- お役立ち記事
- “Exploring the Role of Polyethylene OEMs in Japan’s Advanced Manufacturing Sector”
“Exploring the Role of Polyethylene OEMs in Japan’s Advanced Manufacturing Sector”
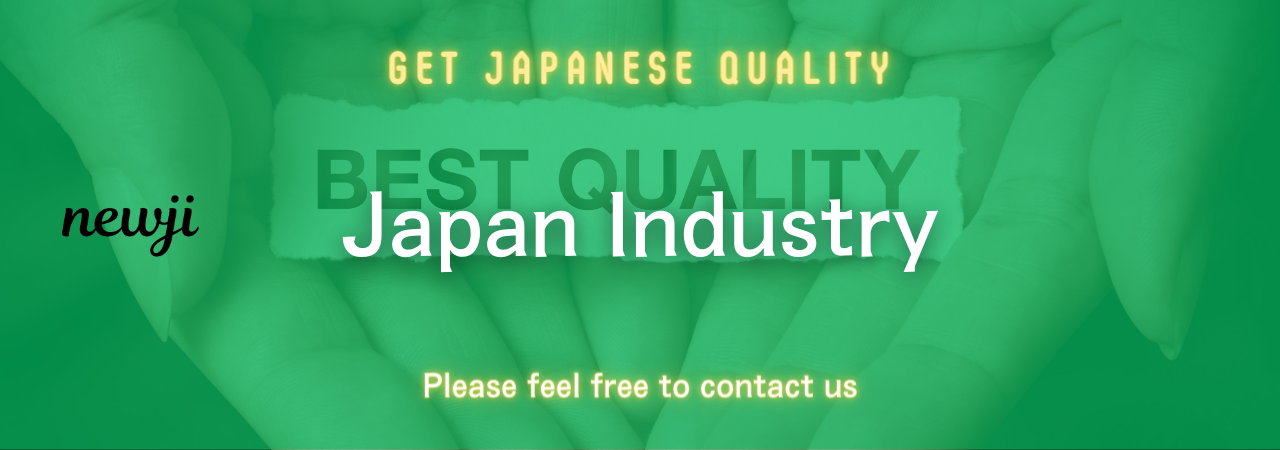
目次
Understanding Polyethylene OEMs in Japan
Polyethylene Original Equipment Manufacturers (OEMs) in Japan play a pivotal role in the country’s advanced manufacturing sector. These companies specialize in producing polyethylene materials, which are essential components in various industries, including automotive, electronics, packaging, and consumer goods. By partnering with Japanese Polyethylene OEMs, manufacturers can access high-quality materials that meet stringent industry standards.
Japan’s reputation for precision engineering and innovation is reflected in its polyethylene OEMs. These manufacturers invest heavily in research and development, ensuring that their products incorporate the latest advancements in material science. This commitment to quality and innovation makes Japanese Polyethylene OEMs attractive partners for global manufacturing companies seeking reliable and cutting-edge materials.
The Importance of Polyethylene in Manufacturing
Polyethylene is one of the most widely used polymers in the world, valued for its versatility, durability, and cost-effectiveness. In manufacturing, polyethylene serves as a fundamental material in the production of a diverse range of products. Its applications span from packaging materials and household goods to automotive parts and electronic components.
The unique properties of polyethylene, such as its lightweight nature, flexibility, and resistance to chemicals and moisture, make it indispensable in various manufacturing processes. Additionally, advancements in polyethylene technology have led to the development of specialized grades, tailored to meet specific performance requirements. This adaptability ensures that manufacturers can select the right type of polyethylene for their unique applications, enhancing product quality and performance.
Advantages of Partnering with Japanese Polyethylene OEMs
Collaborating with Japanese Polyethylene OEMs offers numerous advantages for manufacturers. One of the primary benefits is access to high-quality materials that adhere to rigorous quality control standards. Japanese manufacturers are known for their meticulous attention to detail, ensuring that each batch of polyethylene meets or exceeds industry specifications.
