- お役立ち記事
- For project leaders in the precision rack and pinion manufacturing industry! Designed to achieve both high torque and smoothness
For project leaders in the precision rack and pinion manufacturing industry! Designed to achieve both high torque and smoothness
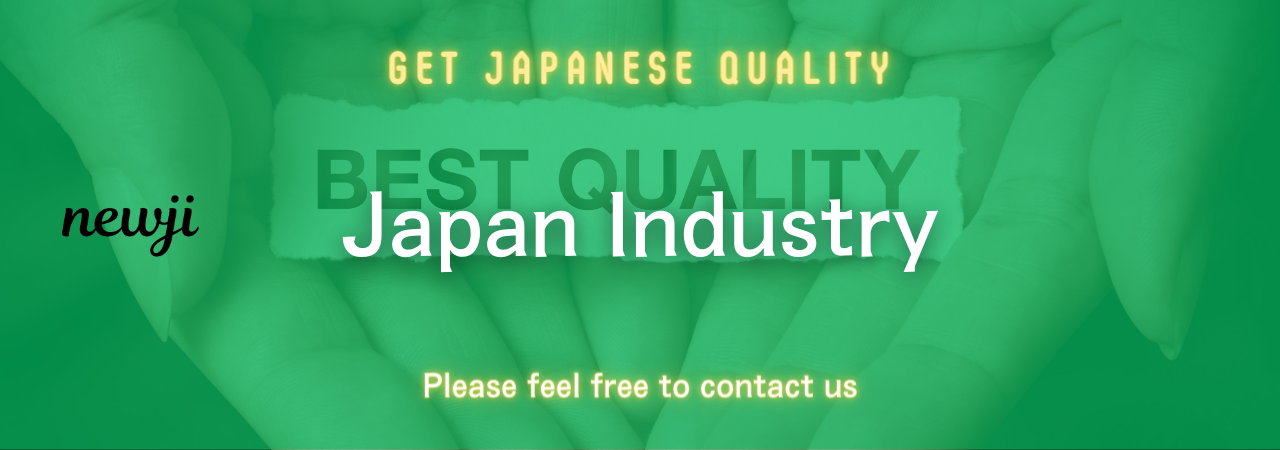
目次
Introduction to High Torque and Smoothness
In the precision rack and pinion manufacturing industry, balancing the need for high torque and operational smoothness is critical for success.
Achieving this balance isn’t just a technical necessity; it can also be a key differentiator in the competitive landscape of precision engineering.
Understanding how to design systems that offer both high torque and smoothness can lead to more efficient machinery and increased customer satisfaction.
This article will delve into effective strategies, challenges, and innovations in this field, providing valuable insights for project leaders looking to excel in rack and pinion manufacturing.
Understanding Rack and Pinion Mechanisms
To appreciate the complexities involved in achieving both high torque and smoothness in rack and pinion systems, it’s essential to understand the basic mechanics.
Rack and pinion systems convert rotational motion into linear motion, relying on the gear pair to ensure precise movement.
The pinion is a small gear that engages a linear gear, or rack, moving it linearly.
This setup is crucial in many applications, from automotive steering systems to industrial machinery.
The challenge arises when trying to enhance torque without compromising the smoothness of motion or introducing excessive wear and noise.
The Importance of Material Selection
Material selection plays a pivotal role in determining the performance characteristics of rack and pinion systems.
Choosing materials that can withstand high torque while maintaining optimal performance under stress is crucial.
High-strength alloys, advanced composites, and treated metals are frequently used for their durability and reduced friction properties.
By utilizing materials with the right balance of strength and weight, engineers can enhance torque capabilities without sacrificing the smooth operation essential for precise control.
Additionally, using materials with good wear resistance properties helps in prolonging the lifespan of the components, improving reliability and reducing maintenance costs.
Design Precision and Gear Geometry
Precision in design and manufacturing is vital for combining high torque with smooth motion.
Attention to gear geometry, including tooth profile and spacing, can dramatically impact performance.
Optimizing these parameters reduces friction and minimizes backlash, contributing to smoother operation.
Advanced computer-aided design (CAD) software allows engineers to model various configurations and simulate performance under different load conditions.
This technology enables the prediction of potential issues and optimizes design before manufacturing, saving time and resources.
Investing in precision machining technologies ensures that the actual production matches the meticulous design, further enhancing system performance.
