- お役立ち記事
- Revolutionizing Japanese Manufacturing: The Impact of Heat Fluid Analysis Tools on Electronic Devices
Revolutionizing Japanese Manufacturing: The Impact of Heat Fluid Analysis Tools on Electronic Devices
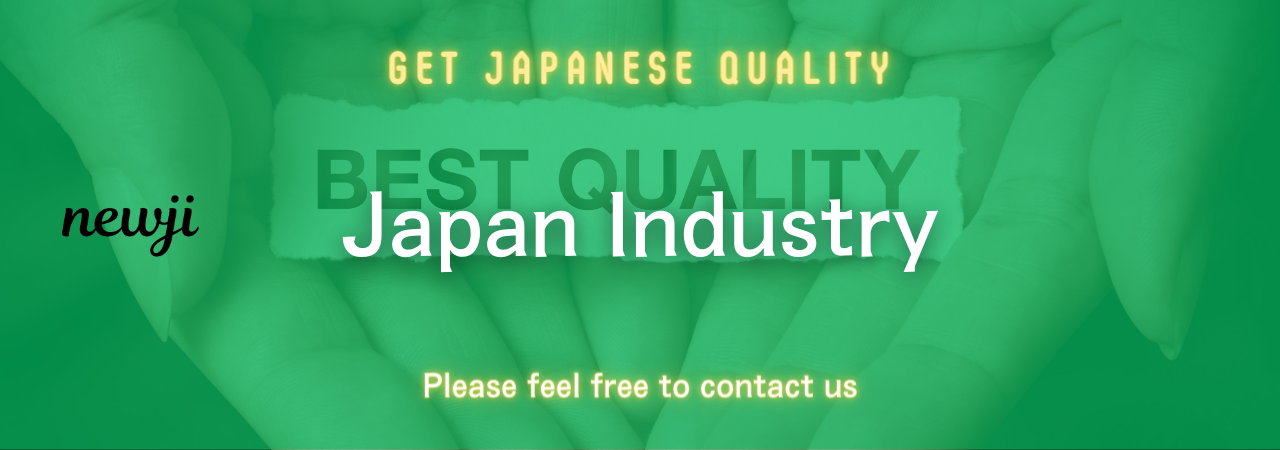
目次
Introduction to Heat Fluid Analysis in Japanese Manufacturing
Japanese manufacturing has long been synonymous with precision, efficiency, and innovation. One of the key areas contributing to this reputation is the advanced use of heat fluid analysis tools in the production of electronic devices. These tools play a pivotal role in ensuring the reliability and performance of electronic components, which are critical in today’s technology-driven world.
Heat fluid analysis involves the study and management of heat transfer within electronic devices. As electronic devices become more compact and powerful, managing heat effectively becomes essential to prevent overheating, which can lead to device failure or reduced lifespan. Japanese manufacturers have embraced heat fluid analysis tools to optimize thermal performance, thereby enhancing the quality and durability of their electronic products.
Understanding Heat Fluid Analysis Tools
Heat fluid analysis tools are sophisticated instruments and software used to model, simulate, and analyze heat transfer and fluid flow within electronic devices. These tools help engineers design systems that efficiently dissipate heat, ensuring that components operate within safe temperature ranges.
Types of Heat Fluid Analysis Tools
There are several types of heat fluid analysis tools utilized in the manufacturing industry:
1. **Computational Fluid Dynamics (CFD) Software**: CFD tools simulate fluid flow and heat transfer within a device, allowing engineers to predict thermal behavior under various operating conditions.
2. **Thermal Imaging Cameras**: These cameras provide real-time visualization of heat distribution across electronic components, aiding in the identification of hotspots and inefficiencies.
3. **Thermocouples and Sensors**: These devices measure temperature at specific points within a system, providing data essential for validating simulation models and optimizing designs.
4. **Finite Element Analysis (FEA) Software**: FEA tools are used to analyze thermal stresses and deformations in materials, ensuring structural integrity under thermal loads.
Applications in Electronic Device Manufacturing
Heat fluid analysis tools are applied in various aspects of electronic device manufacturing, including:
– **PCB Design**: Ensuring optimal layout and component placement to facilitate effective heat dissipation.
– **Power Electronics**: Designing cooling systems for high-power components to maintain operational efficiency.
– **Semiconductor Manufacturing**: Managing heat in chip fabrication processes to achieve precise and reliable semiconductor devices.
– **Consumer Electronics**: Enhancing the thermal management of devices like smartphones, laptops, and gaming consoles to improve performance and user experience.
