- お役立ち記事
- A must-see for managers of production technology departments in the auto parts manufacturing industry! Flexible production line design and implementation guidelines
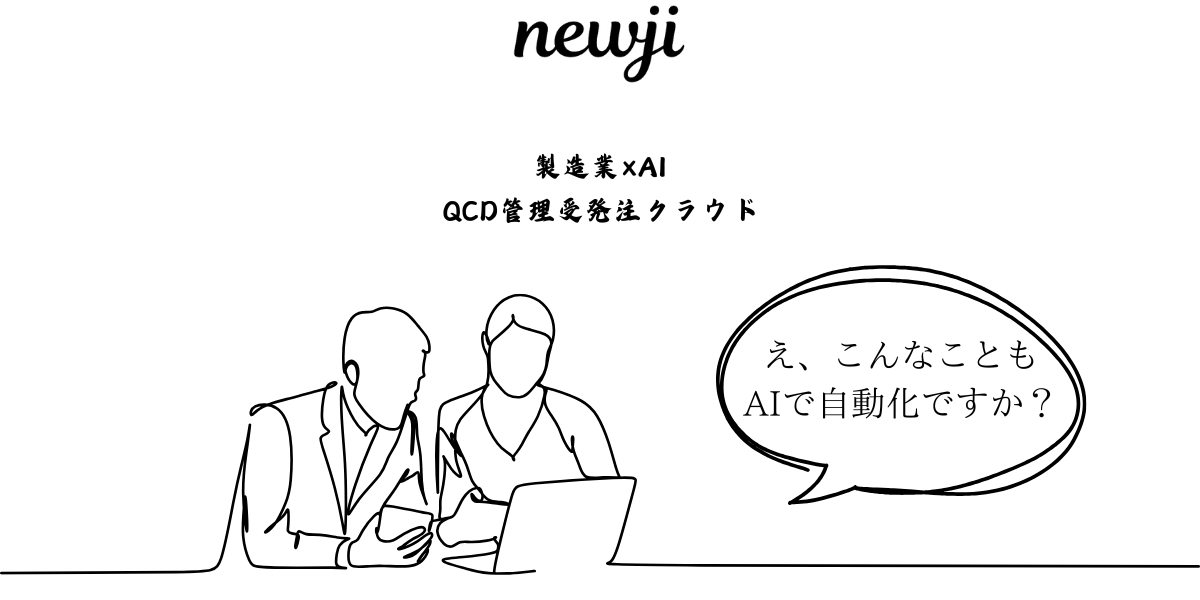
A must-see for managers of production technology departments in the auto parts manufacturing industry! Flexible production line design and implementation guidelines
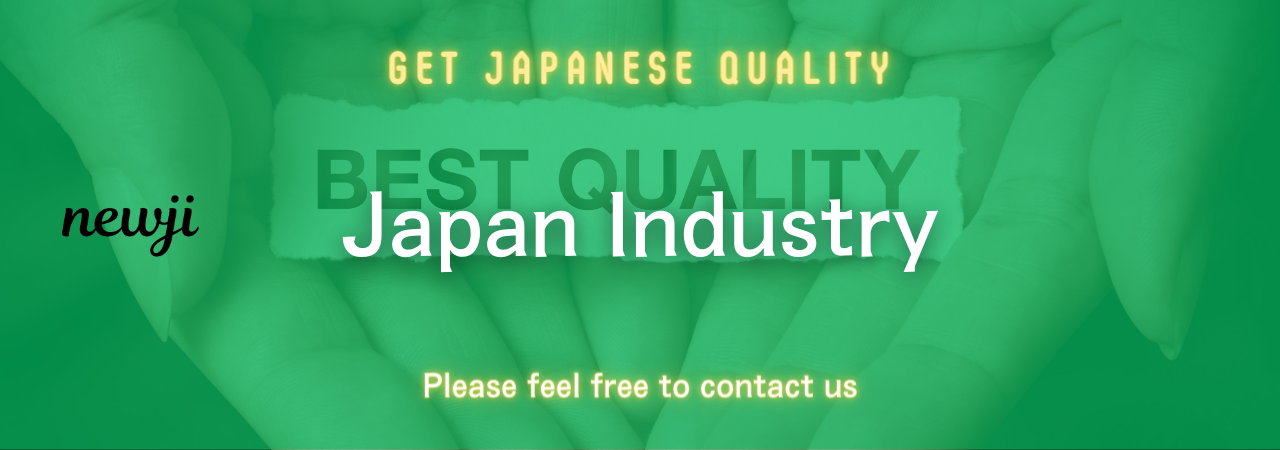
目次
Introduction to Flexible Production Lines
In the fast-evolving auto parts manufacturing industry, staying competitive means constantly improving production processes.
One of the key advancements in this field is the adoption of flexible production lines.
These systems offer massive benefits, including increased efficiency, reduced downtime, and the ability to swiftly adapt to market changes.
Flexible production lines allow for the seamless production of different auto parts without the need for extensive reconfiguration.
This adaptability is crucial in meeting varying product demands and accommodating new technology without significant interruptions.
Understanding Flexible Manufacturing Systems
A flexible manufacturing system (FMS) is a critical component of a flexible production line.
These systems consist of adaptable machinery, automated handling equipment, and integrated computer control systems.
