- お役立ち記事
- Mastering the Craft: How Japanese Manufacturers Excel in Wire-Formed Products
Mastering the Craft: How Japanese Manufacturers Excel in Wire-Formed Products
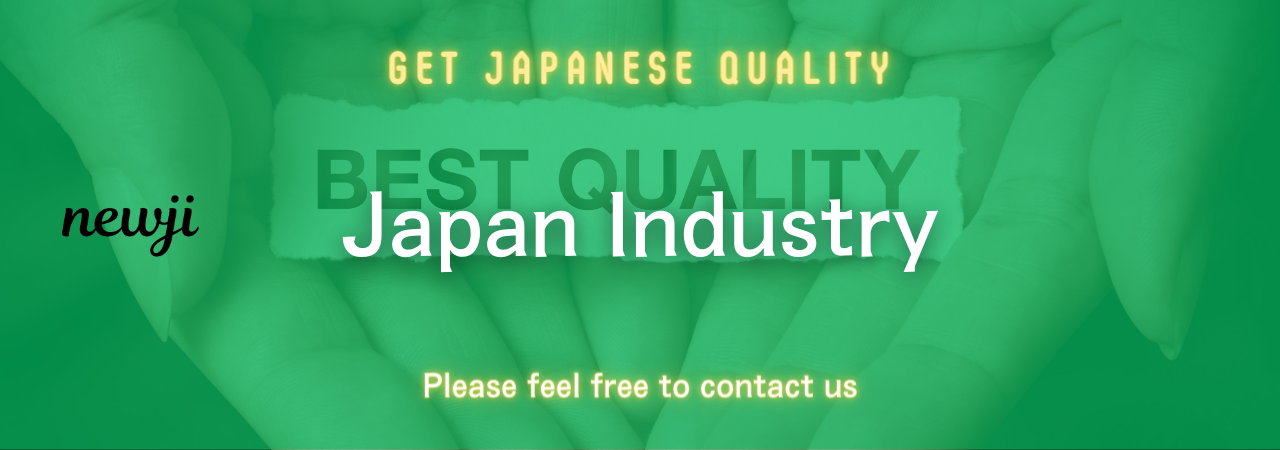
目次
Understanding the Excellence of Japanese Manufacturers in Wire-Formed Products
Japanese manufacturers have long been revered for their precision, quality, and innovation, particularly in the realm of wire-formed products. This excellence is not a product of chance but the result of meticulous processes, strategic procurement, and a deep-seated commitment to continuous improvement. In this article, we delve into the factors that make Japanese manufacturers leaders in wire-forming, exploring their procurement strategies, quality control measures, supplier relationships, and best practices that other industries can emulate.
Procurement Strategies in Japanese Wire Formation
Emphasis on Supplier Relationships
One of the cornerstones of Japanese manufacturing success is the strong emphasis on building long-term relationships with suppliers. Unlike transactional approaches common in other regions, Japanese companies prioritize trust, reliability, and mutual growth. This collaborative relationship ensures that suppliers are aligned with the manufacturer’s quality standards and production timelines.
Just-In-Time (JIT) Inventory Management
Japanese manufacturers often employ Just-In-Time inventory systems to minimize waste and reduce inventory costs. By receiving materials only as they are needed in the production process, companies can maintain lower inventory levels and increase efficiency. This approach requires precise coordination with suppliers and robust forecasting methods to ensure timely delivery of materials.
Cost Management and Value Engineering
Effective cost management is crucial in maintaining the competitiveness of wire-formed products. Japanese manufacturers leverage value engineering techniques to optimize product design and manufacturing processes, reducing costs without compromising quality. This involves analyzing each component’s function and finding cost-effective alternatives that maintain or enhance product performance.
Quality Control: The Heart of Japanese Manufacturing
Total Quality Management (TQM)
Total Quality Management is a foundational philosophy in Japanese manufacturing. TQM involves every employee in the organization taking responsibility for maintaining high-quality standards. Continuous training, rigorous testing, and a culture that encourages the identification and elimination of defects are integral to this approach.
Kaizen: Continuous Improvement
Kaizen, meaning “continuous improvement,” is deeply embedded in Japanese manufacturing culture. This philosophy encourages incremental improvements in processes, products, and services. By fostering a mindset of ongoing enhancement, manufacturers can adapt to changing market demands and technological advancements, maintaining their competitive edge.
