- お役立ち記事
- For process engineers in the pharmaceutical manufacturing industry! Techniques for controlling particle size with high-pressure homogenizers
For process engineers in the pharmaceutical manufacturing industry! Techniques for controlling particle size with high-pressure homogenizers
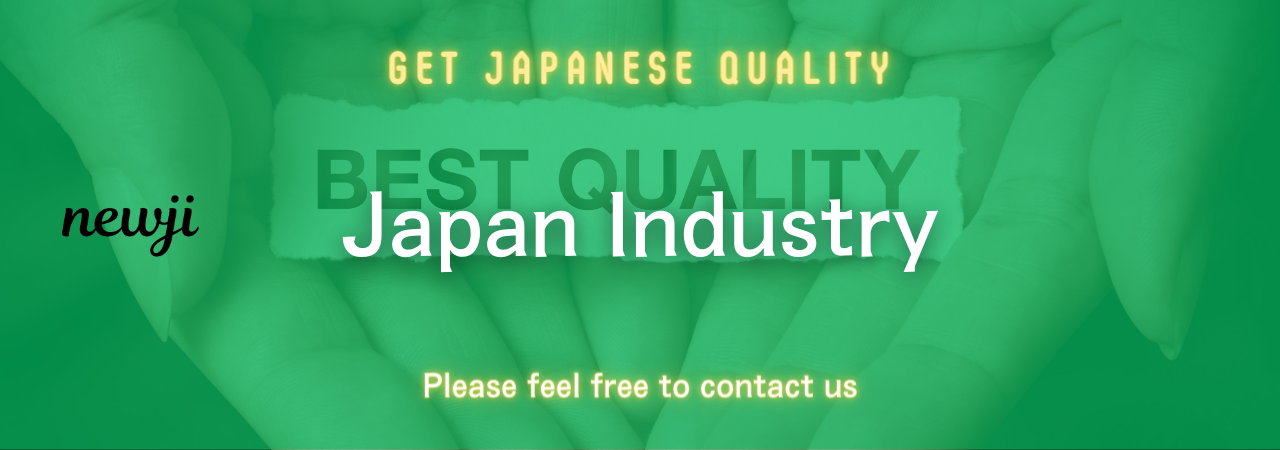
目次
Understanding High-Pressure Homogenization in Pharmaceutical Manufacturing
High-pressure homogenization is a pivotal technique in the pharmaceutical manufacturing industry, especially when it comes to controlling particle size.
This process involves forcing a product through a narrow space in the presence of high pressure, which results in the reduction of particle size.
For process engineers, mastering this technique is essential for creating products with desirable traits and ensuring consistency and quality in drug formulations.
Particle size impacts several critical factors, such as solubility, dissolution rate, and bioavailability of a drug.
Therefore, controlling particle size is crucial in the pharmaceutical manufacturing process.
It’s important to understand the benefits and methodologies behind using high-pressure homogenizers to harness and optimize the capabilities of this technology.
The Importance of Particle Size Control in Pharmaceuticals
Particle size plays a significant role in the effectiveness and quality of pharmaceutical products.
Smaller particles generally dissolve faster, leading to quicker release and absorption of the drug in the body.
This can greatly enhance the drug’s bioavailability and efficacy.
On the other hand, larger particles might be useful in controlled release formulations where a slower rate of dissolution is beneficial.
Consistency in particle size also affects the stability of the pharmaceutical compound, removing the potential for degradation and separation during storage.
Process engineers must ensure a uniform particle size to maintain the stability and shelf-life of products.
How High-Pressure Homogenizers Work
High-pressure homogenizers operate by pumping the fluid containing the particles through a narrow valve at high pressure.
This sudden drop in pressure creates turbulence and shear forces, which result in the reduction of particle size.
The key components of a high-pressure homogenizer include a high-pressure pump, a homogenizing valve, and a cooling system.
The pump applies the necessary force to move the product through the system, while the homogenizing valve is designed to provide controlled pressure to achieve the desired particle size reduction.
