- お役立ち記事
- A must-see for project leaders in the load cell manufacturing industry for automatic weighing machines! Design method for achieving both accuracy and stability
A must-see for project leaders in the load cell manufacturing industry for automatic weighing machines! Design method for achieving both accuracy and stability
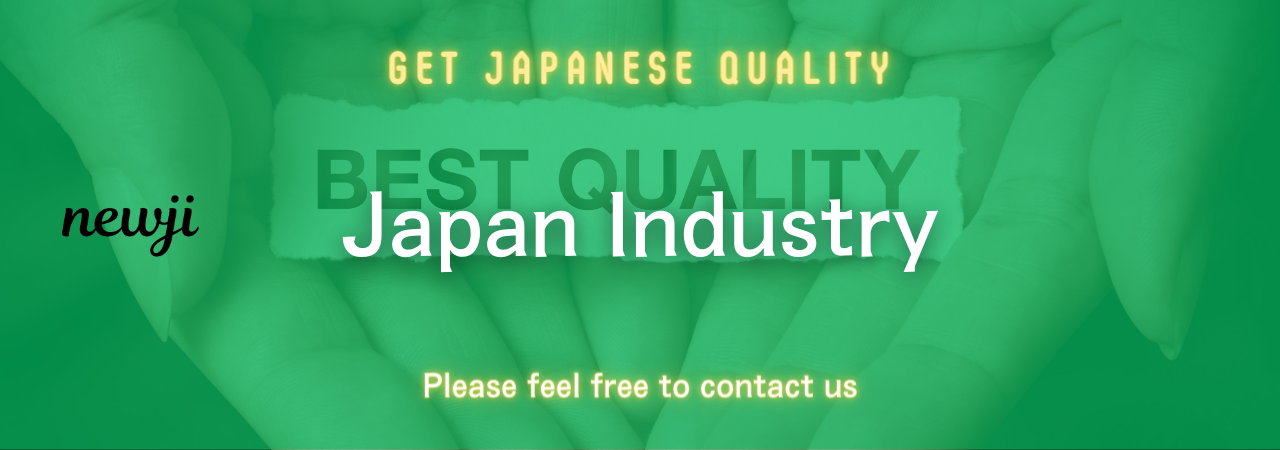
目次
Introduction to Load Cell Manufacturing for Automatic Weighing Machines
The load cell manufacturing industry is pivotal to the development of automatic weighing machines, which play a significant role in various sectors such as food processing, pharmaceuticals, and logistics.
Ensuring accuracy and stability in these machines is essential for maintaining quality control and efficiency.
For project leaders in this industry, understanding and implementing effective design methods are key to achieving these objectives.
Understanding Load Cells: The Basics
Load cells are transducers that convert a force into an electrical signal.
This signal is then used by the automatic weighing machine to determine the weight of an item placed on its platform.
There are different types of load cells, including strain gauge load cells, hydraulic load cells, and pneumatic load cells.
Each type offers various advantages, making it suitable for different applications within the industry.
Strain Gauge Load Cells
Strain gauge load cells are the most common type used in modern weighing systems.
They consist of a metal body that is attached with strain gauges.
When a force is applied, the strain gauges distort, changing their electrical resistance.
This change is then measured and translated into a weight value by the weighing machine’s processor.
Hydraulic and Pneumatic Load Cells
Hydraulic load cells use fluid pressure to measure weight, while pneumatic load cells utilize air pressure.
Hydraulic cells are often used in situations where electrical power is limited or in environments with extreme conditions.
Pneumatic load cells, however, are used where hygiene is crucial and can be easily cleaned.
Designing for Accuracy in Load Cell Manufacturing
Accuracy in load cell manufacturing is crucial, and achieving it requires the adoption of precise design methods.
Material Selection
Choosing the right material for load cell construction directly affects performance and durability.
Materials must withstand applied forces without significant deformation.
Common materials include aluminum, steel, and stainless steel.
Stainless steel is often preferred for its superior resistance to corrosive environments.
Calibration and Compensation
Calibration ensures that load cells provide accurate readings.
