- お役立ち記事
- Introduction of ATP testing and strengthening of hygiene management that managers of quality assurance departments in the food processing industry should keep in mind
Introduction of ATP testing and strengthening of hygiene management that managers of quality assurance departments in the food processing industry should keep in mind
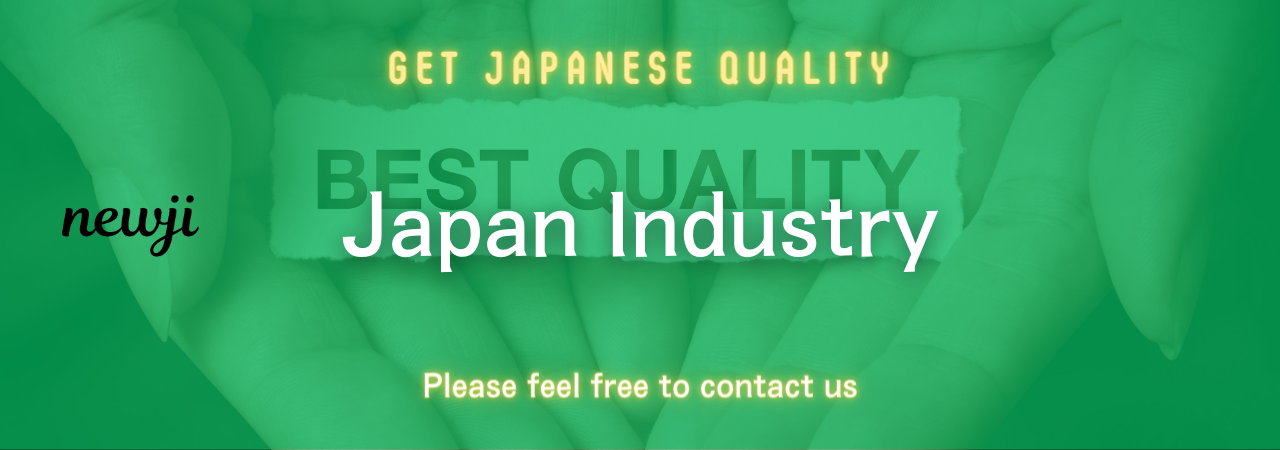
目次
Understanding ATP Testing
ATP testing stands for Adenosine Triphosphate testing.
It’s a method used to measure the level of hygiene on surfaces.
ATP is a molecule found in all living cells, including bacteria.
When you measure ATP levels, you’re essentially determining how much organic matter is present.
In the food processing industry, cleanliness is crucial for ensuring product safety.
ATP testing provides a quick and reliable way to verify cleaning effectiveness.
ATP meters, also known as luminometers, are used to read ATP levels.
A swab is used to collect a sample from a surface.
This swab is then placed in the meter, which calculates the ATP concentration.
The result is displayed in Relative Light Units (RLU).
Lower RLU readings indicate better hygiene, while higher readings suggest inadequate cleaning.
The speed and ease of ATP testing make it a valuable tool for maintaining hygiene standards.
Why Hygiene Management Matters
Hygiene management is essential in the food processing industry.
It ensures that products are safe for consumption.
Contaminated food can lead to severe health risks and financial consequences.
Effective hygiene management can prevent these issues from arising.
Proper cleanliness in processing facilities minimizes the risk of foodborne diseases.
Maintaining a hygienic environment also enhances the reputation of a brand.
Consumers trust companies that prioritize safety and cleanliness.
Moreover, adhering to hygiene standards ensures regulatory compliance.
Failing to meet these standards can lead to fines and legal troubles.
Therefore, it’s crucial for quality assurance departments to implement robust hygiene management practices.
How ATP Testing Helps with Hygiene Management
ATP testing plays a significant role in strengthening hygiene management.
It provides immediate feedback on cleaning effectiveness.
This allows managers to address potential issues right away.
Frequent ATP testing helps in identifying trends in hygiene over time.
By tracking RLU readings, managers can pinpoint areas that need improvement.
Moreover, ATP testing covers both visible and invisible contaminants.
Traditional cleaning methods may overlook harmful microbes or organic residues.
With ATP testing, you get a comprehensive view of surface cleanliness.
