- お役立ち記事
- Multi-layer board manufacturing and quality assurance that leaders of production technology departments in the electronic component manufacturing industry should know.
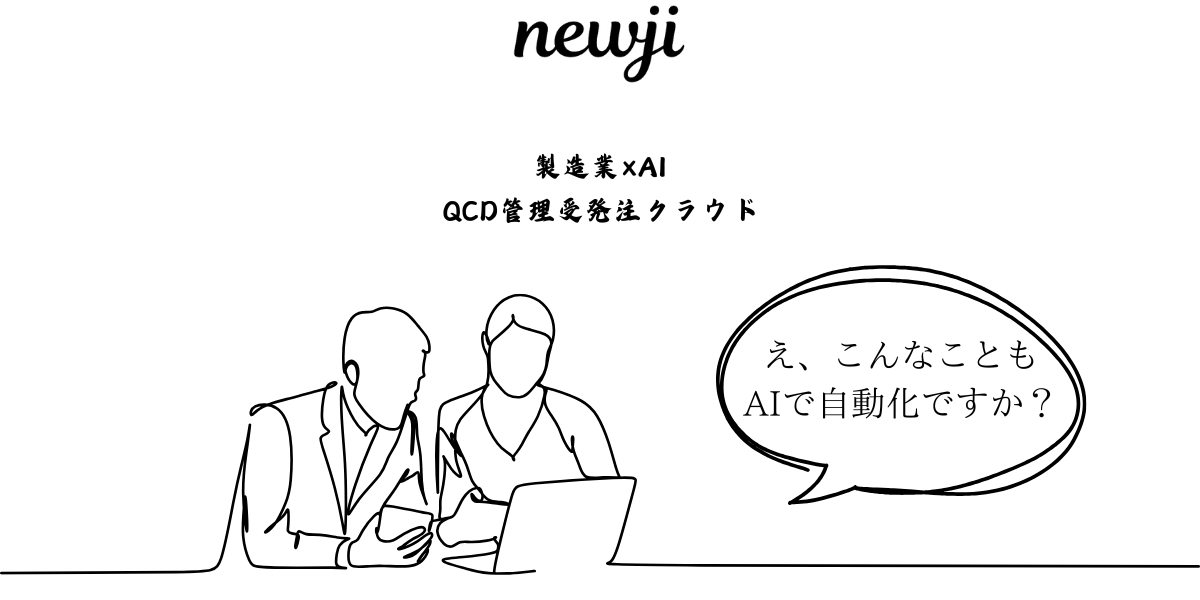
Multi-layer board manufacturing and quality assurance that leaders of production technology departments in the electronic component manufacturing industry should know.
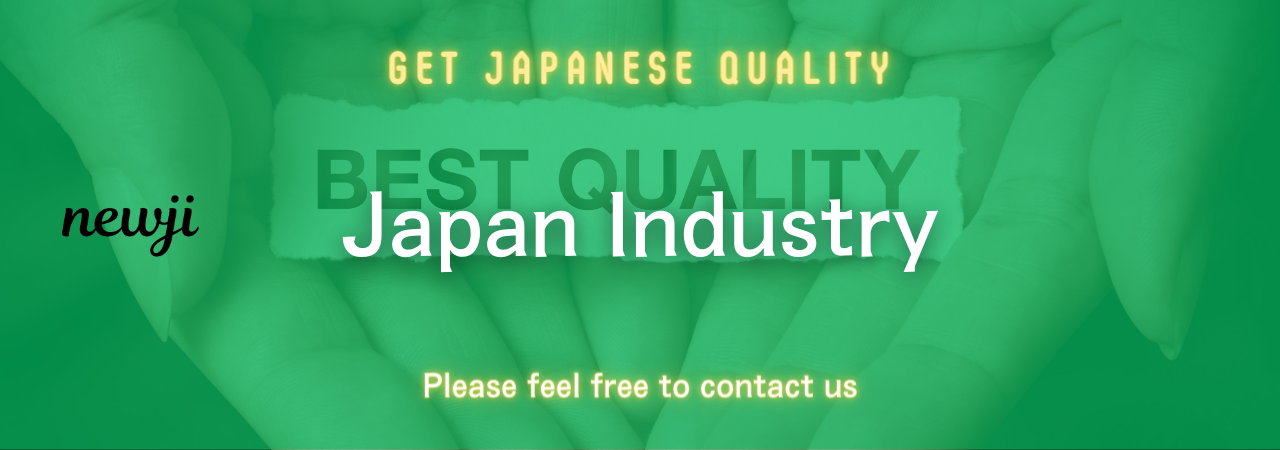
目次
Understanding Multi-layer Boards
Multi-layer boards form the backbone of modern electronic devices, providing compact and efficient circuitry.
In essence, these boards are composed of multiple layers of electronic components etched onto insulating substrates.
The layers are stacked and bonded together to function as a single assembly.
This design allows for greater circuit complexity and higher performance without increasing the physical size of the board significantly.
Understanding the intricacies of multi-layer board manufacturing is crucial for leaders in the production technology departments of electronic manufacturing industries.
The Importance of Multi-layer Boards
The electronic industry relies heavily on multi-layer boards due to their ability to accommodate complex circuits while saving space.
These boards are essential for the production of advanced gadgets, ranging from smartphones and laptops to medical devices and aerospace technology.
The inherent complexity offers numerous advantages, including increased circuit density, improved signal integrity, and reduced electromagnetic interference.