Another advantage is the emphasis on innovation. Japanese OEMs invest significantly in research and development, continually improving their polyethylene products and developing new formulations to meet evolving market demands. This focus on innovation allows manufacturers to stay ahead of the competition by incorporating the latest material advancements into their products.
Additionally, Japanese Polyethylene OEMs often provide comprehensive technical support and expertise. This partnership approach facilitates smooth integration of polyethylene materials into manufacturing processes, minimizing disruptions and enhancing overall efficiency.
Disadvantages and Challenges
While there are many benefits to partnering with Japanese Polyethylene OEMs, there are also potential challenges to consider. One of the primary disadvantages is the higher cost associated with importing materials from Japan compared to sourcing from domestic suppliers. Exchange rate fluctuations and shipping costs can impact the overall expenditure, making budget management more complex.
Another challenge is the complexity of communication and cultural differences. Japanese business practices and communication styles may differ significantly from those in other regions, potentially leading to misunderstandings or delays. Effective cross-cultural communication strategies are essential to mitigate these issues and ensure a productive partnership.
Furthermore, lead times for receiving materials from Japan can be longer compared to local suppliers. This extended timeframe may affect production schedules, requiring careful planning and inventory management to prevent shortages and maintain seamless operations.
Supplier Negotiation Techniques with Japanese OEMs
Successful negotiations with Japanese Polyethylene OEMs require a strategic approach that respects cultural norms and business practices. Building strong relationships based on trust and mutual respect is crucial in Japanese business culture. Taking the time to develop a rapport with OEM representatives can lead to more favorable negotiation outcomes.
Understanding the value of long-term partnerships is essential. Japanese manufacturers often prefer stable, ongoing relationships over one-time transactions. Demonstrating a commitment to a long-term collaboration can enhance bargaining power and result in better terms and pricing.
Additionally, being well-prepared with clear and detailed specifications can facilitate smoother negotiations. Presenting a thorough understanding of the required polyethylene grades, quality standards, and delivery expectations shows professionalism and fosters confidence in the partnership.
Flexibility in negotiations is also important. Being open to compromises and finding mutually beneficial solutions can help overcome obstacles and achieve agreement on key terms.
Market Conditions in Japan’s Advanced Manufacturing Sector
Japan’s advanced manufacturing sector is characterized by its emphasis on technology, quality, and efficiency. The sector is a significant contributor to the global economy, with industries such as automotive, electronics, and machinery at the forefront of innovation. Polyethylene OEMs in Japan operate within this dynamic environment, continuously adapting to market trends and technological advancements.
The demand for high-performance polyethylene materials is driven by the need for lightweight and durable solutions in various applications. As industries strive for greater efficiency and sustainability, the role of polyethylene as a versatile and recyclable material becomes increasingly important.
Economic factors, such as domestic consumption trends and global trade dynamics, also impact the market conditions for Japanese Polyethylene OEMs. Staying attuned to these factors allows manufacturers to anticipate changes in supply and demand, enabling proactive adjustments to procurement strategies.
Best Practices for Procurement and Purchasing
Implementing best practices in procurement and purchasing is essential for maximizing the benefits of partnering with Japanese Polyethylene OEMs. One such practice is establishing clear and comprehensive contracts that outline specifications, delivery schedules, pricing, and quality standards. Clear agreements help prevent misunderstandings and ensure that both parties are aligned in their expectations.
Engaging in regular performance evaluations is another best practice. Monitoring the quality, delivery performance, and overall satisfaction with the OEM allows for continuous improvement and early identification of potential issues.
Diversifying the supplier base can also mitigate risks associated with relying on a single source. While Japanese Polyethylene OEMs offer significant advantages, having alternative suppliers ensures that production remains uninterrupted in case of unforeseen disruptions.
Furthermore, investing in supply chain visibility and transparency enhances coordination and reduces lead times. Utilizing advanced procurement software and fostering open communication channels with OEMs helps streamline the procurement process and improve overall efficiency.