Advanced Quality Assurance Techniques
Japanese manufacturers utilize advanced quality assurance techniques, including statistical process control, Six Sigma, and Failure Mode and Effects Analysis (FMEA). These methods help in identifying potential quality issues early in the production process, allowing for timely interventions and reducing the likelihood of defective products reaching the market.
Supplier Negotiation Techniques
Collaborative Negotiation
In Japan, negotiation with suppliers is seen as a collaborative process aimed at mutual benefit rather than a zero-sum game. This approach fosters long-term partnerships and ensures that both parties are invested in each other’s success. Suppliers are often involved in the early stages of product development, contributing their expertise to enhance product quality and innovation.
Transparency and Open Communication
Transparency is a key element in Japanese supplier negotiations. Clear communication regarding expectations, specifications, and timelines helps in building trust and reducing misunderstandings. Regular meetings and updates ensure that both manufacturers and suppliers are aligned in their goals and can address any issues promptly.
Performance-Based Agreements
Performance-based agreements are commonly used in Japanese procurement practices. These agreements tie supplier compensation to specific performance metrics such as quality, delivery times, and cost savings. This incentivizes suppliers to maintain high standards and continuously seek ways to improve their performance.
Market Conditions and Adaptability
Understanding Global Market Trends
Japanese manufacturers excel in wire-formed products by staying attuned to global market trends and consumer demands. They invest in market research and analysis to anticipate changes and adapt their production strategies accordingly. This proactive approach allows them to innovate and introduce new products that meet emerging needs.
Technological Integration
Embracing cutting-edge technologies is pivotal for Japanese manufacturers. Automation, robotics, and advanced software systems are integrated into the production process to enhance precision, reduce manual errors, and increase efficiency. This technological prowess enables them to produce high-quality wire-formed products consistently.
Flexibility in Production
Flexibility is another strength of Japanese manufacturers. They are adept at adjusting production volumes and processes to respond to fluctuating market demands. This adaptability ensures that they can maintain optimal production levels, minimize downtime, and efficiently manage resources.
Best Practices in Wire-Formed Product Manufacturing
Lean Manufacturing Principles
Lean manufacturing principles are widely adopted in Japanese wire-forming industries. By eliminating waste, optimizing workflows, and focusing on value-added activities, manufacturers can enhance productivity and reduce costs. Techniques such as 5S, Value Stream Mapping, and Kanban systems are integral to implementing lean practices effectively.
Employee Training and Development
Investing in employee training and development is a hallmark of Japanese manufacturing excellence. Continuous education programs ensure that workers are skilled in the latest techniques and technologies. Empowered and knowledgeable employees contribute significantly to maintaining high standards of quality and efficiency.
Sustainability and Environmental Responsibility
Sustainability is increasingly important in Japanese manufacturing. Companies are adopting eco-friendly practices such as recycling materials, reducing energy consumption, and minimizing emissions. Sustainable manufacturing not only benefits the environment but also enhances the company’s reputation and meets the growing consumer demand for green products.
Advantages of Japanese Wire-Formed Products
Unmatched Quality and Precision
Japanese wire-formed products are renowned for their superior quality and precision. Strict quality control measures and meticulous attention to detail ensure that products meet the highest standards, making them reliable and durable for various applications.
Innovation and Technological Advancement
Japanese manufacturers are at the forefront of innovation in wire-forming technology. They continuously invest in research and development to introduce new techniques and materials, pushing the boundaries of what is possible in wire-formed products.
Strong Supply Chain Management
Efficient supply chain management allows Japanese manufacturers to maintain smooth operations and timely deliveries. Their ability to synchronize procurement, production, and distribution processes minimizes delays and ensures that products reach the market promptly.
Challenges and Disadvantages
High Production Costs
While Japanese wire-formed products are top-tier in quality, they often come with higher production costs compared to competitors from other regions. The emphasis on quality, advanced technologies, and skilled labor contributes to these increased costs, which can be a barrier for some buyers.
Rigid Standards and Practices
The stringent standards and traditional practices in Japanese manufacturing, while beneficial for quality, can sometimes lead to rigidity. Adapting to rapid market changes or adopting unconventional methods may be slower compared to more flexible manufacturing cultures.
Language and Cultural Barriers
For international procurement teams, language and cultural differences can pose challenges when dealing with Japanese suppliers. Misunderstandings or miscommunications may arise, requiring additional efforts in relationship management and communication strategies.
