- お役立ち記事
- Reducing energy consumption by optimizing the operating conditions of electric arc furnaces, which managers of production technology departments in the steel industry should know about
Reducing energy consumption by optimizing the operating conditions of electric arc furnaces, which managers of production technology departments in the steel industry should know about
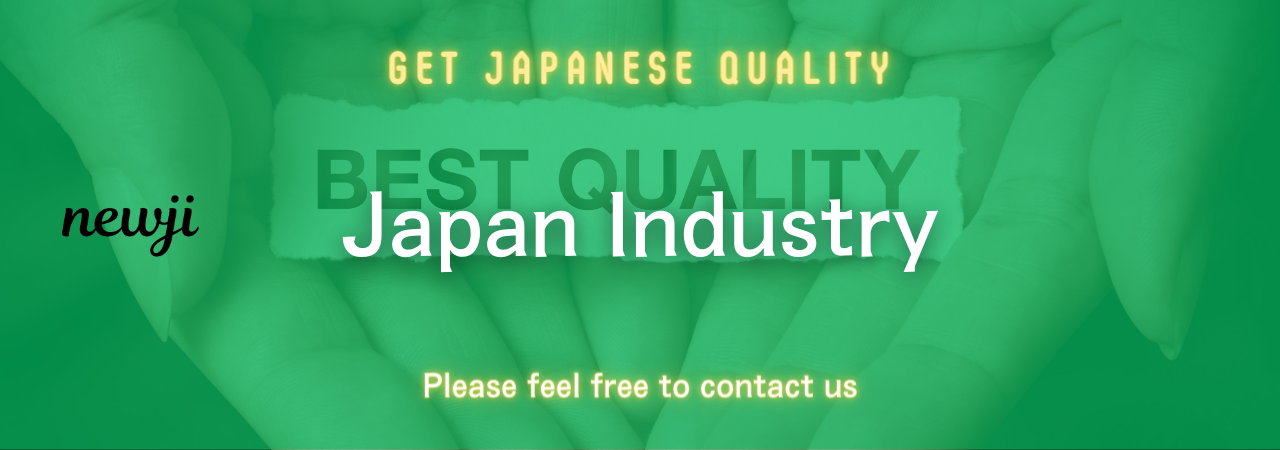
目次
Introduction to Electric Arc Furnaces
Electric Arc Furnaces (EAFs) play a crucial role in the steel industry by melting scrap metal to produce steel, an essential material for construction, manufacturing, and countless other applications.
These furnaces use electrical energy to generate intense heat, transforming scrap metal into molten steel.
This process, while effective, can be energy-intensive, making it important for industry professionals to find ways to optimize energy consumption and reduce operational costs.
Understanding Energy Consumption in EAFs
The energy consumption of an electric arc furnace depends on several factors, including the quality of scrap metal, furnace design, and the efficiency of the operation.
Given the extensive energy requirements of EAFs, optimizing these factors can lead to substantial cost savings and reduced environmental impact.
Before diving into the optimization methods, it is essential to understand where the energy is consumed during the process.
Typically, energy is used for melting, refining, and maintaining the temperature of the molten steel.
Factors Affecting Energy Consumption
Several factors influence energy consumption in electric arc furnaces:
1. **Scrap Quality:** The composition and cleanliness of scrap metal significantly impact energy needs since impurities can necessitate additional processing.
2. **Furnace Design:** Advances in technology and design can lead to more efficient energy use by improving heat transfer and reducing energy loss.
3. **Operational Practices:** Efficient management practices, such as optimizing charging systems and minimizing downtime, can lead to energy savings.
Techniques for Optimizing Operating Conditions
Optimizing the operating conditions of electric arc furnaces involves adopting strategies that minimize energy use while maintaining production quality.
Here are some techniques that managers of production technology departments in the steel industry should consider:
1. Control of Energy Inputs
Managing the energy input into EAFs can significantly impact energy consumption.
This can be achieved through techniques such as:
– **Power Input Control:** Adjusting the power input to match the characteristics of the scrap metal, ensuring efficient melting.
– **Electrode Regulation:** Maintaining optimal arc length, which reduces energy waste and prolongs electrode life.
