- お役立ち記事
- “Exploring Japan’s Pioneering Role in PCB (Printed Circuit Board) Manufacturing”
“Exploring Japan’s Pioneering Role in PCB (Printed Circuit Board) Manufacturing”
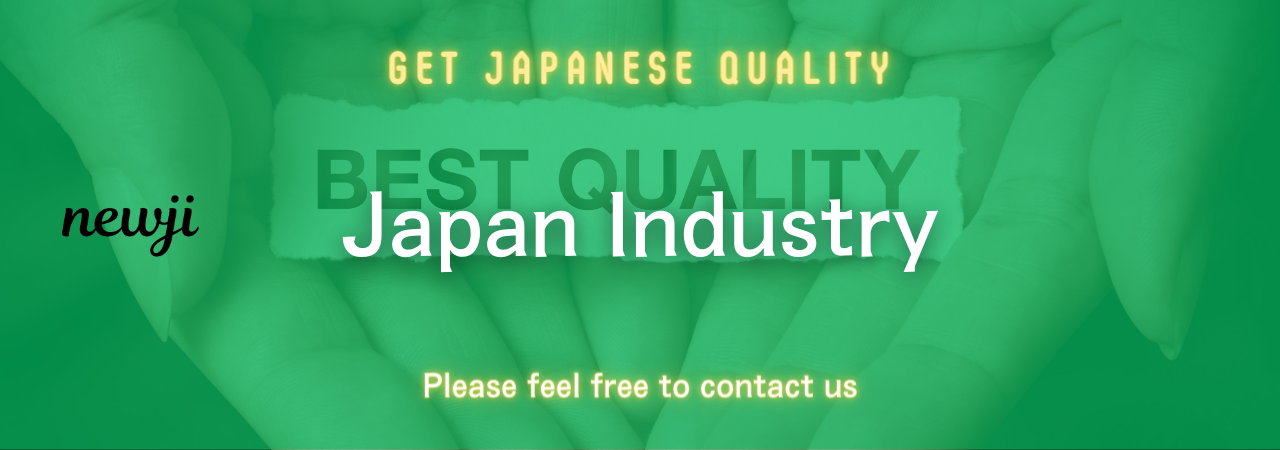
目次
Introduction to Japan’s PCB Manufacturing Landscape
Japan has long been recognized as a global leader in technology and manufacturing. Among its numerous contributions, Japan’s role in the Printed Circuit Board (PCB) manufacturing industry stands out prominently. PCBs are essential components in virtually all electronic devices, serving as the backbone for electrical connections and component integration. Japan’s expertise in PCB manufacturing is a testament to its commitment to quality, innovation, and precision engineering.
The Evolution of PCB Manufacturing in Japan
Historical Development
Japan’s journey in PCB manufacturing began in the mid-20th century, aligning with the country’s rapid industrialization and technological advancements. Initially focusing on basic PCB production, Japanese manufacturers quickly adapted to emerging technologies, emphasizing quality control and efficient production processes.
Technological Advancements
Over the decades, Japan has consistently invested in research and development, leading to significant technological breakthroughs in PCB manufacturing. Innovations such as high-density interconnect (HDI) PCBs, flexible and rigid-flex PCBs, and advanced surface mount technology (SMT) have been pioneered by Japanese firms. These advancements have not only enhanced the performance and reliability of electronic devices but also solidified Japan’s position as a leader in the global PCB market.
Advantages of Sourcing PCBs from Japan
Unparalleled Quality Control
Japanese PCB manufacturers are renowned for their stringent quality control measures. Implementing meticulous inspection protocols at every stage of production ensures that the final products meet the highest standards of reliability and performance. This commitment to quality minimizes defects and reduces the need for rework, offering significant benefits to international buyers.
Advanced Manufacturing Techniques
Japan’s PCB industry leverages cutting-edge manufacturing technologies, including automated assembly lines, precise etching processes, and sophisticated testing equipment. These advanced techniques enable the production of complex and high-density PCBs that cater to the demanding requirements of modern electronics, such as smartphones, automotive systems, and medical devices.