Case Studies and Real-World Applications
Examining real-world case studies can provide valuable insights into the successful integration of Japanese Polyethylene OEMs in manufacturing processes. For instance, a leading automotive manufacturer partnered with a Japanese Polyethylene OEM to source specialized polyethylene components for electric vehicles. The collaboration resulted in the development of lightweight, high-strength parts that contributed to the overall efficiency and performance of the vehicles.
In another example, a consumer electronics company worked with a Japanese OEM to source innovative polyethylene packaging solutions. The partnership enabled the company to create eco-friendly, durable packaging that enhanced product protection and reduced environmental impact, aligning with the company’s sustainability goals.
These case studies highlight the tangible benefits of collaborating with Japanese Polyethylene OEMs, demonstrating how strategic partnerships can drive product innovation, enhance quality, and support business objectives.
Future Trends in Polyethylene Manufacturing
The polyethylene manufacturing landscape is continually evolving, driven by advancements in technology and shifting market demands. One of the key future trends is the development of bio-based and biodegradable polyethylene materials. As sustainability becomes a central focus for industries worldwide, the demand for environmentally friendly polyethylene alternatives is expected to rise.
Another trend is the integration of smart manufacturing practices, such as automation and the Internet of Things (IoT), into polyethylene production. These technologies enhance production efficiency, reduce waste, and enable real-time monitoring of manufacturing processes, leading to higher quality products and lower costs.
Additionally, the customization of polyethylene materials to meet specific application requirements is set to increase. Japanese Polyethylene OEMs are likely to continue investing in research and development to create tailored solutions that address the unique needs of various industries, providing manufacturers with more options to optimize their products.
Conclusion
Japanese Polyethylene OEMs play a crucial role in Japan’s advanced manufacturing sector, offering high-quality, innovative polyethylene materials that support a wide range of industries. While partnering with these OEMs presents certain challenges, such as higher costs and cultural differences, the advantages of access to superior materials, technical expertise, and a commitment to innovation make them valuable partners for manufacturers worldwide.
By employing effective procurement strategies, understanding market conditions, and adopting best practices, manufacturers can maximize the benefits of collaborating with Japanese Polyethylene OEMs. As the manufacturing landscape continues to evolve, the role of these OEMs is set to grow, driven by ongoing advancements in polyethylene technology and a focus on sustainability and efficiency.
Investing in strong partnerships with Japanese Polyethylene OEMs not only enhances product quality and performance but also positions manufacturers to leverage the latest innovations in material science, ensuring long-term success in a competitive global market.
資料ダウンロード
QCD調達購買管理クラウド「newji」は、調達購買部門で必要なQCD管理全てを備えた、現場特化型兼クラウド型の今世紀最高の購買管理システムとなります。
ユーザー登録
調達購買業務の効率化だけでなく、システムを導入することで、コスト削減や製品・資材のステータス可視化のほか、属人化していた購買情報の共有化による内部不正防止や統制にも役立ちます。
NEWJI DX
製造業に特化したデジタルトランスフォーメーション(DX)の実現を目指す請負開発型のコンサルティングサービスです。AI、iPaaS、および先端の技術を駆使して、製造プロセスの効率化、業務効率化、チームワーク強化、コスト削減、品質向上を実現します。このサービスは、製造業の課題を深く理解し、それに対する最適なデジタルソリューションを提供することで、企業が持続的な成長とイノベーションを達成できるようサポートします。
オンライン講座
製造業、主に購買・調達部門にお勤めの方々に向けた情報を配信しております。
新任の方やベテランの方、管理職を対象とした幅広いコンテンツをご用意しております。
お問い合わせ
コストダウンが利益に直結する術だと理解していても、なかなか前に進めることができない状況。そんな時は、newjiのコストダウン自動化機能で大きく利益貢献しよう!
(Β版非公開)