- お役立ち記事
- New employees in the quality control department should learn the basics of QC process charts and how to use them on site.
New employees in the quality control department should learn the basics of QC process charts and how to use them on site.
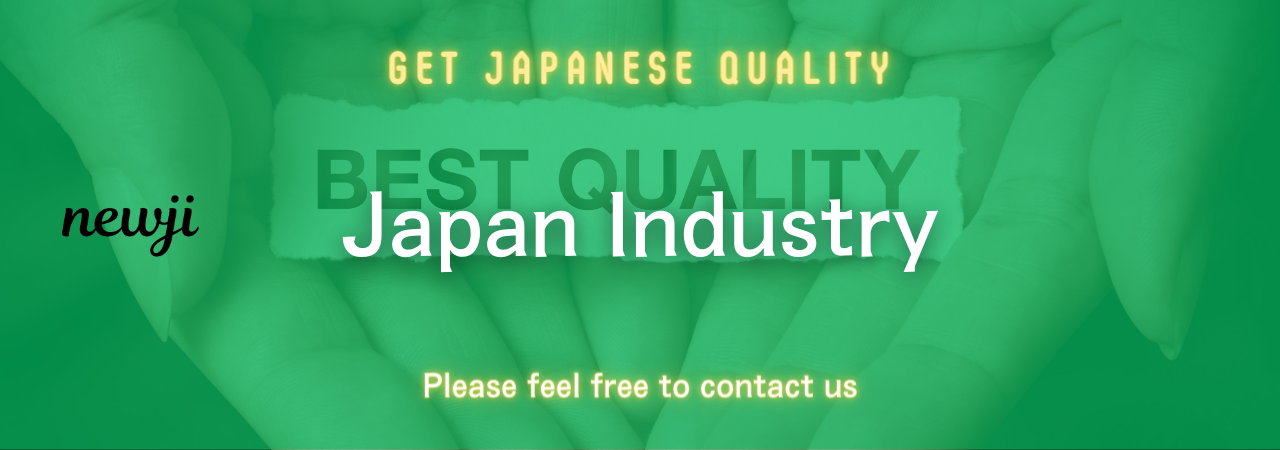
目次
Understanding QC Process Charts
Quality Control (QC) process charts are vital tools used in maintaining and improving the quality of products and services.
These charts visually display data and help identify trends, variations, and potential issues in the production process.
For new employees in the quality control department, learning the basics of QC process charts is an essential step toward effective quality management.
The most common types of QC charts include Pareto charts, flowcharts, control charts, histogram, scatter diagrams, and cause-and-effect diagrams.
Each type serves a unique purpose, offering different insights into the process quality.
Pareto Charts
Pareto charts, named after economist Vilfredo Pareto, use bars and a line graph to highlight the most significant factors in a dataset.
The bars show the individual values in descending order, while the line graph represents the cumulative total percentage.
This dual representation helps easily identify the ‘vital few’ factors that need attention, supporting the Pareto Principle that 80% of problems come from 20% of causes.
Flowcharts
Flowcharts provide a visual representation of the step-by-step sequence of operations in a process.
These charts use various symbols to denote different actions or steps, clarifying the workflow and making it easier to spot inefficiencies or redundancies.
Understanding a flowchart enables a new employee to grasp the entire scope of operations within their department or company.
Control Charts
Control charts are used to study how a process changes over time.
They display data in a time-ordered sequence, with a central line representing the average, an upper control line, and a lower control line.
By observing data points in these charts, employees can determine if the process operates consistently or if any variations exist that require examination or rectification.
Histograms
Histograms are bar graphs that depict the frequency distribution of a set of data.
By categorizing data into different ranges or bins, histograms provide insight into the distribution pattern of a process.
This is particularly useful for visualizing large datasets and checking for deviations from the standard distribution.
Scatter Diagrams
Scatter diagrams plot individual values as coordinates on a graph to examine the relationship between two variables.
The pattern formed by the points can reveal correlations or causal relationships.
Understanding these relationships aids QC personnel in identifying underlying issues that may impact product quality.
Cause-and-Effect Diagrams
Also known as fishbone or Ishikawa diagrams, these charts help identify potential causes of a specific problem or effect.