Efficient Supply Chain Management
Japanese suppliers excel in supply chain management, ensuring timely delivery and consistent supply of PCBs. Their well-organized logistics networks and strong relationships with component suppliers facilitate efficient procurement processes, reducing lead times and enhancing overall operational efficiency for international buyers.
Strong Emphasis on Sustainability
Sustainability is a core value in Japanese manufacturing. PCB manufacturers in Japan prioritize environmentally friendly practices, such as reducing waste, recycling materials, and minimizing energy consumption. These sustainable practices not only benefit the environment but also align with the growing demand for eco-friendly products in the global market.
Challenges and Considerations
Higher Production Costs
One of the primary challenges of sourcing PCBs from Japan is the higher production costs compared to other regions. Factors such as advanced technology, high labor standards, and stringent quality control contribute to increased manufacturing expenses. While the initial investment may be higher, the long-term benefits of superior quality and reliability often justify the costs for many businesses.
Language and Cultural Barriers
Conducting business with Japanese suppliers may involve navigating language and cultural differences. Effective communication is crucial for successful partnerships, and misunderstandings can arise without proper translation and cultural understanding. Building strong relationships and employing skilled translators or local representatives can mitigate these challenges.
Lead Time Considerations
Although Japanese suppliers are known for their efficient supply chain management, international logistics can introduce longer lead times. Shipping PCBs from Japan to other parts of the world may be affected by factors such as distance, customs regulations, and global shipping constraints. Planning and forecasting are essential to ensure timely procurement.
Supplier Negotiation Techniques
Building Strong Relationships
In Japanese business culture, building trust and long-term relationships is fundamental. Investing time in establishing rapport with suppliers can lead to more favorable terms, better communication, and enhanced collaboration. Demonstrating respect and understanding of Japanese business practices fosters mutual trust and cooperation.
Understanding Supplier Needs
Effective negotiation involves understanding the supplier’s needs and constraints. By recognizing the challenges and priorities of Japanese PCB manufacturers, buyers can propose solutions that benefit both parties. This collaborative approach can lead to win-win outcomes, such as volume discounts, flexible payment terms, or exclusive agreements.
Leveraging Volume and Long-Term Commitments
Japanese suppliers value stability and predictability. Committing to long-term contracts or higher volume orders can provide leverage in negotiations. Buyers who offer consistent and substantial business may secure better pricing, priority during peak periods, and access to the latest technological advancements.
Emphasizing Quality and Reliability
Highlighting the importance of quality and reliability in PCB procurement aligns with the strengths of Japanese manufacturers. By prioritizing these aspects in negotiations, buyers can negotiate terms that ensure high standards are maintained, such as stringent quality assurance protocols, detailed inspection reports, and warranties.
Market Conditions and Trends
Global Demand for Advanced PCBs
The global demand for advanced PCBs, such as HDI, flexible, and rigid-flex boards, continues to grow alongside the expansion of the electronics industry. Japan’s ability to deliver these sophisticated products positions it well to capitalize on emerging market opportunities in sectors like automotive electronics, telecommunications, and healthcare.
Impact of Global Supply Chain Disruptions
The COVID-19 pandemic and geopolitical tensions have highlighted vulnerabilities in global supply chains. Japan’s robust manufacturing infrastructure and resilient supply chain management practices have helped mitigate some of these disruptions. However, suppliers and buyers alike must remain adaptable and proactive in addressing potential challenges.
Emphasis on Miniaturization and Integration
The trend towards miniaturization and higher integration in electronic devices drives the demand for more compact and efficient PCBs. Japanese manufacturers are at the forefront of developing solutions that meet these requirements, including multi-layer boards and advanced materials that enhance performance while reducing size.
Best Practices for International Procurement and Purchasing
Conducting Thorough Supplier Assessments
Before engaging with Japanese PCB manufacturers, it is essential to conduct comprehensive supplier assessments. Evaluating factors such as production capabilities, quality certifications, financial stability, and past performance helps ensure that suppliers can meet the buyer’s requirements and maintain consistent standards.
Establishing Clear Specifications and Standards
Providing detailed specifications and standards is crucial for successful PCB procurement. Clear communication of technical requirements, quality expectations, and delivery timelines ensures that suppliers understand and can fulfill the buyer’s needs accurately.