Advanced Lubrication Techniques
Lubrication is another critical factor in achieving both high torque and smooth motion in rack and pinion systems.
Advanced lubrication techniques can reduce friction and heat build-up, preventing wear and ensuring smooth operation even under heavy loads.
Synthetic lubricants, designed for high temperature and extreme pressure conditions, are often preferred for these systems.
These lubricants provide consistent protection and performance over extended periods, reducing the need for frequent maintenance.
Additionally, some systems may benefit from integrating automated lubrication systems that ensure optimal lubricant application, further enhancing performance and longevity.
Incorporating Automation and Control Technologies
Automation and control technologies are transforming how rack and pinion systems operate.
Integrating sensors and feedback systems can optimize performance by automatically adjusting parameters to maintain smooth operation under varying conditions.
For instance, torque monitoring systems can provide real-time data to control units, which can adjust lubrication flow or thermal management systems to ensure peak performance.
This level of control helps in maintaining operational smoothness, even under peak loads, and reduces wear on components.
For project leaders, incorporating such technologies can lead to improvements in efficiency and reliability, setting their products apart in the marketplace.
The Challenges of High Torque and Smoothness
While achieving high torque and smooth motion are desirable goals, they come with their own set of challenges.
Project leaders must consider potential trade-offs, such as increased complexity and higher costs.
The need for precise manufacturing and high-quality materials can drive up production expenses.
Addressing these challenges requires a clear strategy that balances performance with cost-effectiveness.
Cost Management and Efficiency
Managing costs while striving for high-performance standards is a critical challenge.
Adopting lean manufacturing principles can help reduce waste and improve efficiency.
Collaborating closely with suppliers to negotiate better pricing or bulk purchase agreements can also lower material costs.
Furthermore, investing in employee training ensures that the workforce is skilled in using advanced manufacturing technologies, which can improve yield and reduce defects.
By sustaining a focus on cost management, project leaders can deliver high-quality products without exceeding budget constraints.
Continuous Innovation and R&D
In the rapidly evolving field of precision engineering, continuous innovation and research and development (R&D) are essential.
Project leaders should encourage a culture of innovation, where teams are motivated to experiment and explore new ideas.
Keeping abreast of industry trends and technological advancements can provide insights into potential improvements and innovations.
Partnering with research institutions or investing in in-house R&D can lead to breakthroughs that enhance both torque and smoothness.
Embracing innovation not only addresses existing challenges but also positions companies at the forefront of industry advancements.
Conclusion
Achieving both high torque and smoothness in precision rack and pinion systems is a complex but achievable goal for project leaders in this industry.
By focusing on material selection, precise design, advanced lubrication, and automation technologies, organizations can overcome challenges and deliver superior products.
Understanding the interplay of these factors and managing costs effectively are key to maintaining a competitive edge.
Continuous innovation will pave the way for further advancements, ensuring that companies remain leaders in precision engineering solutions.
By addressing these elements, project leaders can confidently steer their projects towards success in the competitive precision manufacturing sector.
資料ダウンロード
QCD調達購買管理クラウド「newji」は、調達購買部門で必要なQCD管理全てを備えた、現場特化型兼クラウド型の今世紀最高の購買管理システムとなります。
ユーザー登録
調達購買業務の効率化だけでなく、システムを導入することで、コスト削減や製品・資材のステータス可視化のほか、属人化していた購買情報の共有化による内部不正防止や統制にも役立ちます。
NEWJI DX
製造業に特化したデジタルトランスフォーメーション(DX)の実現を目指す請負開発型のコンサルティングサービスです。AI、iPaaS、および先端の技術を駆使して、製造プロセスの効率化、業務効率化、チームワーク強化、コスト削減、品質向上を実現します。このサービスは、製造業の課題を深く理解し、それに対する最適なデジタルソリューションを提供することで、企業が持続的な成長とイノベーションを達成できるようサポートします。
オンライン講座
製造業、主に購買・調達部門にお勤めの方々に向けた情報を配信しております。
新任の方やベテランの方、管理職を対象とした幅広いコンテンツをご用意しております。
お問い合わせ
コストダウンが利益に直結する術だと理解していても、なかなか前に進めることができない状況。そんな時は、newjiのコストダウン自動化機能で大きく利益貢献しよう!
(Β版非公開)