This process typically involves the application of known weights and the adjustment of the device’s output to match.
Temperature compensation is also vital as environmental changes can influence measurements.
Advanced load cells integrate temperature compensation technologies to maintain accuracy under varying conditions.
Signal Processing
The integrity of the signal output by the load cell is crucial for accurate measurements.
Implementing effective signal processing techniques can help minimize noise and enhance the accuracy of readings.
Choosing the right Analog-to-Digital Converter (ADC) and filter designs plays a significant role in refining signal precision.
Ensuring Stability in Load Cell Manufacturing
Stability in weighing systems is just as important as accuracy.
Stability ensures that the weighing machines provide consistent readings over time.
Creep and Hysteresis
Creep refers to the gradual change in a load cell’s output under a constant load, while hysteresis is the difference in output when increasing and decreasing weights are applied.
To minimize these factors, materials with low creep and hysteresis should be used, and precise manufacturing processes should be implemented.
Environmental Protection
Load cells must operate reliably in the environments where they are deployed.
Protective measures, such as sealing against dust and moisture and using corrosion-resistant materials, are imperative.
This helps maintain stable operation and prolongs the device’s lifespan.
Load Cell Installation
Proper installation plays a critical role in achieving stability.
Ensuring that load cells are mounted correctly and are free from external forces such as vibrations or temperature fluctuations is essential.
Following manufacturer guidelines for installation can greatly enhance the stability of the weighing system.
Balancing Accuracy and Stability in Design
Achieving both accuracy and stability in load cell design can be challenging.
However, with meticulous attention to design and engineering principles, it is possible to achieve this balance.
Advanced Engineering Techniques
Employing advanced engineering techniques such as Finite Element Analysis (FEA) during the design phase can help optimize the structure of the load cell.
This analysis aids in identifying points of stress and potential deformation, allowing for adjustments before manufacturing.
Integration of Smart Technologies
Integrating smart technologies, such as Internet of Things (IoT) sensors and machine learning algorithms, can improve both accuracy and stability.
These technologies enable real-time monitoring and adaptive calibration, enhancing overall performance.
Continuous Testing and Quality Control
Ongoing testing and quality control processes are essential to ensure that load cells meet the required standards.
Regular testing under different conditions can reveal issues related to both accuracy and stability before the products reach the customer.
Conclusion: The Roadmap to Success
For project leaders in the load cell manufacturing industry, achieving accuracy and stability is not a one-time task.
It requires continuous efforts and innovations in design methods.
By focusing on material selection, calibration, signal processing, environmental protection, and the integration of advanced technologies, businesses can design load cells that meet the demands of their respective industries.
Staying ahead in technology, adapting to new challenges, and maintaining a robust quality control regime are key to sustaining success in this ever-evolving field.
資料ダウンロード
QCD調達購買管理クラウド「newji」は、調達購買部門で必要なQCD管理全てを備えた、現場特化型兼クラウド型の今世紀最高の購買管理システムとなります。
ユーザー登録
調達購買業務の効率化だけでなく、システムを導入することで、コスト削減や製品・資材のステータス可視化のほか、属人化していた購買情報の共有化による内部不正防止や統制にも役立ちます。
NEWJI DX
製造業に特化したデジタルトランスフォーメーション(DX)の実現を目指す請負開発型のコンサルティングサービスです。AI、iPaaS、および先端の技術を駆使して、製造プロセスの効率化、業務効率化、チームワーク強化、コスト削減、品質向上を実現します。このサービスは、製造業の課題を深く理解し、それに対する最適なデジタルソリューションを提供することで、企業が持続的な成長とイノベーションを達成できるようサポートします。
オンライン講座
製造業、主に購買・調達部門にお勤めの方々に向けた情報を配信しております。
新任の方やベテランの方、管理職を対象とした幅広いコンテンツをご用意しております。
お問い合わせ
コストダウンが利益に直結する術だと理解していても、なかなか前に進めることができない状況。そんな時は、newjiのコストダウン自動化機能で大きく利益貢献しよう!
(Β版非公開)