- お役立ち記事
- How to create a “Process Improvement Plan”—How to proceed with a project based on instructions from management
How to create a “Process Improvement Plan”—How to proceed with a project based on instructions from management
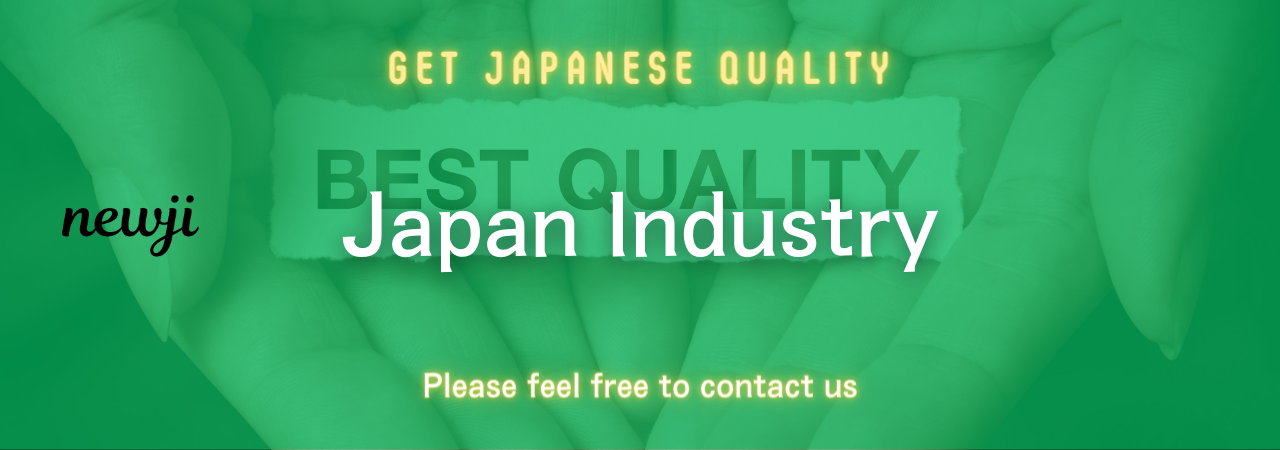
目次
Understanding the Importance of a Process Improvement Plan
Before diving into the steps to create a process improvement plan, it’s essential to understand why it matters.
A process improvement plan is a strategic approach to identifying, analyzing, and improving existing business processes.
The goal is to enhance performance, meet best practice standards, and increase customer satisfaction.
Management often identifies the need for improvement to stay competitive, efficient, and cost-effective.
An effective process improvement plan can lead to reduced process times, increased efficiency, and improved product or service quality.
This plan is crucial for responding to evolving market demands and improving operational performance.
Initial Steps in Creating a Process Improvement Plan
The creation of a process improvement plan typically begins with management’s directive.
Here are the key initial steps to take:
Define Objectives and Scope
Clearly define what you want to achieve with the process improvement.
Whether it’s reducing costs, enhancing efficiency, or improving product quality, specific objectives will guide your plan.
Determine the scope of the process that will be examined.
Decide whether it pertains to a single department or spans multiple areas of the organization.
Gather and Analyze Data
Collect data on current processes to understand how things are done.
This may include reviewing process documentation, conducting interviews with staff, and observing workflows.
Analyze the data to identify bottlenecks, redundancies, and areas that require enhancements.
Use qualitative and quantitative data to understand the current performance of processes.
Developing the Process Improvement Plan
Once the preliminary steps are complete, move on to develop the plan itself.
Map Out the Current Process
Creating a visual representation of the current process is crucial.
Use flowcharts or diagrams to illustrate each step of the process.
This will help identify inefficiencies and streamline communication among team members regarding the process.
Identify Improvement Opportunities
Based on the data analysis and current process map, pinpoint specific areas that need improvement.
This could include eliminating unnecessary steps, automating manual tasks, or reallocating resources.
Consider the potential impact of these changes on overall process efficiency and employee workload.
Implementation of the Process Improvement Plan
With a clear understanding of necessary improvements, develop an implementation strategy.
Develop an Action Plan
Create a detailed action plan that outlines the steps required to implement improvements.
Assign roles and responsibilities to team members, and set deadlines for each task.
Make sure to include a communication plan to inform all stakeholders of changes.
Provide Training and Resources
Employees may require additional training to adapt to new processes or technologies.
Ensure that all necessary resources are available for them to perform their tasks efficiently.
This investment in human capital is crucial for successful implementation.
Monitoring and Continuous Improvement
A process improvement plan doesn’t end with implementation.
Ongoing monitoring and refinement are essential for long-term success.
Monitor Progress
Regularly track the performance of the new process to ensure it meets the desired objectives.
Use key performance indicators (KPIs) to measure success and identify areas that need further refinement.
Encourage Feedback
Solicit feedback from employees and stakeholders about the new process.
Their insights can provide valuable information that may help refine the process further.
Encouraging open communication fosters a culture of continuous improvement.
Review and Adjust
Based on feedback and performance metrics, make necessary adjustments to the process.
Regular review ensures that the process continues to evolve in line with business needs and external market changes.
Conclusion
Creating a process improvement plan involves a structured approach that begins with management’s directive and continues through several critical stages.
By focusing on defining objectives, analyzing data, identifying opportunities, implementing changes, and ensuring continuous monitoring, businesses can achieve notable improvements in efficiency and effectiveness.
A well-constructed process improvement plan not only enhances current operations but also positions the organization for future success and adaptability in a dynamic market.
資料ダウンロード
QCD調達購買管理クラウド「newji」は、調達購買部門で必要なQCD管理全てを備えた、現場特化型兼クラウド型の今世紀最高の購買管理システムとなります。
ユーザー登録
調達購買業務の効率化だけでなく、システムを導入することで、コスト削減や製品・資材のステータス可視化のほか、属人化していた購買情報の共有化による内部不正防止や統制にも役立ちます。
NEWJI DX
製造業に特化したデジタルトランスフォーメーション(DX)の実現を目指す請負開発型のコンサルティングサービスです。AI、iPaaS、および先端の技術を駆使して、製造プロセスの効率化、業務効率化、チームワーク強化、コスト削減、品質向上を実現します。このサービスは、製造業の課題を深く理解し、それに対する最適なデジタルソリューションを提供することで、企業が持続的な成長とイノベーションを達成できるようサポートします。
オンライン講座
製造業、主に購買・調達部門にお勤めの方々に向けた情報を配信しております。
新任の方やベテランの方、管理職を対象とした幅広いコンテンツをご用意しております。
お問い合わせ
コストダウンが利益に直結する術だと理解していても、なかなか前に進めることができない状況。そんな時は、newjiのコストダウン自動化機能で大きく利益貢献しよう!
(Β版非公開)