Implementing Robust Quality Assurance Processes
Collaborating with suppliers to implement robust quality assurance processes enhances the reliability of PCBs. This may include joint inspections, regular audits, and the use of quality management systems (QMS) such as ISO 9001. Continuous monitoring and feedback loops help maintain high-quality standards and address issues promptly.
Optimizing Inventory and Lead Times
Effective inventory management and lead time optimization are critical for maintaining smooth production workflows. Collaborating with Japanese suppliers to forecast demand, establish safety stock levels, and streamline logistics can minimize delays and ensure a steady supply of PCBs.
Case Studies: Successful Partnerships with Japanese PCB Manufacturers
Automotive Electronics Manufacturer
A global automotive electronics company partnered with a leading Japanese PCB manufacturer to enhance the quality and reliability of its advanced driver-assistance systems (ADAS). Through collaborative development, the suppliers implemented HDI PCB technologies that reduced weight and improved performance. This partnership resulted in higher product reliability and a competitive edge in the automotive market.
Consumer Electronics Startup
A consumer electronics startup sought high-quality PCBs for its innovative wearable devices. By engaging with a Japanese PCB supplier, the startup benefited from the supplier’s expertise in flexible and rigid-flex PCBs. The close collaboration allowed for rapid prototyping and iterative design improvements, leading to a successful product launch and strong market reception.
Future Outlook for Japan’s PCB Industry
Integration of Smart Technologies
The integration of smart technologies, such as the Internet of Things (IoT) and artificial intelligence (AI), is set to drive further advancements in PCB manufacturing. Japanese manufacturers are investing in smart manufacturing processes, including automation, data analytics, and machine learning, to enhance production efficiency and product innovation.
Expansion into Emerging Markets
Japan’s PCB industry is poised to expand into emerging markets in Asia, Africa, and Latin America. By leveraging its technological prowess and reputation for quality, Japanese suppliers can tap into new customer bases and diversify their market presence, ensuring sustained growth in the global landscape.
Emphasis on Sustainable Manufacturing
Sustainability will continue to be a key focus for Japan’s PCB manufacturers. Investing in green technologies, adopting circular economy principles, and enhancing energy efficiency will not only reduce environmental impact but also meet the evolving demands of environmentally conscious consumers and regulatory bodies.
Conclusion
Japan’s pioneering role in PCB manufacturing is a reflection of its dedication to quality, innovation, and efficiency. For international procurement and purchasing professionals, sourcing PCBs from Japan offers numerous advantages, including superior quality, advanced technology, and reliable supply chains. While challenges such as higher costs and cultural differences exist, adopting best practices in supplier negotiation and relationship management can lead to successful and enduring partnerships. As the global electronics industry continues to evolve, Japan’s PCB manufacturers are well-positioned to meet the demands of the future, driving technological advancements and setting benchmarks for excellence in the field.
資料ダウンロード
QCD調達購買管理クラウド「newji」は、調達購買部門で必要なQCD管理全てを備えた、現場特化型兼クラウド型の今世紀最高の購買管理システムとなります。
ユーザー登録
調達購買業務の効率化だけでなく、システムを導入することで、コスト削減や製品・資材のステータス可視化のほか、属人化していた購買情報の共有化による内部不正防止や統制にも役立ちます。
NEWJI DX
製造業に特化したデジタルトランスフォーメーション(DX)の実現を目指す請負開発型のコンサルティングサービスです。AI、iPaaS、および先端の技術を駆使して、製造プロセスの効率化、業務効率化、チームワーク強化、コスト削減、品質向上を実現します。このサービスは、製造業の課題を深く理解し、それに対する最適なデジタルソリューションを提供することで、企業が持続的な成長とイノベーションを達成できるようサポートします。
オンライン講座
製造業、主に購買・調達部門にお勤めの方々に向けた情報を配信しております。
新任の方やベテランの方、管理職を対象とした幅広いコンテンツをご用意しております。
お問い合わせ
コストダウンが利益に直結する術だと理解していても、なかなか前に進めることができない状況。そんな時は、newjiのコストダウン自動化機能で大きく利益貢献しよう!
(Β版非公開)