- お役立ち記事
- How to set the optimal lot size for the manufacturing industry: Basics that purchasing departments should understand
How to set the optimal lot size for the manufacturing industry: Basics that purchasing departments should understand
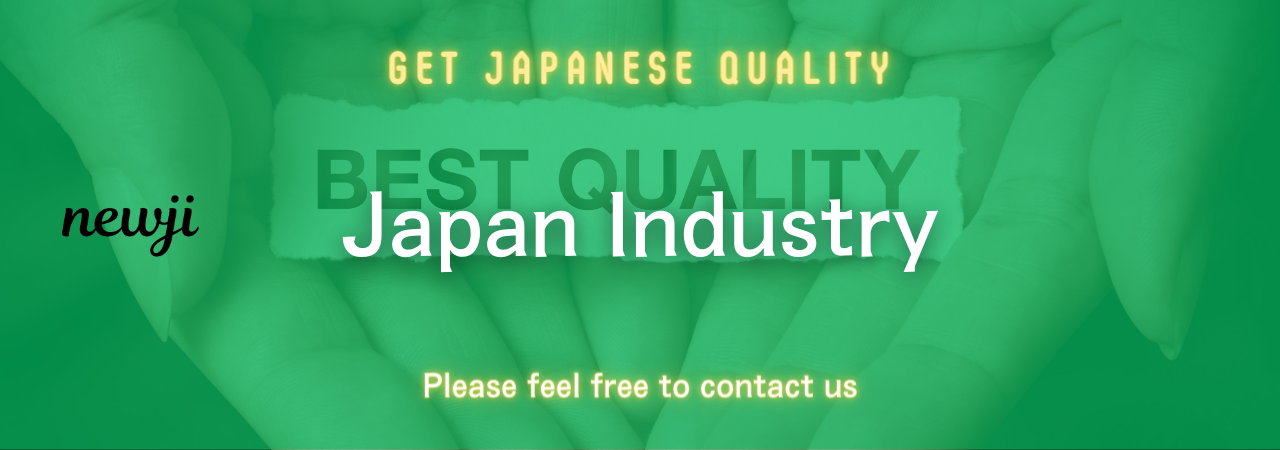
目次
Understanding Lot Size in Manufacturing
In the manufacturing industry, determining the optimal lot size is crucial for balancing production efficiency and inventory management.
Lot size refers to the number of units produced in one batch during a production run.
Deciding on the right lot size can significantly impact the cost of production, inventory levels, and even the overall profitability of a company.
For purchasing departments, understanding how to set the optimal lot size involves recognizing the trade-offs between production costs and inventory holding costs.
This knowledge helps ensure that manufacturers maintain a balance between meeting customer demand and minimizing the costs associated with overproduction or insufficient inventory.
Factors Influencing Lot Size
Several factors influence the decision-making process for setting the optimal lot size in manufacturing.
1. Production Costs
One of the most important factors to consider is the cost of production, which includes setup costs and per-unit production costs.
Setup costs are incurred each time the production equipment is prepared for a new batch.
These costs can include time spent adjusting machines, testing equipment, and preparing materials.
Per-unit production costs involve the direct costs associated with manufacturing each unit, such as materials, labor, and energy.
2. Inventory Holding Costs
Another factor is inventory holding costs, which include the expenses associated with storing unsold products.
These costs can comprise warehousing expenses, insurance, taxes, losses from obsolescence, and depreciation.
Higher inventory levels lead to higher holding costs, so the lot size must balance production efficiency with manageable inventory levels.
3. Demand Fluctuations
Demand for products can vary due to seasonal trends, market changes, or consumer preferences.
Accurate demand forecasting is critical for determining the optimal lot size.
Producing too much may lead to excess inventory, while producing too little may result in stockouts and potentially lost sales.
4. Production Lead Time
Lead time is the time taken from the start of production until the product is ready for delivery.
Long lead times can complicate inventory management and make it challenging to respond to sudden changes in demand.
An optimal lot size considers both the lead time and the frequency of production runs to ensure a steady supply of products for customers.
Calculating the Optimal Lot Size
The Economic Production Quantity (EPQ) model is a widely used formula for calculating the optimal lot size.
It extends the Economic Order Quantity (EOQ) model by considering the production capabilities and specifics of a manufacturing process.
EPQ Formula
The formula is:
\[ EPQ = \sqrt{\frac{2DS}{H} \cdot \frac{P}{(P – D)}} \]
Where:
– D = Demand rate (units per period)
– S = Setup cost per order
– H = Holding cost per unit per period
– P = Production rate (units per period)
The EPQ model helps determine the ideal production quantity that minimizes the total costs of production and inventory.
Advantages of Using EPQ
Using the EPQ model has several benefits:
– It reduces the overall costs associated with production and inventory.
– It efficiently utilizes production resources by optimizing the number of production runs.
– It improves inventory management by reducing the risks of stockouts and excess inventory.
Strategies for Purchasing Departments
Purchasing departments can adopt several strategies when setting lot sizes to optimize manufacturing operations.
1. Collaborate with Production Teams
Purchasing departments should work closely with production teams to understand the factors affecting production capabilities and constraints.
This collaboration ensures that lot sizes are feasible and align with production schedules.
2. Use Demand Forecasting Tools
Implementing demand forecasting tools and software can assist in predicting sales patterns and consumer behavior.
Accurate forecasts enable purchasing departments to make informed decisions about lot sizes, reducing the risks of overproduction or stockouts.
3. Implement Lean Manufacturing Techniques
Lean manufacturing techniques focus on minimizing waste, improving process efficiency, and enhancing product quality.
By applying lean principles, companies can optimize lot sizes to reduce costs and improve operational efficiency.
4. Regularly Review and Adjust Lot Sizes
The market environment and demand patterns are dynamic and can change frequently.
Regularly reviewing and adjusting lot sizes allows purchasing departments to remain agile and responsive to these changes.
Conclusion
Determining the optimal lot size in manufacturing is a complex process influenced by various factors such as production costs, inventory holding costs, and demand fluctuations.
By utilizing models like EPQ and implementing strategic approaches, purchasing departments can optimize manufacturing operations to improve overall efficiency and profitability.
Understanding the basics of lot sizing and staying informed about changes in the industry landscape are essential for purchasing professionals aiming to make data-driven decisions that enhance their company’s performance.
資料ダウンロード
QCD調達購買管理クラウド「newji」は、調達購買部門で必要なQCD管理全てを備えた、現場特化型兼クラウド型の今世紀最高の購買管理システムとなります。
ユーザー登録
調達購買業務の効率化だけでなく、システムを導入することで、コスト削減や製品・資材のステータス可視化のほか、属人化していた購買情報の共有化による内部不正防止や統制にも役立ちます。
NEWJI DX
製造業に特化したデジタルトランスフォーメーション(DX)の実現を目指す請負開発型のコンサルティングサービスです。AI、iPaaS、および先端の技術を駆使して、製造プロセスの効率化、業務効率化、チームワーク強化、コスト削減、品質向上を実現します。このサービスは、製造業の課題を深く理解し、それに対する最適なデジタルソリューションを提供することで、企業が持続的な成長とイノベーションを達成できるようサポートします。
オンライン講座
製造業、主に購買・調達部門にお勤めの方々に向けた情報を配信しております。
新任の方やベテランの方、管理職を対象とした幅広いコンテンツをご用意しております。
お問い合わせ
コストダウンが利益に直結する術だと理解していても、なかなか前に進めることができない状況。そんな時は、newjiのコストダウン自動化機能で大きく利益貢献しよう!
(Β版非公開)