Best Practices for International Procurement from Japan
Building Strong Relationships
Establishing trust and building strong relationships with Japanese suppliers is essential. Regular visits, open communication, and demonstrating commitment to mutual success can help bridge cultural gaps and foster a collaborative partnership.
Understanding Japanese Business Etiquette
Familiarity with Japanese business etiquette can significantly enhance procurement interactions. Respect for hierarchy, punctuality, and formal communication styles are important aspects to consider when negotiating and collaborating with Japanese manufacturers.
Leveraging Local Expertise
Hiring local experts or consultants who understand the Japanese market and business practices can be invaluable. These professionals can facilitate smoother negotiations, provide insights into cultural nuances, and help navigate the complexities of international procurement.
Case Studies: Success Stories in Japanese Wire Formation
Case Study 1: Toyota’s Supply Chain Excellence
Toyota is a prime example of Japanese manufacturing excellence, particularly in its wire-forming capabilities. By implementing lean manufacturing and JIT inventory systems, Toyota has created a highly efficient supply chain that minimizes waste and maximizes productivity. Their collaborative relationships with suppliers ensure high-quality components and timely deliveries, contributing to Toyota’s reputation for reliability.
Case Study 2: Panasonic’s Innovation in Wire Technology
Panasonic has leveraged advanced wire-forming technologies to develop innovative products that cater to diverse industries. Their investment in research and development has led to the creation of high-precision wire components used in electronics, automotive, and industrial applications. Panasonic’s commitment to quality and innovation exemplifies the strengths of Japanese manufacturing.
Future Trends in Japanese Wire Formation
Adoption of Industry 4.0
The integration of Industry 4.0 technologies, such as the Internet of Things (IoT), artificial intelligence (AI), and machine learning, is set to further enhance Japanese wire-forming capabilities. These technologies enable real-time monitoring, predictive maintenance, and data-driven decision-making, leading to increased efficiency and reduced downtime.
Sustainable Manufacturing Practices
Sustainability will continue to be a major focus for Japanese manufacturers. Innovations in eco-friendly materials, energy-efficient processes, and waste reduction will drive the next wave of advancements in wire formation, aligning with global environmental standards and consumer preferences.
Global Expansion and Market Diversification
Japanese wire-forming companies are expanding their global footprint, entering new markets, and diversifying their product offerings. By catering to a broader range of industries and regions, these manufacturers are poised to sustain their leadership position in the global market.
Conclusion: Emulating Japanese Excellence in Wire Formation
Japanese manufacturers have set a high standard in the wire-forming industry through their unwavering commitment to quality, strategic procurement practices, and continuous improvement. By adopting similar strategies—such as fostering strong supplier relationships, implementing lean manufacturing principles, and embracing technological advancements—manufacturers worldwide can enhance their own capabilities and compete more effectively in the global market.
The Japanese approach offers valuable lessons in efficiency, precision, and innovation. As the industry evolves, maintaining these core principles while adapting to new trends will be crucial for sustaining excellence in wire-formed product manufacturing.
資料ダウンロード
QCD調達購買管理クラウド「newji」は、調達購買部門で必要なQCD管理全てを備えた、現場特化型兼クラウド型の今世紀最高の購買管理システムとなります。
ユーザー登録
調達購買業務の効率化だけでなく、システムを導入することで、コスト削減や製品・資材のステータス可視化のほか、属人化していた購買情報の共有化による内部不正防止や統制にも役立ちます。
NEWJI DX
製造業に特化したデジタルトランスフォーメーション(DX)の実現を目指す請負開発型のコンサルティングサービスです。AI、iPaaS、および先端の技術を駆使して、製造プロセスの効率化、業務効率化、チームワーク強化、コスト削減、品質向上を実現します。このサービスは、製造業の課題を深く理解し、それに対する最適なデジタルソリューションを提供することで、企業が持続的な成長とイノベーションを達成できるようサポートします。
オンライン講座
製造業、主に購買・調達部門にお勤めの方々に向けた情報を配信しております。
新任の方やベテランの方、管理職を対象とした幅広いコンテンツをご用意しております。
お問い合わせ
コストダウンが利益に直結する術だと理解していても、なかなか前に進めることができない状況。そんな時は、newjiのコストダウン自動化機能で大きく利益貢献しよう!
(Β版非公開)