- お役立ち記事
- On-site reforms to prevent human errors—Specific measures from a management perspective
On-site reforms to prevent human errors—Specific measures from a management perspective
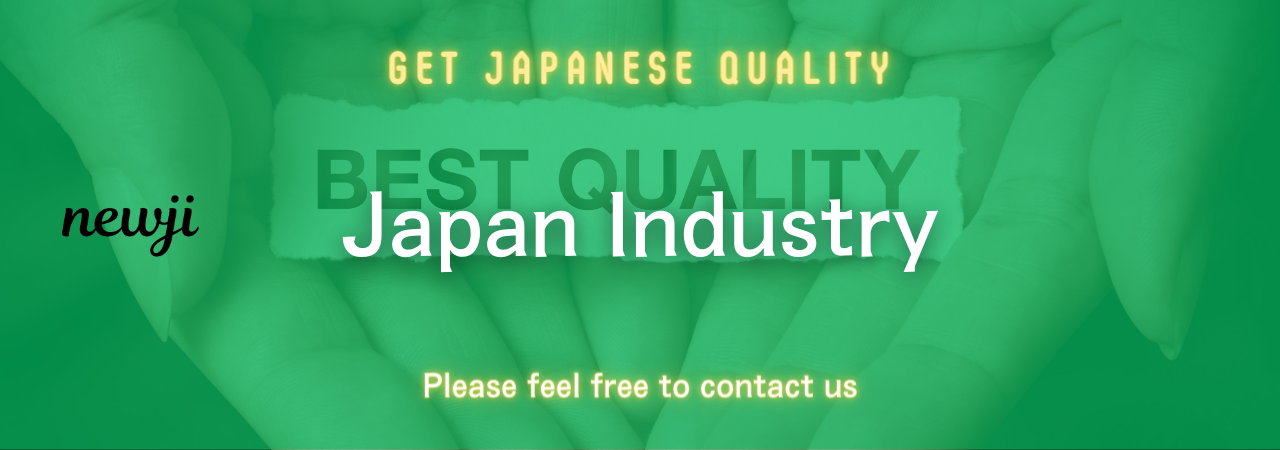
目次
Understanding Human Errors in the Workplace
Human errors are inevitable in any workplace, whether it is due to distractions, miscommunications, or sheer oversight.
These mistakes can potentially lead to significant consequences, such as financial losses or even compromising safety standards.
However, by understanding the root causes of human errors, management can implement strategies aimed at reducing their frequency and impact.
This requires a conscientious effort to analyze the working environment, understand the dynamics between team members, and make necessary reforms.
The Role of Management in Addressing Human Errors
Management plays a crucial role in mitigating human errors.
Their perspective not only influences the work culture but also determines how efficiently procedures are executed.
A proactive management approach can create an environment where errors are less likely to occur and are rectified promptly when they do.
This involves setting clear expectations, promoting open communication, and investing in employee training and development.
Specific Measures to Prevent Human Errors
1. Enhance Communication Channels
Clear communication is key to ensuring that everyone understands their roles and responsibilities.
Miscommunication often leads to mistakes, so it is important to establish effective communication channels.
Encourage an open-door policy where employees feel comfortable discussing any uncertainties or issues they encounter.
Regular team meetings and updates can also help reinforce the importance of effective communication.
2. Implement Comprehensive Training Programs
Continuous training and development are essential to minimizing human errors.
Comprehensive programs should include orientation for new hires as well as ongoing training sessions for existing staff.
Training should not only focus on job-specific skills but also on critical thinking, decision-making, and problem-solving abilities.
Offer workshops, seminars, and other learning opportunities to ensure employees remain informed about the latest industry standards and practices.
3. Establish Clear Standard Operating Procedures (SOPs)
Having clear and concise SOPs is critical in preventing human errors.
Procedures should be documented, easily accessible, and regularly reviewed to reflect any changes in processes or regulations.
These guidelines should be straightforward enough for all employees to understand and follow consistently.
Involve employees in the creation and updating of SOPs to ensure they are practical and applicable to real-world situations.
4. Utilize Technology and Automation
Technology can be a considerable asset in minimizing human errors.
Automating routine tasks can free up time for employees to focus on more complex activities that require human judgment and creativity.
Utilize tools such as project management software, automated checklists, and reminders to keep tasks on track and ensure nothing is overlooked.
Additionally, using technology to monitor and analyze processes can help identify patterns or potential issues before they lead to errors.
5. Foster a Culture of Accountability and Transparency
Encouraging a culture of accountability ensures that employees understand the importance of their contributions and recognize the impact of their actions.
Promote transparency by encouraging employees to speak up when they identify potential risks or witness errors.
Instead of placing blame when mistakes occur, focus on finding solutions and learning opportunities.
This approach promotes a safe environment where employees feel empowered to grow and improve.
Monitoring and Continuous Improvement
1. Conduct Regular Audits and Assessments
Regular audits and assessments help management identify areas prone to human errors.
Develop a comprehensive checklist to evaluate processes, identify weak points, and track compliance with established procedures.
By continually assessing the workplace, management can promptly address issues before they escalate into larger problems.
2. Solicit Feedback from Employees
Employees are an invaluable resource for identifying and preventing potential errors.
Regularly solicit feedback from staff to gain insight into day-to-day operations and gather suggestions for improvements.
Act on this feedback and involve employees in the decision-making process whenever possible.
This promotes a sense of ownership and can lead to the implementation of effective solutions that management may not have considered.
3. Review and Adapt Strategies
It’s essential for management to continually review and adapt strategies aimed at reducing human errors.
As the business environment changes, so too must the approaches to managing errors.
Stay informed about industry trends and emerging best practices, and be willing to make adjustments to existing procedures when necessary.
Set performance metrics to evaluate the effectiveness of error-prevention strategies and make changes as needed.
Conclusion
Preventing human errors in the workplace requires an ongoing commitment from management to support a culture of safety, communication, and continuous improvement.
By implementing structured measures and leveraging feedback and technology, businesses can significantly reduce the occurrence and impact of human errors.
Ultimately, fostering a proactive and adaptive work environment ensures a more efficient, safe, and productive workplace for all.
資料ダウンロード
QCD調達購買管理クラウド「newji」は、調達購買部門で必要なQCD管理全てを備えた、現場特化型兼クラウド型の今世紀最高の購買管理システムとなります。
ユーザー登録
調達購買業務の効率化だけでなく、システムを導入することで、コスト削減や製品・資材のステータス可視化のほか、属人化していた購買情報の共有化による内部不正防止や統制にも役立ちます。
NEWJI DX
製造業に特化したデジタルトランスフォーメーション(DX)の実現を目指す請負開発型のコンサルティングサービスです。AI、iPaaS、および先端の技術を駆使して、製造プロセスの効率化、業務効率化、チームワーク強化、コスト削減、品質向上を実現します。このサービスは、製造業の課題を深く理解し、それに対する最適なデジタルソリューションを提供することで、企業が持続的な成長とイノベーションを達成できるようサポートします。
オンライン講座
製造業、主に購買・調達部門にお勤めの方々に向けた情報を配信しております。
新任の方やベテランの方、管理職を対象とした幅広いコンテンツをご用意しております。
お問い合わせ
コストダウンが利益に直結する術だと理解していても、なかなか前に進めることができない状況。そんな時は、newjiのコストダウン自動化機能で大きく利益貢献しよう!
(Β版非公開)