- お役立ち記事
- Product stability testing and packaging improvement measures that quality assurance leaders in the cosmetics manufacturing industry should know.
Product stability testing and packaging improvement measures that quality assurance leaders in the cosmetics manufacturing industry should know.
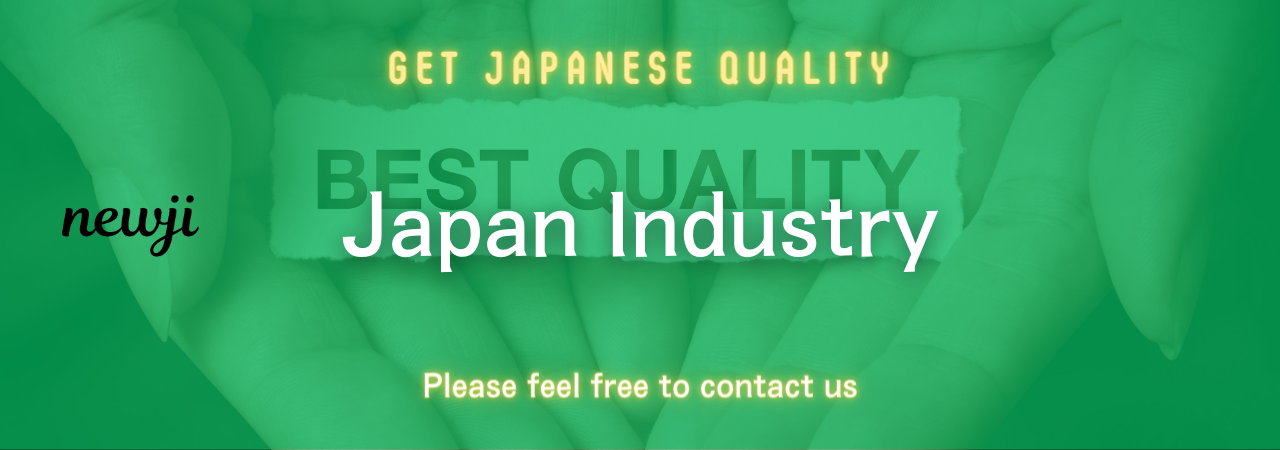
目次
Understanding Product Stability Testing
Product stability testing is a critical component in the cosmetics manufacturing industry.
It involves evaluating how a product maintains its quality over time, under various environmental conditions, such as light, temperature, and humidity.
Stability testing ensures that products will perform effectively and safely from the time they are manufactured until the end of their shelf lives.
Quality assurance leaders play a pivotal role in determining the protocols for these tests.
By designing effective stability testing procedures, these leaders can predict potential product degradation and make informed decisions about formulation adjustments.
The Importance of Stability Testing
Product stability is essential for maintaining consumer trust and safety.
Cosmetics that degrade over time can lose efficacy, develop unpleasant odors, discolor, or separate into components, making them less appealing and potentially unsafe.
Through stability testing, manufacturers can set accurate expiration dates, ensuring customers receive products that work as expected throughout their intended shelf life.
Moreover, regulatory bodies like the Food and Drug Administration (FDA) or the European Medicines Agency (EMA) require documented evidence of product stability.
Without this testing, companies risk non-compliance and potential recalls, which can be costly and damaging to brand reputation.
Key Elements of Stability Testing
Quality assurance leaders must consider several key elements when conducting stability tests.
These include the selection of batches for testing, the environmental factors to be simulated, and the duration of testing.
Consistency is crucial in selecting representative batches, as variations can lead to inaccurate results.
Environmental factors such as temperature, humidity, and light exposure mimic real-world conditions the product might face in storage and use.
For instance, high-temperature testing can simulate the potential effects of products stored in warm climates, while light exposure tests assess the product’s resistance to degradation from UV rays.
Duration of testing is also essential, typically spanning from six months to two years, with assessments at multiple intervals.
