- お役立ち記事
- Parts lifecycle management that contributes to cost reduction Basic actions that purchasing departments should take
Parts lifecycle management that contributes to cost reduction Basic actions that purchasing departments should take
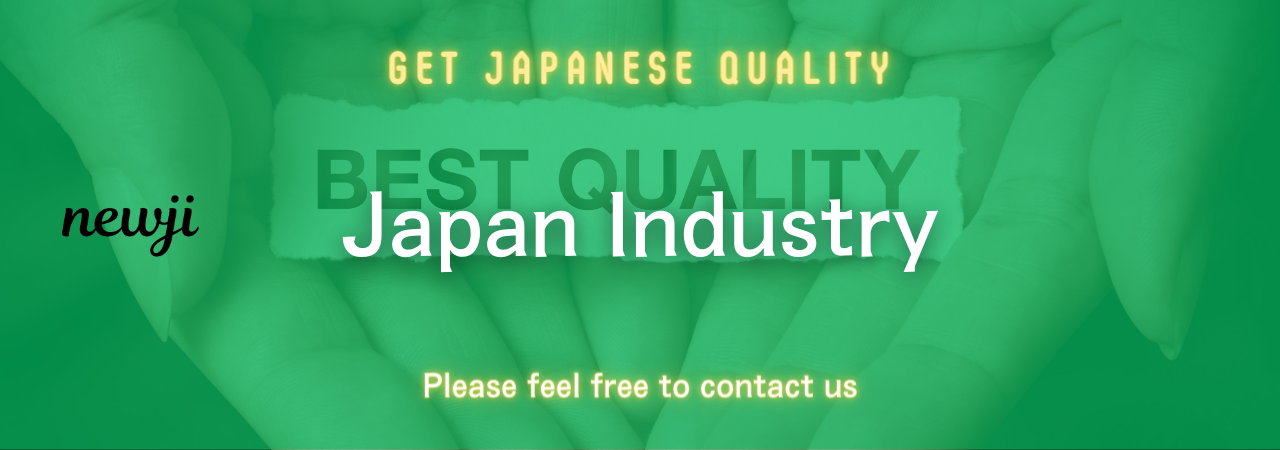
目次
Understanding Parts Lifecycle Management
Parts lifecycle management is a crucial process in any organization that relies on manufactured goods and components.
It involves planning, tracking, and managing the different phases of part usage from acquisition through to disposal.
This comprehensive approach ensures that components are used efficiently and cost-effectively throughout their lifecycle.
The lifecycle of a part typically includes phases such as procurement, utilization, maintenance, and ultimately, disposal or recycling.
When effectively managed, it can lead to significant cost reductions and enhanced operational efficiencies.
Why Parts Lifecycle Management Matters
Understanding and improving the lifecycle of parts can bring multiple benefits to an organization.
Firstly, it aids in reducing costs through the optimization of resource usage and the identification of more efficient processes.
Secondly, it ensures the availability of parts when needed, minimizing downtime and maintaining smooth operations.
Thus, investing time and resources into robust parts lifecycle management is essential.
Phases of Parts Lifecycle Management
To implement effective lifecycle management, organizations must focus on the following phases:
Procurement
Procurement involves sourcing and acquiring parts from suppliers.
By working closely with suppliers, organizations can negotiate better prices, ensuring cost-effective purchases.
It’s also crucial to establish reliable supply chains to reduce the risks of delays and shortages.
During this phase, purchasing departments should carry out thorough market research and supplier evaluations.
This will ensure that they select the most cost-effective and reliable vendors for their needs.
Utilization
Once parts are procured, utilization refers to how these parts are used within the organization.
Optimal utilization ensures that parts are used efficiently, thereby extending their life and maximizing their value.
Proper training for staff on how to handle and use parts correctly is paramount to achieving this.
Moreover, regular performance assessments can identify areas of improvement to further optimize part usage.
Maintenance
The maintenance phase involves regular check-ups and repairs to ensure parts function correctly and last as long as possible.
Proper maintenance reduces the likelihood of unexpected breakdowns, which can lead to increased costs and downtime.
Developing a preventive maintenance schedule helps keep parts in optimal condition.