The Impact on Procurement and Purchasing
The integration of heat fluid analysis tools into Japanese manufacturing processes has significant implications for procurement and purchasing strategies. Understanding these impacts is crucial for businesses looking to collaborate with Japanese suppliers effectively.
Advantages of Heat Fluid Analysis Tools in Procurement
1. **Enhanced Product Quality**: By ensuring effective thermal management, products are less likely to fail due to overheating, leading to higher quality and greater customer satisfaction.
2. **Reduced Manufacturing Costs**: Optimizing heat dissipation can lower the need for additional cooling components, reducing material and production costs.
3. **Faster Time-to-Market**: Advanced simulation tools accelerate the design and testing phases, enabling quicker product launches.
4. **Better Supplier Collaboration**: Detailed thermal analysis facilitates clearer communication between manufacturers and suppliers, ensuring that components meet thermal performance requirements.
Disadvantages and Challenges
1. **High Initial Investment**: Implementing advanced heat fluid analysis tools requires significant upfront investment in software, hardware, and training.
2. **Complexity of Use**: These tools can be complex to operate, necessitating specialized training for procurement and engineering teams.
3. **Integration with Existing Systems**: Aligning new analysis tools with existing manufacturing and procurement systems can be challenging and may require additional resources.
4. **Dependence on Accurate Data**: The effectiveness of heat fluid analysis tools relies on the accuracy of input data, making data collection and validation critical.
Supplier Negotiation Techniques
Effective supplier negotiation is essential for leveraging the benefits of heat fluid analysis tools in procurement. Japanese suppliers often have rigorous standards and expectations, making strategic negotiation approaches necessary.
Building Strong Relationships
Japanese business culture emphasizes long-term relationships and trust. Establishing a strong rapport with suppliers is fundamental to successful negotiations. Regular communication, respect for cultural norms, and demonstrating commitment to mutual success are key factors in building these relationships.
Understanding Supplier Capabilities
Before entering negotiations, it is essential to thoroughly understand the supplier’s capabilities, especially regarding their use of heat fluid analysis tools. This includes:
– **Technical Expertise**: Assess the supplier’s proficiency with thermal management technologies and their ability to meet your product specifications.
– **Production Capacity**: Ensure that the supplier can handle the required production volume without compromising on quality.
– **Innovation Potential**: Evaluate the supplier’s willingness and ability to adopt new technologies and improve processes continuously.
Leveraging Data and Insights
Utilizing data from heat fluid analysis can strengthen negotiation positions. Presenting detailed thermal performance reports and requiring suppliers to meet specific thermal criteria can ensure that the components provided will meet your quality standards. This data-driven approach can also justify pricing and foster transparency.
Collaborative Problem-Solving
Adopting a collaborative approach to negotiations can lead to mutually beneficial outcomes. Working together to address thermal management challenges can result in innovative solutions that enhance product performance and reduce costs for both parties.
Market Conditions and Trends
The global market for electronic devices is highly competitive and rapidly evolving. Understanding current market conditions and trends is vital for optimizing procurement and purchasing strategies in the context of heat fluid analysis.
Increasing Demand for High-Performance Electronics
As technology advances, the demand for high-performance electronics continues to grow. Devices require better thermal management to support increased processing power and functionality. This trend drives the need for sophisticated heat fluid analysis tools to ensure products can meet these higher performance standards.
Shift Towards Miniaturization
The trend towards smaller, more compact electronic devices exacerbates thermal management challenges. Effective heat fluid analysis becomes even more critical as engineers strive to maximize performance within limited physical spaces. Japanese manufacturers are at the forefront of developing innovative solutions to address these challenges.
Sustainability and Energy Efficiency
Sustainability is becoming a key consideration in manufacturing. Efficient thermal management contributes to energy savings and reduces the environmental impact of electronic devices. Companies are increasingly focusing on eco-friendly manufacturing practices, and heat fluid analysis tools play a significant role in achieving these sustainability goals.
Advancements in Material Science
Progress in material science is providing new opportunities for thermal management. Advanced materials with superior thermal conductivity or insulating properties are being integrated into electronic devices. Heat fluid analysis tools help in selecting and optimizing these materials to enhance overall device performance.
Best Practices in Utilizing Heat Fluid Analysis Tools
To maximize the benefits of heat fluid analysis tools, organizations should adopt best practices that encompass strategic planning, effective implementation, and continuous improvement.
Strategic Planning and Integration
Integrate heat fluid analysis tools into the early stages of product design and development. This proactive approach allows for the identification and resolution of thermal issues before they escalate, reducing the need for costly redesigns and delays in production.
Comprehensive Training and Skill Development
Invest in training programs to ensure that procurement and engineering teams are proficient in using heat fluid analysis tools. Skilled personnel can effectively interpret analysis results and make informed decisions that enhance product quality and operational efficiency.