This timeline offers a comprehensive view of how a product behaves over time and under different conditions.
Accelerated vs. Real-Time Testing
There are two primary types of stability testing: accelerated and real-time.
Accelerated testing uses elevated stress conditions to hasten the degradation process, providing quick insights into product stability.
This method is useful for early detection of stability issues and setting preliminary expiration dates.
In contrast, real-time testing simulates normal storage conditions and offers the most accurate representation of product performance over its actual shelf life.
While more time-consuming than accelerated testing, it is crucial for confirming the predictions made during accelerated tests and is often required for compliance with regulatory standards.
Packaging Improvement Measures
Packaging plays a vital role in product stability, as it protects cosmetics from environmental factors that can cause degradation.
Quality assurance leaders should work closely with packaging engineers to design solutions that enhance product longevity and safety.
Choosing the Right Materials
The selection of packaging materials is critical in protecting products from external elements.
Glass and metal are excellent barriers to moisture and oxygen, while certain plastics can offer significant UV protection.
However, material choice should consider the product’s chemical composition to avoid reactions that could impair product quality.
Testing packaging materials for compatibility with the product is also essential.
Incompatibility can lead to reactions that compromise product integrity, causing off-odors, color changes, or other undesirable effects.
Innovative Packaging Solutions
Incorporating innovative packaging technologies can further enhance product stability.
For example, airless pumps minimize the product’s exposure to air, reducing oxidation and microbial growth.
Light-blocking coatings or UV-filtering containers can protect light-sensitive products, maintaining their effectiveness and appearance.
Additionally, smart packaging solutions, such as time-temperature indicators, can inform consumers about the proper storage of products.
These features provide users with valuable information to detect if products have been exposed to unsuitable conditions that could affect performance and safety.
Regular Assessment and Improvement
Continuous evaluation of both product stability and packaging efficacy is crucial for maintaining the highest quality standards in the cosmetics manufacturing industry.
Quality assurance leaders should establish routine review processes to assess ongoing stability data and packaging performance.
Feedback from consumers and retailers can offer insights into real-world product and packaging performance, guiding further improvements.
By staying proactive and responsive to data, manufacturers can continuously enhance product stability and packaging, ensuring quality and safety that meets regulatory and consumer expectations.
Structured collaboration between product development, quality assurance, and packaging teams will facilitate the implementation of effective solutions and foster a company culture committed to excellence.
In conclusion, for quality assurance leaders in the cosmetics manufacturing industry, a comprehensive approach to product stability testing and packaging improvements is indispensable.
Focusing on these areas helps safeguard product integrity, consumer trust, and brand reputation, ensuring success in a competitive market.
資料ダウンロード
QCD調達購買管理クラウド「newji」は、調達購買部門で必要なQCD管理全てを備えた、現場特化型兼クラウド型の今世紀最高の購買管理システムとなります。
ユーザー登録
調達購買業務の効率化だけでなく、システムを導入することで、コスト削減や製品・資材のステータス可視化のほか、属人化していた購買情報の共有化による内部不正防止や統制にも役立ちます。
NEWJI DX
製造業に特化したデジタルトランスフォーメーション(DX)の実現を目指す請負開発型のコンサルティングサービスです。AI、iPaaS、および先端の技術を駆使して、製造プロセスの効率化、業務効率化、チームワーク強化、コスト削減、品質向上を実現します。このサービスは、製造業の課題を深く理解し、それに対する最適なデジタルソリューションを提供することで、企業が持続的な成長とイノベーションを達成できるようサポートします。
オンライン講座
製造業、主に購買・調達部門にお勤めの方々に向けた情報を配信しております。
新任の方やベテランの方、管理職を対象とした幅広いコンテンツをご用意しております。
お問い合わせ
コストダウンが利益に直結する術だと理解していても、なかなか前に進めることができない状況。そんな時は、newjiのコストダウン自動化機能で大きく利益貢献しよう!
(Β版非公開)