Finally, the cooling system ensures that the heat generated from the process does not degrade the product.
Advantages of Using High-Pressure Homogenizers
One of the significant advantages of high-pressure homogenizers is their ability to achieve a uniform particle size distribution.
This uniformity can significantly enhance the physical and chemical properties of the formulation, leading to predictable and consistent drug performance.
High-pressure homogenizers are also versatile, making them suitable for a broad range of applications, from emulsions and dispersions to suspensions.
This versatility makes them an ideal choice for developing various drug formulations in the pharmaceutical industry.
Furthermore, high-pressure homogenization is a clean and efficient process.
It does not require hazardous solvents, making it environmentally friendly and safe for the workforce.
Optimizing the High-Pressure Homogenization Process
For process engineers, optimizing the high-pressure homogenization process is crucial to achieving the desired outcome.
Several factors need to be considered, including pressure levels, the number of passes, and the characteristics of the material being homogenized.
Pressure Levels
Adjusting the pressure levels can greatly influence particle size reduction.
Higher pressures typically result in smaller particle sizes, leading to more effective formulations.
However, understanding the material’s properties is vital, as too much pressure can cause degradation or denaturation in some sensitive compounds.
Number of Passes
The number of times that the material passes through the homogenizer can determine the uniformity and consistency of particle size.
More passes can lead to finer particles but may also increase the processing time and cost.
Thus, process engineers must find a balance between the number of passes and the desired outcome to ensure efficiency without compromising quality.
Material Characteristics
Each material will behave differently under high-pressure conditions.
Understanding the physical and chemical characteristics of the material being processed is essential.
For instance, the viscosity, initial particle size, and temperature stability will influence the processing parameters.
Process engineers must tailor the homogenization process to the specific material for optimal results.
Challenges and Solutions
While high-pressure homogenization offers several advantages, it also comes with challenges.
Ensuring consistency and reproducibility can be difficult, given the complex interplay of variables that impact the process.
One potential solution is the use of advanced monitoring and control systems.
These technologies provide real-time data on various parameters, allowing for better control and adjustment during the process.
Implementing feedback control systems can help maintain the desired pressure and ensure uniformity in particle size.
Continuous research and development are also crucial.
Exploring new materials, formulations, and processing techniques can lead to innovative solutions that optimize the homogenization process further.
Staying updated with the latest technologies and methodologies will position process engineers at the forefront of pharmaceutical manufacturing.
In conclusion, mastering high-pressure homogenization techniques is essential for process engineers working in pharmaceutical manufacturing.
By understanding the intricacies of this process and optimizing it effectively, engineers can ensure the production of high-quality pharmaceutical products with controlled particle sizes, leading to better efficacy and performance in drug administration.
資料ダウンロード
QCD調達購買管理クラウド「newji」は、調達購買部門で必要なQCD管理全てを備えた、現場特化型兼クラウド型の今世紀最高の購買管理システムとなります。
ユーザー登録
調達購買業務の効率化だけでなく、システムを導入することで、コスト削減や製品・資材のステータス可視化のほか、属人化していた購買情報の共有化による内部不正防止や統制にも役立ちます。
NEWJI DX
製造業に特化したデジタルトランスフォーメーション(DX)の実現を目指す請負開発型のコンサルティングサービスです。AI、iPaaS、および先端の技術を駆使して、製造プロセスの効率化、業務効率化、チームワーク強化、コスト削減、品質向上を実現します。このサービスは、製造業の課題を深く理解し、それに対する最適なデジタルソリューションを提供することで、企業が持続的な成長とイノベーションを達成できるようサポートします。
オンライン講座
製造業、主に購買・調達部門にお勤めの方々に向けた情報を配信しております。
新任の方やベテランの方、管理職を対象とした幅広いコンテンツをご用意しております。
お問い合わせ
コストダウンが利益に直結する術だと理解していても、なかなか前に進めることができない状況。そんな時は、newjiのコストダウン自動化機能で大きく利益貢献しよう!
(Β版非公開)