By organizing various factors that could be contributing to an issue, these diagrams assist in pinpointing root causes in order to devise effective solutions.
Using QC Process Charts on Site
QC process charts are essential not only for visual analysis but also for onsite application.
Understanding how to use them practically enhances the accuracy and effectiveness of quality control efforts.
Collecting and Analyzing Data
The first step in applying QC charts onsite is collecting accurate and relevant data.
Data collection may involve manual recording, automated systems, or a combination of both.
Accurate data is the foundation of effective charting; without it, the insights drawn are likely to be flawed.
Once data is collected, proper analysis using the appropriate type of chart is necessary.
Choosing the right chart is vital as it determines the quality and type of information extracted.
For instance, Pareto charts may identify significant issues, while control charts help monitor consistency.
Identifying and Solving Problems
One of the primary goals of QC charts is to identify areas needing improvement.
By analyzing these charts, new employees can gain a better understanding of where quality issues may arise within a process.
Once a problem is detected, the next step is to determine the cause and apply corrective actions.
For instance, cause-and-effect diagrams can identify the root causes of a particular failure, helping decide which steps need adjustment.
Implementing Continuous Improvement
Continuous improvement involves making regular, incremental changes to processes to enhance quality and efficiency.
QC process charts play an integral part in this endeavor.
Utilizing them regularly ensures employees spot minor variations before they grow into significant problems.
By implementing the insights gained from QC analysis, employees contribute to the ongoing refinement of company processes and procedures.
This culture of continuous improvement ultimately elevates product quality, benefiting overall customer satisfaction.
Normalizing QC Chart Use Across Teams
For new employees, it’s important to understand that the effectiveness of QC charts is proportional to their standardization and consistent use across the organization.
Teams should work collectively toward this goal for optimal results.
Fostering Communication and Collaboration
Effective use of QC charts requires team members from various departments to communicate and collaborate closely.
For instance, production teams should regularly consult with quality control teams and vice versa, ensuring synergy in adopting QC chart insights.
By working together, teams can leverage collective expertise and experience in identifying process improvements.
Documentation and Training
Comprehensive documentation and training on QC process charts are vital.
Standardized guides and manuals, which detail the types of charts, data interpretation methods, and the steps for chart application, can serve as a valuable resource.
Regular training sessions and workshops should focus on practical applications of QC charts.
Encouraging active participation ensures employees build confidence and expertise in quality control methodologies.
Feedback and Adaptation
Organizations should maintain an iterative feedback loop that seeks employees’ insights into QC chart efficacy and usability.
By gathering, analyzing, and acting on feedback, the company can refine its QC processes to better suit the evolving needs of the workforce.
Listening to employee observations aids the organization in adapting QC charts to be more comprehensive and relevant to current processes.
Conclusion
In conclusion, QC process charts are vital tools for new employees in the quality control department.
Understanding these charts provides the foundation to effectively monitor and improve quality in processes.
By learning to apply chart insights practically and fostering a culture of continuous improvement, employees contribute significantly to the success of the organization.
資料ダウンロード
QCD調達購買管理クラウド「newji」は、調達購買部門で必要なQCD管理全てを備えた、現場特化型兼クラウド型の今世紀最高の購買管理システムとなります。
ユーザー登録
調達購買業務の効率化だけでなく、システムを導入することで、コスト削減や製品・資材のステータス可視化のほか、属人化していた購買情報の共有化による内部不正防止や統制にも役立ちます。
NEWJI DX
製造業に特化したデジタルトランスフォーメーション(DX)の実現を目指す請負開発型のコンサルティングサービスです。AI、iPaaS、および先端の技術を駆使して、製造プロセスの効率化、業務効率化、チームワーク強化、コスト削減、品質向上を実現します。このサービスは、製造業の課題を深く理解し、それに対する最適なデジタルソリューションを提供することで、企業が持続的な成長とイノベーションを達成できるようサポートします。
オンライン講座
製造業、主に購買・調達部門にお勤めの方々に向けた情報を配信しております。
新任の方やベテランの方、管理職を対象とした幅広いコンテンツをご用意しております。
お問い合わせ
コストダウンが利益に直結する術だと理解していても、なかなか前に進めることができない状況。そんな時は、newjiのコストダウン自動化機能で大きく利益貢献しよう!
(Β版非公開)