- お役立ち記事
- For design leaders in the plastic molding industry! Optimize mold design with cascade flow analysis
For design leaders in the plastic molding industry! Optimize mold design with cascade flow analysis
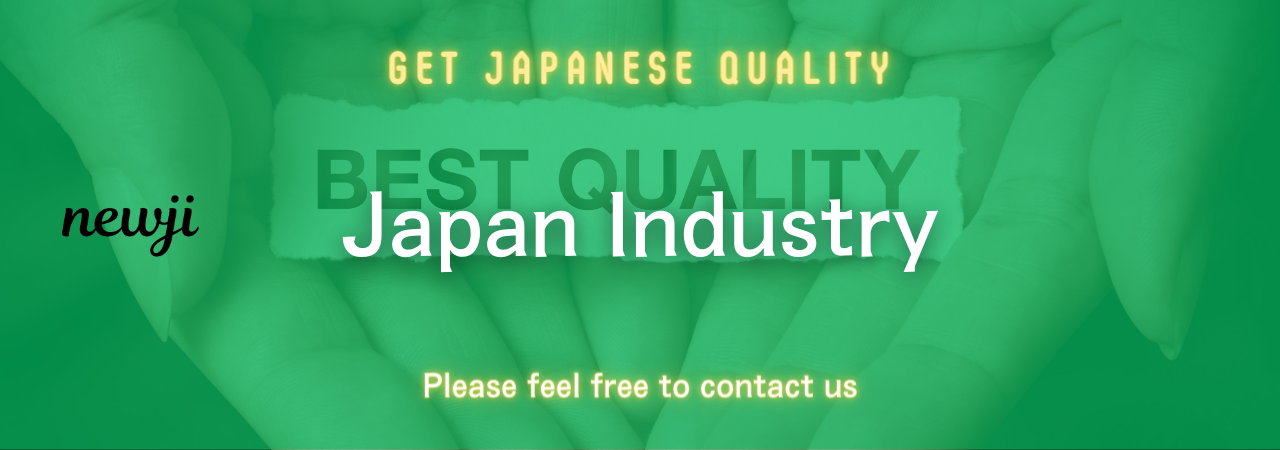
目次
Understanding Cascade Flow Analysis in Plastic Molding
Plastic molding is a crucial process in manufacturing, where transforming raw plastic materials into finished products relies heavily on precise mold design.
Design leaders in the plastic molding industry constantly seek methods to optimize these mold designs to improve efficiency and product quality.
One such method is cascade flow analysis, a sophisticated tool that can greatly enhance the design process of plastic molds.
By understanding and utilizing cascade flow analysis, design leaders can achieve an optimal balance between material usage, production speed, and product integrity.
What is Cascade Flow Analysis?
Cascade flow analysis is a computer simulation technique used in the plastic molding industry to predict how molten plastic will flow through a mold during the injection molding process.
This analysis provides insights into the dynamics of fluid motion, taking into account variables such as temperature, pressure, and velocity.
It allows design leaders to visualize how changes in mold geometry, material selection, and processing parameters can influence the flow patterns of the molten plastic.
This is essential for identifying and addressing potential issues like air traps, weld lines, and incomplete fills before the actual production process begins.
Benefits of Using Cascade Flow Analysis
One of the primary advantages of using cascade flow analysis is the ability to optimize mold designs for efficiency.
By simulating the flow of plastic, design leaders can adjust mold features to minimize waste, reduce cycle times, and enhance product quality.
This reduces the time and costs associated with trial-and-error testing on physical prototypes.
Moreover, cascade flow analysis helps in detecting common molding defects early in the design phase.
By anticipating problems like excessive warping, shrinkage, or sink marks, it’s possible to make design alterations that ensure the structural integrity and aesthetic quality of the final product.
Implementing Cascade Flow Analysis in Mold Design
For design leaders in the plastic molding industry, implementing cascade flow analysis involves several steps.