2. Scrap Preheating
Preheating scrap metal before it enters the furnace can help reduce the energy required for melting.
This process involves utilizing waste heat from the furnace exhaust to raise the temperature of the incoming scrap, leading to lower overall energy consumption.
3. Oxygen Lancing
Introducing oxygen directly into the furnace through lancing enhances combustion and accelerates the melting process.
This technique not only reduces melting time but also decreases energy consumption, as less electricity is required to melt the scrap.
4. Slag Foaming
Slag foaming involves creating a layer of foamed slag, which acts as a thermal insulator to trap heat within the furnace.
This method improves energy efficiency by reducing heat loss, allowing the furnace to maintain temperature while consuming less energy.
5. Furnace Design Improvements
Investing in modern furnace designs that incorporate advanced technologies can yield significant energy savings.
Examples include furnaces equipped with efficient burners, enhanced refractory materials, and better heat recovery systems.
Monitoring and Maintenance for Continuous Improvement
Regular monitoring and maintenance of electric arc furnaces are essential for sustaining optimized energy consumption.
Implement a robust monitoring system to track energy use and identify areas for improvement.
Key considerations include:
1. Regular Audits
Conducting regular audits of the furnace’s energy use can help identify inefficiencies and areas where improvements can be made.
These audits should encompass all aspects of the operation, from the energy input to scrap management and melting processes.
2. Equipment Upgrades
Investing in periodic equipment upgrades ensures that furnaces operate efficiently.
Replacing outdated components with modern, energy-efficient alternatives can result in significant energy savings over time.
3. Staff Training
Ensure that all personnel operating the furnaces are adequately trained in energy-efficient practices.
Continuous education and training programs can keep staff informed of the latest techniques and technologies for reducing energy consumption.
Economic and Environmental Benefits
Optimizing the operating conditions of electric arc furnaces not only reduces energy consumption but also offers numerous economic and environmental benefits.
Economically, reduced energy costs translate directly into higher profit margins for steel manufacturers.
Efficient EAF operations can also enhance productivity by minimizing downtime and maintenance requirements.
From an environmental perspective, using less energy reduces the carbon footprint of steel production.
This aligns with sustainability goals and responds to increasing regulatory and consumer pressures for environmentally responsible manufacturing practices.
Conclusion
Reducing energy consumption in electric arc furnaces requires a comprehensive approach that includes optimizing operational practices, employing advanced technologies, and maintaining rigorous monitoring and maintenance routines.
By implementing these strategies, managers in the steel industry can achieve substantial cost savings and contribute to a more sustainable manufacturing process.
Staying informed about the latest advancements in EAF technology is crucial, as the steel industry continues to evolve in response to economic and environmental challenges.
Through commitment and innovation, optimizing the operating conditions of electric arc furnaces represents a significant opportunity for progress in energy efficiency.
資料ダウンロード
QCD調達購買管理クラウド「newji」は、調達購買部門で必要なQCD管理全てを備えた、現場特化型兼クラウド型の今世紀最高の購買管理システムとなります。
ユーザー登録
調達購買業務の効率化だけでなく、システムを導入することで、コスト削減や製品・資材のステータス可視化のほか、属人化していた購買情報の共有化による内部不正防止や統制にも役立ちます。
NEWJI DX
製造業に特化したデジタルトランスフォーメーション(DX)の実現を目指す請負開発型のコンサルティングサービスです。AI、iPaaS、および先端の技術を駆使して、製造プロセスの効率化、業務効率化、チームワーク強化、コスト削減、品質向上を実現します。このサービスは、製造業の課題を深く理解し、それに対する最適なデジタルソリューションを提供することで、企業が持続的な成長とイノベーションを達成できるようサポートします。
オンライン講座
製造業、主に購買・調達部門にお勤めの方々に向けた情報を配信しております。
新任の方やベテランの方、管理職を対象とした幅広いコンテンツをご用意しております。
お問い合わせ
コストダウンが利益に直結する術だと理解していても、なかなか前に進めることができない状況。そんな時は、newjiのコストダウン自動化機能で大きく利益貢献しよう!
(Β版非公開)