Collaboration Across Departments
Foster collaboration between procurement, engineering, and other relevant departments. Sharing insights from heat fluid analysis can lead to more cohesive and efficient manufacturing processes, as well as stronger supplier relationships.
Continuous Monitoring and Feedback
Implement a system for continuous monitoring and feedback. Regularly review thermal performance data and use it to drive ongoing improvements in product design and manufacturing processes. This iterative approach ensures that thermal management strategies remain effective and up-to-date with technological advancements.
Leveraging Technology and Automation
Adopt advanced technologies and automation to streamline heat fluid analysis processes. Automated data collection and analysis can enhance accuracy, reduce manual errors, and free up resources for more strategic tasks.
Supplier Engagement and Alignment
Engage suppliers in the heat fluid analysis process to ensure alignment with your thermal management objectives. Collaborative efforts in thermal analysis can lead to shared innovations and more robust supply chain integration.
Advantages of Heat Fluid Analysis in Japanese Manufacturing
Japanese manufacturers have successfully leveraged heat fluid analysis tools to gain a competitive edge in the global market. Understanding the specific advantages these tools provide is essential for businesses aiming to benefit from Japanese procurement practices.
Enhanced Product Reliability
By effectively managing heat within electronic devices, Japanese manufacturers ensure higher product reliability. This reliability is a key differentiator in the market, as consumers and businesses alike prioritize products that perform consistently under various conditions.
Improved Design Efficiency
Heat fluid analysis tools enable precise simulations and optimizations, leading to more efficient design processes. This efficiency reduces the time and resources required for prototyping and testing, accelerating the overall development cycle.
Cost Savings
Optimizing thermal management can result in significant cost savings by reducing the need for additional cooling components and minimizing energy consumption. These savings can be passed on to customers, enhancing the competitiveness of Japanese products.
Innovation and Technological Leadership
The use of advanced heat fluid analysis tools fosters a culture of innovation. Japanese manufacturers are able to develop cutting-edge thermal management solutions that set industry standards and drive technological advancements across the sector.
Challenges and Limitations
While heat fluid analysis tools offer numerous benefits, there are also challenges and limitations that organizations must navigate to fully harness their potential.
High Initial Costs
The cost of acquiring and implementing advanced heat fluid analysis tools can be prohibitive, especially for smaller manufacturers. Budget constraints may limit the ability to invest in the latest technologies, potentially impacting competitiveness.
Technical Complexity
The complexity of heat fluid analysis tools requires specialized knowledge and expertise. Without sufficient training and skilled personnel, organizations may struggle to effectively utilize these tools, diminishing their potential benefits.
Data Accuracy and Reliability
The precision of heat fluid analysis is heavily dependent on the accuracy of input data. Inaccurate or incomplete data can lead to flawed analyses, resulting in suboptimal design decisions and compromised product performance.
Integration Challenges
Integrating heat fluid analysis tools with existing manufacturing and procurement systems can be challenging. Compatibility issues and the need for system upgrades can disrupt operations and require additional investments.
Rapid Technological Advancements
The fast-paced nature of technological advancements means that heat fluid analysis tools must be regularly updated to remain effective. Keeping up with the latest developments requires continuous investment in software updates and training.
Future Outlook and Trends
The role of heat fluid analysis tools in Japanese manufacturing is set to expand as the electronics industry continues to evolve. Several trends are shaping the future of thermal management and procurement practices.
Integration with Artificial Intelligence and Machine Learning
AI and machine learning are being integrated into heat fluid analysis tools to enhance predictive capabilities and optimize thermal management strategies. These technologies can identify patterns and insights that improve the accuracy and efficiency of thermal analyses.
Internet of Things (IoT) and Smart Manufacturing
The rise of IoT and smart manufacturing is transforming thermal management practices. Connected devices can provide real-time data on thermal performance, enabling dynamic adjustments and more responsive thermal management systems.
Sustainable and Eco-Friendly Solutions
Sustainability remains a key focus in manufacturing. Future heat fluid analysis tools will emphasize eco-friendly thermal management solutions that reduce energy consumption and minimize environmental impact.
Advanced Materials and Nanotechnology
Advancements in materials science and nanotechnology will introduce new options for thermal management. Heat fluid analysis tools will evolve to accommodate and leverage these innovative materials, further enhancing thermal performance.
Global Collaboration and Standardization
As manufacturing becomes more globalized, there will be increased collaboration and standardization in thermal management practices. Heat fluid analysis tools will play a critical role in ensuring consistent standards and facilitating cross-border collaborations.
