the Steel
The mold is the next critical component in the continuous casting process.
It is a water-cooled copper tube that shapes the molten steel into the desired semi-finished form.
The mold oscillates to prevent the developing steel shell from sticking and tearing, which can cause defects in the final product.
Understanding mold operation is key to ensuring consistent product quality.
Secondary Cooling Zone: Strengthening the Shell
Once the steel exits the mold, it enters the secondary cooling zone, where water sprays continue to cool it down gradually.
This controlled cooling process is crucial for developing a uniform and strong shell.
The secondary cooling zone must be carefully monitored and adjusted to prevent rapid cooling, which could lead to surface cracks or internal defects.
Operators must ensure optimal cooling rates to maintain product integrity and quality.
Straightening and Cutting: Finalizing Formats
As the steel progresses further, it passes through a straightener to correct any mild bending caused by uneven cooling.
The final step is to cut the solidified steel strand into lengths by using an oxy-fuel torch or shear.
These semi-finished products are then ready for further hot rolling, forging, or other processing steps, depending on the desired end product.
Yield Management in Continuous Casting
Yield management in continuous casting is all about optimizing the process to maximize the amount of quality steel produced from each batch of molten metal.
Achieving high yield rates is crucial for maintaining profitability and reducing waste in steel manufacturing.
Minimizing Defects and Scrap
One aspect of yield management is minimizing defects that can lead to scrap.
Operators must pay close attention to casting parameters, such as mold temperature control and casting speed, to ensure a defect-free operation.
Regular maintenance and testing of equipment also play a critical role in minimizing the likelihood of defects.
Process Optimization Techniques
Advanced process optimization techniques involve the use of modeling and simulation technologies.
These tools can help operators predict and adjust casting conditions to achieve optimal performance.
Data from past casting operations can be analyzed to identify patterns and areas for improvement, thus increasing yield through informed decision-making.
Energy Efficiency and Cost Considerations
Energy efficiency is another important factor in yield management.
By optimizing energy consumption across the process, plants can reduce costs and environmental impact.
Improved energy utilization also contributes to better process stability, quality, and overall yield.
Training and Skill Development
Investing in employee training and skill development is crucial for successful yield management.
Properly trained employees are more adept at recognizing potential issues and responding accordingly.
Regular training sessions can keep new employees updated with the latest best practices and technological advancements.
Continuous Improvement and Innovation
The steel industry is continually evolving, with new technologies and processes emerging to further enhance continuous casting and yield management.
New employees should embrace these changes and be willing to adapt to new methods and tools.
Encouraging a culture of continuous improvement and innovation will help steel plants remain competitive in a global market.
Leveraging Technology
Emerging technologies like artificial intelligence and IoT can provide valuable insights for improving operations.
By leveraging these technologies, steel manufacturers can monitor, analyze, and refine their continuous casting processes more effectively.
Sustainability Initiatives
Sustainability is becoming increasingly important in the steel industry.
Efforts to reduce waste, improve energy efficiency, and minimize environmental impact are crucial components of modern yield management strategies.
A focus on sustainability not only supports compliance with regulations but also strengthens the company’s reputation and long-term viability.
In conclusion, gaining an understanding of continuous casting technology and yield management is essential for new employees in the production technology department of the steel industry.
By familiarizing themselves with the process components, optimizing yield, and embracing continuous improvement, they can contribute significantly to their organization’s success.
資料ダウンロード
QCD調達購買管理クラウド「newji」は、調達購買部門で必要なQCD管理全てを備えた、現場特化型兼クラウド型の今世紀最高の購買管理システムとなります。
ユーザー登録
調達購買業務の効率化だけでなく、システムを導入することで、コスト削減や製品・資材のステータス可視化のほか、属人化していた購買情報の共有化による内部不正防止や統制にも役立ちます。
NEWJI DX
製造業に特化したデジタルトランスフォーメーション(DX)の実現を目指す請負開発型のコンサルティングサービスです。AI、iPaaS、および先端の技術を駆使して、製造プロセスの効率化、業務効率化、チームワーク強化、コスト削減、品質向上を実現します。このサービスは、製造業の課題を深く理解し、それに対する最適なデジタルソリューションを提供することで、企業が持続的な成長とイノベーションを達成できるようサポートします。
オンライン講座
製造業、主に購買・調達部門にお勤めの方々に向けた情報を配信しております。
新任の方やベテランの方、管理職を対象とした幅広いコンテンツをご用意しております。
お問い合わせ
コストダウンが利益に直結する術だと理解していても、なかなか前に進めることができない状況。そんな時は、newjiのコストダウン自動化機能で大きく利益貢献しよう!
(Β版非公開)