- お役立ち記事
- A must-see for managers of quality control departments in the electronic component manufacturing industry! How to improve customer satisfaction with quality function deployment (QFD)
A must-see for managers of quality control departments in the electronic component manufacturing industry! How to improve customer satisfaction with quality function deployment (QFD)
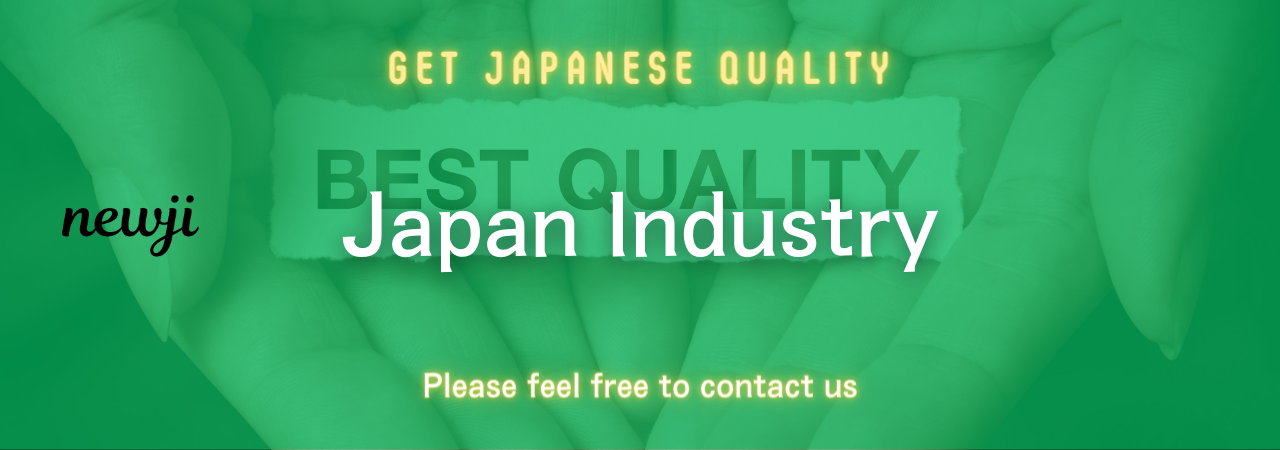
目次
Understanding Quality Function Deployment (QFD)
Quality Function Deployment (QFD) is a powerful tool used in the manufacturing industry to enhance product quality and customer satisfaction.
Originating from Japan, QFD helps manufacturers better understand customer needs and translate them into specific plans to improve their products.
In the electronic component manufacturing industry, where precision and quality are key, QFD can be a game-changer for quality control managers.
QFD is a structured methodology that focuses on the customer’s voice and integrates it into the product development process.
It aims to identify what customers truly need and aligns the manufacturing process to meet those needs effectively.
The Importance of Customer Satisfaction
In today’s competitive marketplace, customer satisfaction is crucial for maintaining a successful business.
Satisfied customers not only foster brand loyalty but also act as ambassadors, bringing in more customers through positive word-of-mouth.
For electronic component manufacturers, where competition is intense, keeping customers happy can significantly impact a company’s market position and profitability.
Customer satisfaction is not just about meeting basic expectations; it’s about exceeding them.
By using QFD, quality control managers can ensure that customer demands are not only met but are exceeded, creating a competitive advantage in the marketplace.
Implementing QFD in Quality Management
Implementing QFD in the manufacturing process involves several steps.
Firstly, it is essential to capture the “Voice of the Customer” (VOC).
This involves collecting input from customers through surveys, interviews, and feedback forms to understand what they truly value in electronic components.
Once the VOC is understood, the development process moves to a series of matrices that help translate these needs into specific technical requirements.
The first matrix is the “House of Quality,” which focuses on aligning customer needs with the company’s capabilities to deliver them.
This matrix helps in setting priorities and determining which features are most important to customers.
Subsequent matrices deal with part deployment, process planning, and production planning, ensuring that every stage of the manufacturing process aligns with customer desires and expectations.
Benefits of Using QFD
The benefits of using QFD in quality control are substantial.
QFD helps in reducing time to market by streamlining the development process and minimizing redesigns.
It also improves communication within departments, as it requires collaboration among marketing, design, engineering, and quality control teams.
In addition, QFD enables the identification of critical quality attributes, allowing manufacturers to focus on improving those areas most valued by customers.
This targeted approach ensures resources are used efficiently, resulting in better product quality and increased customer satisfaction.
Challenges and Solutions
While QFD offers many benefits, its implementation can come with challenges.
One primary challenge is resistance to change within an organization.
Employees accustomed to traditional processes may be hesitant to adopt a new methodology.
To overcome this, it is important to provide adequate training and to emphasize the benefits of QFD.
Demonstrating successful case studies where QFD improved product quality and satisfaction can help alleviate concerns.
Another challenge is ensuring accurate and comprehensive data collection for VOC.
To address this, use multiple data collection methods and ensure active communication with customers to gather detailed and reliable information.
The Role of Technology in QFD
Technology plays a significant role in the effective implementation of QFD.
Software tools can simplify the complex QFD process by automating matrices and data analysis.
These tools can enhance collaboration across departments by providing a centralized platform for input and feedback, ensuring that all team members are aligned with customer expectations.
Moreover, advancements in data analytics allow for deeper insights into customer preferences and emerging trends, enabling more informed decision-making in product development.
Real-World Example
Consider a company manufacturing advanced electronic components for consumer electronics.
By implementing QFD, they were able to identify a key customer need for longer battery life in their components.
This discovery allowed them to shift focus towards enhancing battery efficiency without compromising on other component features.
Using QFD, the company adjusted its production processes accordingly, ultimately resulting in a significant increase in customer satisfaction and sales.
This example illustrates how QFD can directly impact a company’s bottom line by aligning production with customer needs.
Conclusion
For quality control managers in the electronic component manufacturing industry, adopting Quality Function Deployment (QFD) can lead to significant improvements in customer satisfaction.
By focusing on the customer’s voice and systematically aligning production processes to meet those needs, companies can create a competitive advantage, enhance product quality, and reduce time to market.
While challenges exist in implementing QFD, the benefits, supported by modern technology, outweigh these hurdles, making it a valuable strategy in today’s market.
With QFD, manufacturers can not only meet but exceed customer expectations, ensuring long-term success and profitability.
資料ダウンロード
QCD調達購買管理クラウド「newji」は、調達購買部門で必要なQCD管理全てを備えた、現場特化型兼クラウド型の今世紀最高の購買管理システムとなります。
ユーザー登録
調達購買業務の効率化だけでなく、システムを導入することで、コスト削減や製品・資材のステータス可視化のほか、属人化していた購買情報の共有化による内部不正防止や統制にも役立ちます。
NEWJI DX
製造業に特化したデジタルトランスフォーメーション(DX)の実現を目指す請負開発型のコンサルティングサービスです。AI、iPaaS、および先端の技術を駆使して、製造プロセスの効率化、業務効率化、チームワーク強化、コスト削減、品質向上を実現します。このサービスは、製造業の課題を深く理解し、それに対する最適なデジタルソリューションを提供することで、企業が持続的な成長とイノベーションを達成できるようサポートします。
オンライン講座
製造業、主に購買・調達部門にお勤めの方々に向けた情報を配信しております。
新任の方やベテランの方、管理職を対象とした幅広いコンテンツをご用意しております。
お問い合わせ
コストダウンが利益に直結する術だと理解していても、なかなか前に進めることができない状況。そんな時は、newjiのコストダウン自動化機能で大きく利益貢献しよう!
(Β版非公開)