Firstly, accurate digital modeling of the mold is crucial.
Designers need to create a detailed CAD representation of the mold, incorporating all relevant parameters such as gate locations, venting systems, and cooling channels.
Next, the cascade flow analysis software is utilized to simulate the plastic injection process.
The software uses advanced compute algorithms to model how the molten plastic will behave inside the mold under various conditions.
Designers can then refine and iterate upon the mold model based on the predictions provided by the analysis.
Lastly, once an optimal design is achieved, physical prototyping can occur with far greater confidence in the outcome.
This holistic approach significantly streamlines the transition from design to production, ensuring that any potential flaws have already been addressed.
Choosing the Right Software for Cascade Flow Analysis
The effectiveness of cascade flow analysis largely depends on the software used to perform the simulations.
There are several leading tools available, each offering different features and capabilities.
When choosing a software package, design leaders should consider factors such as accuracy, user-friendliness, and compatibility with existing systems.
Features such as advanced meshing capabilities, multi-material support, and comprehensive libraries of material data can greatly enhance the accuracy of the analysis.
Additionally, integration with other design tools and collaboration features are important for larger teams working remotely or across different locations.
Training and Adopting Cascade Flow Analysis
For effective implementation, investing in training programs is essential.
Team members need to be well-versed in not only the functionality of the software but also the principles of fluid dynamics as they apply to mold design.
Workshops or online courses can provide valuable knowledge, allowing the team to take full advantage of cascade flow analysis in their design processes.
Moreover, fostering a culture of continuous learning and innovation helps to encourage team members to stay up-to-date on the latest advancements and techniques in the field.
This can lead to more creative and effective solutions for optimizing mold designs.
Future Trends in Cascade Flow Analysis
As technology advances, so too does the potential of cascade flow analysis.
Emerging trends in artificial intelligence and machine learning are expected to further enhance these simulations.
AI can improve the predictive accuracy of flow analysis, allowing for even more sophisticated optimization of mold designs.
Additionally, as sustainability becomes a priority, cascade flow analysis can play a pivotal role in developing molds that require less material and energy, contributing to a more eco-friendly production process.
The integration of IoT devices could also provide real-time data from production environments, allowing for dynamic adjustments in the design process.
Conclusion
Optimizing mold design in the plastic molding industry with cascade flow analysis offers numerous benefits for design leaders.
It provides valuable insights that lead to efficient, cost-effective, and high-quality production.
By embracing this powerful tool, professionals in the industry can stay ahead of the competition and meet the evolving demands for precision and sustainability.
Through careful implementation, appropriate software selection, and continuous training, cascading flow analysis positions the mold design process for present and future success.
資料ダウンロード
QCD調達購買管理クラウド「newji」は、調達購買部門で必要なQCD管理全てを備えた、現場特化型兼クラウド型の今世紀最高の購買管理システムとなります。
ユーザー登録
調達購買業務の効率化だけでなく、システムを導入することで、コスト削減や製品・資材のステータス可視化のほか、属人化していた購買情報の共有化による内部不正防止や統制にも役立ちます。
NEWJI DX
製造業に特化したデジタルトランスフォーメーション(DX)の実現を目指す請負開発型のコンサルティングサービスです。AI、iPaaS、および先端の技術を駆使して、製造プロセスの効率化、業務効率化、チームワーク強化、コスト削減、品質向上を実現します。このサービスは、製造業の課題を深く理解し、それに対する最適なデジタルソリューションを提供することで、企業が持続的な成長とイノベーションを達成できるようサポートします。
オンライン講座
製造業、主に購買・調達部門にお勤めの方々に向けた情報を配信しております。
新任の方やベテランの方、管理職を対象とした幅広いコンテンツをご用意しております。
お問い合わせ
コストダウンが利益に直結する術だと理解していても、なかなか前に進めることができない状況。そんな時は、newjiのコストダウン自動化機能で大きく利益貢献しよう!
(Β版非公開)