It’s a proactive approach to hygiene management that can prevent future problems.
Integrating ATP testing into regular cleaning routines ensures better overall hygiene.
Steps to Implement ATP Testing in Food Processing
Implementing ATP testing in the food processing environment involves a few strategic steps.
First, educate your staff on the importance of hygiene and the role of ATP testing.
Training sessions should cover how to correctly use ATP meters.
This knowledge ensures everyone understands how to take accurate readings.
Next, develop a testing schedule based on your facility’s needs.
Some areas may require more frequent testing due to higher contamination risks.
For consistency, stick to the plan and make adjustments as necessary.
It’s essential to keep detailed records of all ATP test results.
These records can help identify patterns and inform future cleaning strategies.
Collaboration between departments is also vital for successful ATP implementation.
Ensure communication between quality control, cleaning staff, and management.
This teamwork ensures that everyone is aligned with the hygiene goals.
Finally, regularly review and update your hygiene protocols based on outcomes.
Continual improvement is key to maintaining high cleanliness standards.
Challenges and Solutions in ATP Testing
Despite its advantages, ATP testing has some challenges.
One challenge is that ATP does not differentiate between different types of microbes.
It measures both harmful and harmless residues.
However, it still indicates cleaning efficiency, which is the primary concern.
Another challenge is ensuring consistent testing across all staff members.
Variations in technique can result in inaccurate readings.
Regular training and audits help mitigate this issue.
Calibration of ATP meters is another critical consideration.
Routine checks ensure that meters provide accurate readings.
Financial constraints might also pose a challenge for some organizations.
However, long-term benefits such as reduced contamination and fewer quality issues justify the investment.
Ultimately, overcoming these challenges involves commitment and ongoing education.
Future Trends in Hygiene Management
Hygiene management is continuously evolving in response to new technologies.
Automation and smart technologies are making ATP testing even more efficient.
For example, some companies are developing systems with automated swabbing robots.
These technologies ensure consistency and remove the potential for human error.
Additionally, data analytics is playing a crucial role in hygiene management.
Analyzing ATP test data can provide insights into cleaning practices.
This information helps in refining cleaning protocols and improving hygiene outcomes.
Virtual reality (VR) training is another emerging trend.
VR can offer hands-on training for staff, enhancing their understanding of hygiene processes.
As technology continues to advance, the future of hygiene management looks promising.
Keeping abreast of these trends ensures that food processing facilities remain safe and compliant.
Conclusion
For managers in quality assurance departments, ATP testing is an invaluable tool.
It provides objective data on cleanliness and helps strengthen hygiene management.
Implementing ATP testing requires planning, training, and collaboration.
Despite some challenges, the benefits outweigh the initial difficulties.
Staying informed about future trends can further enhance hygiene practices.
Ensuring food safety requires a commitment to cleanliness.
With ATP testing, managers can uphold high standards of hygiene and protect consumers.
Such efforts not only safeguard public health but also secure the integrity of the brand.
資料ダウンロード
QCD調達購買管理クラウド「newji」は、調達購買部門で必要なQCD管理全てを備えた、現場特化型兼クラウド型の今世紀最高の購買管理システムとなります。
ユーザー登録
調達購買業務の効率化だけでなく、システムを導入することで、コスト削減や製品・資材のステータス可視化のほか、属人化していた購買情報の共有化による内部不正防止や統制にも役立ちます。
NEWJI DX
製造業に特化したデジタルトランスフォーメーション(DX)の実現を目指す請負開発型のコンサルティングサービスです。AI、iPaaS、および先端の技術を駆使して、製造プロセスの効率化、業務効率化、チームワーク強化、コスト削減、品質向上を実現します。このサービスは、製造業の課題を深く理解し、それに対する最適なデジタルソリューションを提供することで、企業が持続的な成長とイノベーションを達成できるようサポートします。
オンライン講座
製造業、主に購買・調達部門にお勤めの方々に向けた情報を配信しております。
新任の方やベテランの方、管理職を対象とした幅広いコンテンツをご用意しております。
お問い合わせ
コストダウンが利益に直結する術だと理解していても、なかなか前に進めることができない状況。そんな時は、newjiのコストダウン自動化機能で大きく利益貢献しよう!
(Β版非公開)