- お役立ち記事
- The balance between corrosion resistance and pressure resistance that new employees in the chemical process piping elbow manufacturing industry should keep in mind
The balance between corrosion resistance and pressure resistance that new employees in the chemical process piping elbow manufacturing industry should keep in mind
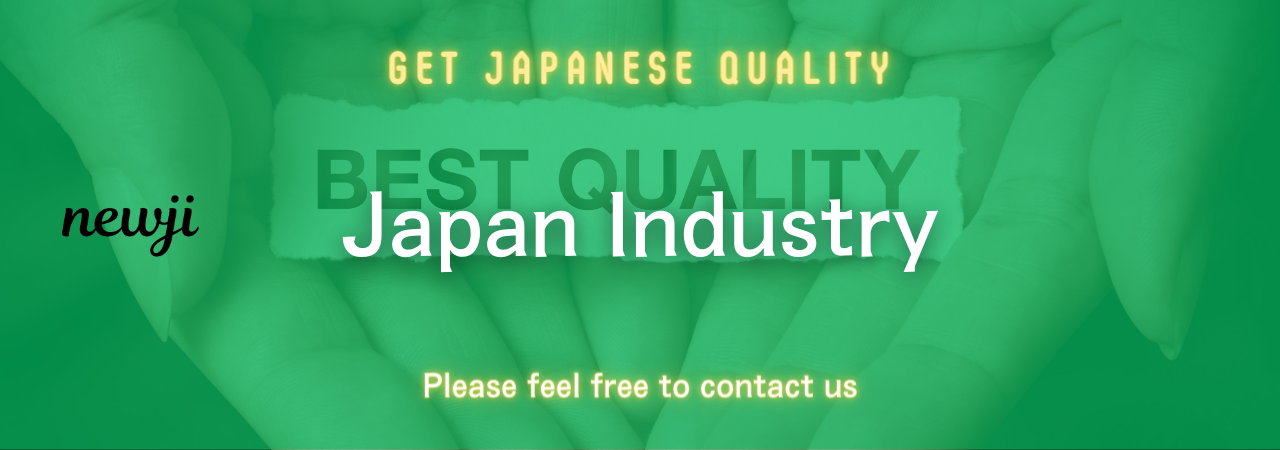
目次
Understanding the Basics of Corrosion Resistance
When stepping into the chemical process piping elbow manufacturing industry, it’s essential for new employees to grasp the concept of corrosion resistance.
Corrosion is a natural process where materials—often metals—deteriorate due to chemical reactions with their environment.
In piping systems, this can compromise structural integrity and lead to failure over time.
Corrosion resistance refers to the material’s ability to withstand these chemical reactions.
In the manufacturing of piping elbows used in chemical processes, choosing materials that resist these reactions is crucial for safety and durability.
Common materials like stainless steel, alloys, and certain polymers are often used due to their resistance to different corrosive environments.
The choice of material depends largely on the specific chemicals and environmental conditions they will encounter in a given piping system.
Pressure Resistance: A Key Consideration
Alongside corrosion, pressure is another critical factor that piping elbows must withstand.
Pressure resistance is the ability of the piping material and structure to withstand the internal and external pressures exerted by transported fluids or gases.
Proper pressure resistance ensures that pipes maintain their shape and function without failure or leakage under designated conditions.
Manufacturers must adhere to precise standards and specifications to ensure the structural integrity of pipes and elbows.
These standards are often promulgated by industry organizations and regulatory bodies to guarantee safe operations in chemical processes.
The Delicate Balance
Balancing corrosion resistance with pressure resistance involves trade-offs.
Materials highly resistant to corrosion might not always offer the best pressure resistance, and vice versa.
An informed selection process is crucial for achieving the optimal balance.
Firstly, consider the chemical composition and environmental conditions of the medium flowing through the piping.
Matrix engineering—choosing and blending the right materials—is an art that can enhance both resistance types by manipulating grain size, coating, and alloying.
This approach reduces risks, increases longevity, and optimally utilizes resources by not selecting an overly protective material unnecessary for the application.
Important Factors in Decision Making
To strike the right balance, several factors should be considered:
– **Chemical Compatibility**: Understanding the chemical characteristics of the fluids the pipe will carry is crucial.
Certain materials react adversely with specific chemicals, leading to accelerated corrosion.
– **Pressure Classifications**: Knowing the maximum operational pressure the piping system will face is vital.
This includes normal operating pressures and potential transient pressures or pressure spikes.
– **Temperature Conditions**: Both the ambient and operational temperatures affect the material properties.
Some materials lose their corrosion resistance or pressure capacity at extreme temperatures.
– **Lifecycle Costs**: Consideration should not only focus on initial material costs but also maintenance, replacements, and potential downtime due to failures.
Best Practices for New Employees
For those new to the industry, familiarize yourself with the standards and regulations that guide material selection and design practices.
These standards often include detailed tables and formulas to help determine the most appropriate materials for specific conditions.
Participate in training programs and mentorship schemes offered by your company.
These opportunities provide hands-on experience and expert insight that can be invaluable in practical situations.
Furthermore, stay abreast of advancements in material science.
Emerging technologies and new materials can offer improved corrosion and pressure resistance, potentially shifting industry practices.
Quality Control and Testing
Implementing stringent quality control measures is non-negotiable.
Regular inspections and testing help identify potential corrosion or pressure-related issues before they become critical.
Advances in nondestructive testing technology allow for safer, quicker assessments of piping integrity.
Understanding the available testing methods and their applications solidifies your capability to maintain high standards.
Conclusion: A Balanced Approach
For new employees in the chemical process piping elbow manufacturing industry, mastering the balance between corrosion resistance and pressure resistance is paramount.
Achieving this balance ensures that products remain safe, reliable, and efficient—the core objectives in the manufacturing process.
With the right materials, informed decisions, and continual learning, new professionals can contribute significantly to the industry’s progress.
Through commitment and an understanding of these fundamental principles, these professionals help secure the integrity of chemical transportation systems worldwide.
資料ダウンロード
QCD調達購買管理クラウド「newji」は、調達購買部門で必要なQCD管理全てを備えた、現場特化型兼クラウド型の今世紀最高の購買管理システムとなります。
ユーザー登録
調達購買業務の効率化だけでなく、システムを導入することで、コスト削減や製品・資材のステータス可視化のほか、属人化していた購買情報の共有化による内部不正防止や統制にも役立ちます。
NEWJI DX
製造業に特化したデジタルトランスフォーメーション(DX)の実現を目指す請負開発型のコンサルティングサービスです。AI、iPaaS、および先端の技術を駆使して、製造プロセスの効率化、業務効率化、チームワーク強化、コスト削減、品質向上を実現します。このサービスは、製造業の課題を深く理解し、それに対する最適なデジタルソリューションを提供することで、企業が持続的な成長とイノベーションを達成できるようサポートします。
オンライン講座
製造業、主に購買・調達部門にお勤めの方々に向けた情報を配信しております。
新任の方やベテランの方、管理職を対象とした幅広いコンテンツをご用意しております。
お問い合わせ
コストダウンが利益に直結する術だと理解していても、なかなか前に進めることができない状況。そんな時は、newjiのコストダウン自動化機能で大きく利益貢献しよう!
(Β版非公開)