Routine inspections and timely repairs are vital components of effective maintenance.
Disposal or Recycling
The final phase is disposal or recycling.
Upon reaching the end of their useful life, parts should be responsibly disposed of or recycled.
Recycling components not only supports sustainability efforts but can also lower costs through the reuse of materials.
Developing relationships with recycling partners can help organizations effectively manage this phase and potentially gain from the value of recycled parts.
Contribution to Cost Reduction
Parts lifecycle management directly contributes to cost reduction in multiple ways.
By optimizing each lifecycle stage, organizations can save on unnecessary expenditure and make better use of their resources.
Negotiating Better Prices
One of the primary ways to reduce costs is through negotiating better prices during the procurement phase.
By understanding supplier capabilities and prices, purchasing departments can negotiate favorable terms and discounts.
Bulk buying agreements and long-term partnerships with suppliers can also lead to cost savings.
Enhancing Operational Efficiency
Through effective utilization and maintenance of parts, operational efficiency is significantly enhanced.
This efficiency minimizes waste and reduces the need for frequent replacements, leading to cost savings.
Implementation of lean practices during the parts usage phase can further optimize resource management.
Reducing Downtime
Efficient parts management reduces machine and equipment downtime.
When parts are available and well-maintained, they contribute to continuous production cycles without interruptions.
A well-organized inventory system and preventive maintenance play crucial roles in avoiding unplanned downtimes.
Extending Parts Lifespan
Regular maintenance and proper usage extend the lifespan of parts considerably.
By doing so, organizations can delay the need for replacements, thereby reducing long-term costs.
Training staff and maintaining an up-to-date maintenance schedule are simple yet effective actions to prolong part longevity.
Actions for Purchasing Departments
To leverage parts lifecycle management for cost reduction, purchasing departments can take several actions:
Develop Strong Supplier Relationships
Building strong relationships with suppliers is essential.
It aids in securing better deals, reliable deliveries, and early access to new technologies.
Regular communication and feedback can enhance mutual understanding and partnerships.
Implement Strategic Sourcing
Strategic sourcing involves understanding market trends and selecting the best suppliers based on quality, prices, and reliability.
A long-term view of sourcing enables better planning and resource allocation.
Utilize Technology
Purchasing departments should utilize technology to streamline parts management.
Inventory management software, for example, can track part usage and forecast demand effectively, reducing wastage and costs.
Continual Evaluation and Improvement
Lastly, continually evaluating lifecycle management processes ensures ongoing improvement.
Feedback and performance reviews help in identifying inefficiencies and implementing necessary changes.
This adaptive approach ensures organizations are always operating at optimal efficiency.
In conclusion, parts lifecycle management is a powerful tool that helps organizations reduce costs and improve efficiencies.
By managing the lifecycle phases carefully and implementing strategic actions, purchasing departments can secure lasting improvements and sustainable growth.
資料ダウンロード
QCD調達購買管理クラウド「newji」は、調達購買部門で必要なQCD管理全てを備えた、現場特化型兼クラウド型の今世紀最高の購買管理システムとなります。
ユーザー登録
調達購買業務の効率化だけでなく、システムを導入することで、コスト削減や製品・資材のステータス可視化のほか、属人化していた購買情報の共有化による内部不正防止や統制にも役立ちます。
NEWJI DX
製造業に特化したデジタルトランスフォーメーション(DX)の実現を目指す請負開発型のコンサルティングサービスです。AI、iPaaS、および先端の技術を駆使して、製造プロセスの効率化、業務効率化、チームワーク強化、コスト削減、品質向上を実現します。このサービスは、製造業の課題を深く理解し、それに対する最適なデジタルソリューションを提供することで、企業が持続的な成長とイノベーションを達成できるようサポートします。
オンライン講座
製造業、主に購買・調達部門にお勤めの方々に向けた情報を配信しております。
新任の方やベテランの方、管理職を対象とした幅広いコンテンツをご用意しております。
お問い合わせ
コストダウンが利益に直結する術だと理解していても、なかなか前に進めることができない状況。そんな時は、newjiのコストダウン自動化機能で大きく利益貢献しよう!
(Β版非公開)