- お役立ち記事
- Basics and practice of injection molding technology that new employees in the production technology department of the plastic molding industry should know
Basics and practice of injection molding technology that new employees in the production technology department of the plastic molding industry should know
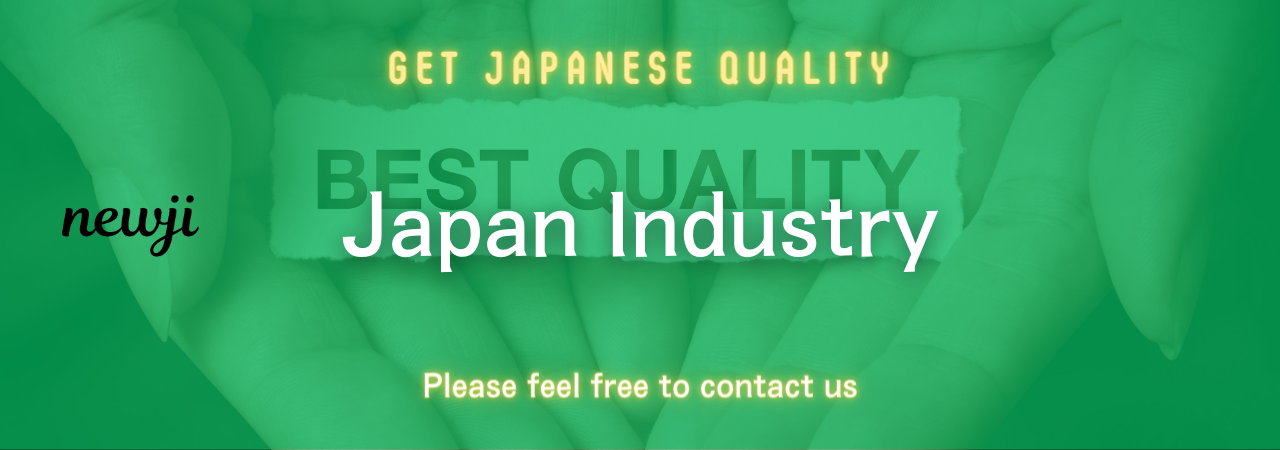
目次
Understanding Injection Molding Technology
Injection molding is a widely used manufacturing process in the plastic molding industry.
It involves injecting molten plastic into a mold to create a wide variety of plastic parts and products.
New employees in the production technology department should have a solid understanding of this process as it forms the backbone of plastic manufacturing.
The Basics of Injection Molding
Injection molding starts with small plastic pellets.
These pellets are fed into a heating barrel where they are melted to create a molten plastic material.
This molten plastic is then injected into a mold cavity, which determines the shape of the final product.
Once the injection is complete, the mold is cooled, solidifying the plastic.
The mold then opens, and the newly formed part is ejected.
Molding Machines and Components
To carry out injection molding, specialized machines called injection molding machines are used.
These machines have several key components:
1. **The Injection Unit**: This part involves the hopper, barrel, and screw.
It’s responsible for feeding, melting, and injecting the plastic into the mold.
2. **The Mold**: This is the hollow metal block where the molten plastic is shaped into its final form.
It consists of two primary components: the core and cavity.
3. **The Clamping Unit**: This holds the mold together during injection and keeps it closed under pressure.
Understanding the Molding Cycle
The injection molding cycle comprises several sequential steps:
– **Clamping**: The process starts by closing and locking the mold with the clamping unit.
– **Injection**: Molten plastic is injected into the mold cavity through the screw.
– **Cooling**: The mold is left to cool, allowing the plastic to solidify.
– **Ejection**: The mold opens, and the solidified part is ejected.
– **Repeat**: The cycle is repeated for the next part to be molded.
Advantages of Injection Molding
Injection molding is favored because of its many advantages:
– **Efficiency**: The process can produce a high volume of parts in a short time.
– **Customizable**: Molds can be designed to create highly detailed and complex shapes.
– **Economical**: Once the initial setup is done, the cost of mass-producing parts is low.
– **Uniformity**: It ensures consistent quality and precision across all parts produced.
Common Materials Used
Several types of plastic materials are used in injection molding:
– **Thermoplastics**: These are the most commonly used due to their flexibility and ease of use.
Examples include polyethylene, polystyrene, and polypropylene.
– **Thermosets**: These are used for parts requiring rigidity and durability.
Understanding the material properties is crucial for selecting the right plastic for specific applications.
Applications of Injection Molding
Injection molding finds applications in numerous industries:
– **Automotive**: Used for manufacturing dashboards, bumpers, and other components.
– **Consumer Goods**: Commonly used for producing household and electronic products.
– **Medical**: Essential for creating precise and hygienic healthcare products.
– **Packaging**: Wide use in creating durable, lightweight packaging solutions.
Challenges in Injection Molding
Like any manufacturing process, injection molding faces certain challenges:
– **Defects**: Issues such as warping, short shots, and sink marks can occur if parameters are not correctly controlled.
– **Material Selection**: Choosing the right material is key to ensuring product quality and performance.
– **Tooling Costs**: The initial cost of creating molds can be high.
Understanding these challenges can help new employees devise strategies to mitigate them.
Safety and Maintenance
Maintaining safety and proper machine maintenance are paramount in ensuring smooth operation:
1. **Safety Measures**: Workers should be properly trained and made aware of safety protocols to avoid accidents.
2. **Regular Maintenance**: Routine inspection and maintenance of machines help in minimizing downtime and prolong machine life.
The Future of Injection Molding
The future of injection molding is promising, with several advancements on the horizon:
– **Automation**: The use of robotic systems is increasing efficiency and reducing human error.
– **Sustainable Practices**: Focus on using biodegradable materials and reducing waste.
– **Advances in Materials**: Development of stronger and lighter materials for various applications.
Conclusion
For new employees in the production technology department, understanding the basics and practices of injection molding technology is essential.
A solid grasp of the process, components, materials, and applications will ensure efficient and high-quality production.
As you continue to learn and adapt to technological advancements, injection molding will remain a central component of the plastic manufacturing industry.
資料ダウンロード
QCD調達購買管理クラウド「newji」は、調達購買部門で必要なQCD管理全てを備えた、現場特化型兼クラウド型の今世紀最高の購買管理システムとなります。
ユーザー登録
調達購買業務の効率化だけでなく、システムを導入することで、コスト削減や製品・資材のステータス可視化のほか、属人化していた購買情報の共有化による内部不正防止や統制にも役立ちます。
NEWJI DX
製造業に特化したデジタルトランスフォーメーション(DX)の実現を目指す請負開発型のコンサルティングサービスです。AI、iPaaS、および先端の技術を駆使して、製造プロセスの効率化、業務効率化、チームワーク強化、コスト削減、品質向上を実現します。このサービスは、製造業の課題を深く理解し、それに対する最適なデジタルソリューションを提供することで、企業が持続的な成長とイノベーションを達成できるようサポートします。
オンライン講座
製造業、主に購買・調達部門にお勤めの方々に向けた情報を配信しております。
新任の方やベテランの方、管理職を対象とした幅広いコンテンツをご用意しております。
お問い合わせ
コストダウンが利益に直結する術だと理解していても、なかなか前に進めることができない状況。そんな時は、newjiのコストダウン自動化機能で大きく利益貢献しよう!
(Β版非公開)