The primary advantage of an FMS is its ability to produce a range of auto parts in varying quantities.
The flexibility stems from several factors, including advanced robotics, smart sensors, and automated control systems.
Robotics allow machines to perform diverse tasks, adapting to different parts production requirements swiftly.
Smart sensors offer real-time data and feedback, enabling manufacturers to swiftly identify and rectify issues.
With automated control systems, the coordination and synchronization of tasks become seamless, reducing human error and increasing efficiency.
Benefits of Implementing Flexible Production Lines
The implementation of flexible production lines can provide several advantages to manufacturers in the auto parts sector.
One of the primary benefits is the reduction in lead time.
With a flexible system, manufacturers can streamline their production processes, reducing the time taken from order to delivery.
Cost reduction is another significant benefit.
Flexible lines reduce the need for extensive reconfiguration, thereby lowering downtime and associated costs.
Moreover, they minimize waste by optimizing resource use.
Quality improvement is yet another advantage.
With advanced machinery and control systems, manufacturers can maintain a consistent standard, reducing defects and enhancing product reliability.
Overall, flexible production lines lead to higher customer satisfaction and increased market competitiveness.
Key Considerations for Design and Implementation
Designing and implementing a flexible production line requires careful planning and consideration of several factors.
Firstly, it is essential to assess the current manufacturing capabilities and identify areas where flexibility is most needed.
Understanding the specific requirements of the production process ensures that the new system aligns well with existing operations.
The choice of technology is crucial.
Invest in state-of-the-art machinery and software systems that can support the desired flexibility.
Robotic systems and smart sensors should be chosen based on their adaptability and ease of integration with existing processes.
Scalability is another critical consideration.
The production line must be able to grow with the company.
Flexible systems should be designed to accommodate future expansion without requiring a complete overhaul.
Employee training must not be overlooked.
The successful implementation of a flexible production line relies heavily on well-trained personnel who can operate and maintain the new systems efficiently.
Invest in comprehensive training programs to ensure a smooth transition.
Challenges and Solutions
While the benefits of flexible production lines are clear, the path to implementation can be fraught with challenges.
One of the main challenges is the high initial investment cost.
Implementing advanced technology requires significant capital and resources.
However, the long-term savings and competitive advantages justify the investment.
Consider options like leasing equipment or seeking financial incentives to mitigate the upfront costs.
Integration issues can also pose a challenge.
New systems must integrate smoothly with existing ones to avoid disruptions.
Collaborate with technology providers who offer robust support and expertise to ensure seamless integration.
Resistance to change is another common challenge.
Employees may be hesitant to adapt to new procedures and systems.
Address this by involving them early in the process and emphasizing the benefits of the change.
Future Trends in Flexible Manufacturing
The field of flexible manufacturing is continually evolving, driven by advances in technology and changing market demands.
One of the future trends is the increased use of artificial intelligence (AI) to enhance production line flexibility.
AI systems can analyze vast amounts of data to optimize production processes, predict maintenance needs, and even design adaptive production strategies.
Another trend is the growing integration of the Internet of Things (IoT) in manufacturing.
IoT devices provide real-time data across the production line, enabling manufacturers to make informed decisions quickly.
This connectivity allows for improved monitoring, maintenance, and efficiency.
Sustainability is also becoming a significant consideration in flexible production line design.
Manufacturers are increasingly focusing on reducing their carbon footprint by implementing energy-efficient systems and processes.
This trend not only reduces environmental impact but also appeals to environmentally conscious consumers.
Conclusion
For production technology managers in the auto parts manufacturing industry, the shift toward flexible production lines is not just a trend but a necessary evolution for staying competitive.
By comprehensively understanding the benefits, key considerations, and challenges, you can effectively design and implement a successful flexible manufacturing system.
Embrace the future trends of AI, IoT, and sustainability to keep your production processes at the forefront of innovation.
With careful planning and investment, flexible production lines can transform your operations, providing the agility needed to thrive in a dynamic market landscape.
資料ダウンロード
QCD調達購買管理クラウド「newji」は、調達購買部門で必要なQCD管理全てを備えた、現場特化型兼クラウド型の今世紀最高の購買管理システムとなります。
ユーザー登録
調達購買業務の効率化だけでなく、システムを導入することで、コスト削減や製品・資材のステータス可視化のほか、属人化していた購買情報の共有化による内部不正防止や統制にも役立ちます。
NEWJI DX
製造業に特化したデジタルトランスフォーメーション(DX)の実現を目指す請負開発型のコンサルティングサービスです。AI、iPaaS、および先端の技術を駆使して、製造プロセスの効率化、業務効率化、チームワーク強化、コスト削減、品質向上を実現します。このサービスは、製造業の課題を深く理解し、それに対する最適なデジタルソリューションを提供することで、企業が持続的な成長とイノベーションを達成できるようサポートします。
オンライン講座
製造業、主に購買・調達部門にお勤めの方々に向けた情報を配信しております。
新任の方やベテランの方、管理職を対象とした幅広いコンテンツをご用意しております。
お問い合わせ
コストダウンが利益に直結する術だと理解していても、なかなか前に進めることができない状況。そんな時は、newjiのコストダウン自動化機能で大きく利益貢献しよう!
(Β版非公開)