Best Practices for Procurement Professionals
Procurement professionals can adopt several best practices to effectively utilize heat fluid analysis tools in their strategies, ensuring optimal outcomes in collaboration with Japanese suppliers.
Early Involvement in Design Process
Engage with suppliers and engineering teams early in the design process. This allows for the integration of thermal management considerations from the outset, leading to more efficient and effective product designs.
Establish Clear Thermal Performance Criteria
Define clear thermal performance criteria and communicate them to suppliers. Ensuring that all parties understand the thermal requirements helps in aligning efforts towards meeting these standards.
Implement Robust Quality Assurance Processes
Develop and implement quality assurance processes that include thermal performance validation. Regular testing and verification ensure that products consistently meet thermal management standards.
Foster Continuous Improvement
Encourage a culture of continuous improvement by regularly reviewing thermal performance data and seeking feedback from suppliers. Use this information to drive ongoing enhancements in thermal management practices.
Leverage Data Analytics
Utilize data analytics to gain deeper insights into thermal performance trends and patterns. Advanced analytics can help identify areas for improvement and inform strategic procurement decisions.
Enhance Supplier Training and Support
Provide training and support to suppliers on the effective use of heat fluid analysis tools. Empowering suppliers with the necessary skills and knowledge enhances their ability to meet thermal management requirements.
Negotiate Flexible Contracts
Structure contracts to allow for flexibility in thermal management solutions. This accommodates evolving technologies and enables suppliers to adopt new thermal management strategies as they become available.
Case Studies: Success Stories in Japanese Manufacturing
Examining real-world examples of how Japanese manufacturers have successfully implemented heat fluid analysis tools provides valuable insights into best practices and potential benefits.
Case Study 1: Semiconductor Manufacturing
A leading Japanese semiconductor manufacturer integrated advanced CFD software into their production process. By simulating heat transfer within semiconductor chips, they were able to identify and eliminate thermal hotspots. This led to a 15% increase in chip reliability and a 10% reduction in production costs due to decreased material usage for cooling components.
Case Study 2: Consumer Electronics
A Japanese consumer electronics company utilized thermal imaging cameras and FEA software to optimize the design of their flagship smartphone. By effectively managing heat dissipation, they improved device performance and extended battery life. The optimized thermal design contributed to a 20% increase in customer satisfaction and a 12% boost in sales.
Case Study 3: Automotive Electronics
In the automotive sector, a Japanese manufacturer employed heat fluid analysis tools to enhance the thermal management of electronic control units (ECUs). This resulted in more efficient cooling systems, reduced energy consumption, and improved overall vehicle performance. The advancements not only enhanced product quality but also positioned the company as a leader in automotive thermal management solutions.
Conclusion
Heat fluid analysis tools have revolutionized Japanese manufacturing, particularly in the realm of electronic devices. These tools provide critical insights into thermal management, enabling the design of more reliable, efficient, and high-performing products. For procurement and purchasing professionals, understanding the impact of these tools is essential for building effective supplier relationships and optimizing supply chain strategies.
Japanese manufacturers’ commitment to precision and innovation in thermal management serves as a benchmark for the global industry. By adopting best practices, leveraging advanced technologies, and fostering strong supplier collaborations, businesses can harness the full potential of heat fluid analysis tools. As the electronic devices market continues to evolve, the integration of sophisticated thermal management solutions will remain a key driver of success and competitiveness in manufacturing.
資料ダウンロード
QCD調達購買管理クラウド「newji」は、調達購買部門で必要なQCD管理全てを備えた、現場特化型兼クラウド型の今世紀最高の購買管理システムとなります。
ユーザー登録
調達購買業務の効率化だけでなく、システムを導入することで、コスト削減や製品・資材のステータス可視化のほか、属人化していた購買情報の共有化による内部不正防止や統制にも役立ちます。
NEWJI DX
製造業に特化したデジタルトランスフォーメーション(DX)の実現を目指す請負開発型のコンサルティングサービスです。AI、iPaaS、および先端の技術を駆使して、製造プロセスの効率化、業務効率化、チームワーク強化、コスト削減、品質向上を実現します。このサービスは、製造業の課題を深く理解し、それに対する最適なデジタルソリューションを提供することで、企業が持続的な成長とイノベーションを達成できるようサポートします。
オンライン講座
製造業、主に購買・調達部門にお勤めの方々に向けた情報を配信しております。
新任の方やベテランの方、管理職を対象とした幅広いコンテンツをご用意しております。
お問い合わせ
コストダウンが利益に直結する術だと理解していても、なかなか前に進めることができない状況。そんな時は、newjiのコストダウン自動化機能で大きく利益貢献しよう!
(Β版非公開)