As a leader in the field, it’s imperative to grasp the significance of these components in your production process.
Manufacturing Multi-layer Boards
The production of multi-layer boards involves several intricate steps, each crucial to ensuring a high-quality product.
Design and Material Selection
The manufacturing process begins with design, where engineers create detailed schematics of the circuit layout.
Selecting the right materials is paramount.
This includes choosing substrates like FR-4, polyimide, or other high-performance materials known for durability and thermal stability.
The choice of material impacts the board’s electromagnetic compatibility and heat dissipation capabilities, directly influencing the final product performance.
Layer Stacking and Bonding
Once the design phase is complete, individual layers are fabricated.
Conductive patterns are etched onto copper-clad laminates, followed by a lamination process to stack these layers.
This multi-layer configuration is then bonded under high pressure and temperature to form a unified board.
Quality during this step ensures precision alignment and robust structural integrity essential for future functionality.
Drilling and Through-Hole Plating
After stacking, drilling techniques are employed to create vias and through-holes for interlayer connectivity.
These tiny holes are essential to ensure electrical signals can traverse the various layers seamlessly.
Following drilling, through-hole plating is executed to deposit a conductive layer within these holes, typically using electroplating, to facilitate current flow across the board.
Testing and Quality Control
Testing is a critical phase in the multi-layer board manufacturing process.
Each board must undergo rigorous testing procedures to ensure functionality and reliability.
These tests often include electrical testing, thermal stress tests, and visual inspections to identify any defects or inconsistencies.
Implementing stringent quality control measures is imperative to maintain product standards and prevent failures in end applications.
Quality Assurance in Multi-layer Boards
Ensuring quality in multi-layer board manufacturing is non-negotiable, affecting both the immediate performance and long-term reliability of electronic devices.
Implementing Quality Standards
Adhering to recognized quality standards, such as ISO 9001, is essential in establishing a framework for consistent production quality.
These standards help in defining procedures, setting benchmarks, and measuring performance throughout the manufacturing process.
Following such guidelines not only helps in maintaining product quality but also instills trust in consumers.
Continuous Process Improvement
Continuous improvement practices such as Lean Manufacturing and Six Sigma can lead to significant advancements in production processes.
These methodologies aim to reduce waste, improve efficiency, and eliminate defects in manufacturing.
By adopting such practices, leaders can expect enhanced productivity and a reduction in production costs while achieving superior product quality.
Advanced Testing Techniques
Employing advanced testing techniques can greatly enhance quality assurance within the production line.
Techniques such as automated optical inspection (AOI), x-ray inspection, and in-circuit testing (ICT) provide comprehensive analysis capabilities.
These methods allow for early detection of defects, making it easier to address issues before they escalate to larger production lots.
The Role of Leaders in Ensuring Quality
Leaders of production technology departments play a pivotal role in ensuring the quality of multi-layer boards.
Strategic Decision Making
Making informed decisions about material selection, process improvements, and technology investments is critical.
Leaders must balance cost considerations with quality objectives to achieve favorable outcomes.
This requires a deep understanding of the production processes and the market demands to make strategic choices that align with business goals.
Fostering a Quality Culture
A strong organizational culture emphasizing quality is vital for long-term success.
Training employees on the importance of quality processes and encouraging a mindset oriented towards continuous improvement can make a substantial difference.
Promoting such a culture ensures that every team member understands the importance of their role in achieving exceptional product quality.
Embracing Innovation
To stay competitive, leaders must embrace innovation and be open to adopting new technologies.
Investing in state-of-the-art equipment and exploring emerging technologies can provide a competitive edge.
Emphasizing innovation not only improves manufacturing capabilities but also positions the company as a leader in the electronic component manufacturing industry.
Conclusion
The manufacturing and quality assurance of multi-layer boards is a complex yet rewarding process essential for the production of cutting-edge electronic devices.
For leaders in the electronic component manufacturing industry, understanding these processes and their impact on product quality is vital.
By ensuring rigorous quality control, fostering a culture of continuous improvement, and embracing innovation, leaders can navigate the complexities of multi-layer board manufacturing effectively.
This will result in high-quality products that meet the highest industry standards and consumer expectations.
資料ダウンロード
QCD調達購買管理クラウド「newji」は、調達購買部門で必要なQCD管理全てを備えた、現場特化型兼クラウド型の今世紀最高の購買管理システムとなります。
ユーザー登録
調達購買業務の効率化だけでなく、システムを導入することで、コスト削減や製品・資材のステータス可視化のほか、属人化していた購買情報の共有化による内部不正防止や統制にも役立ちます。
NEWJI DX
製造業に特化したデジタルトランスフォーメーション(DX)の実現を目指す請負開発型のコンサルティングサービスです。AI、iPaaS、および先端の技術を駆使して、製造プロセスの効率化、業務効率化、チームワーク強化、コスト削減、品質向上を実現します。このサービスは、製造業の課題を深く理解し、それに対する最適なデジタルソリューションを提供することで、企業が持続的な成長とイノベーションを達成できるようサポートします。
オンライン講座
製造業、主に購買・調達部門にお勤めの方々に向けた情報を配信しております。
新任の方やベテランの方、管理職を対象とした幅広いコンテンツをご用意しております。
お問い合わせ
コストダウンが利益に直結する術だと理解していても、なかなか前に進めることができない状況。そんな時は、newjiのコストダウン自動化機能で大きく利益貢献しよう!
(Β版非公開)