- お役立ち記事
- Differences between “single item procurement” and “multiple item procurement”—Options for purchasing departments to improve efficiency
Differences between “single item procurement” and “multiple item procurement”—Options for purchasing departments to improve efficiency
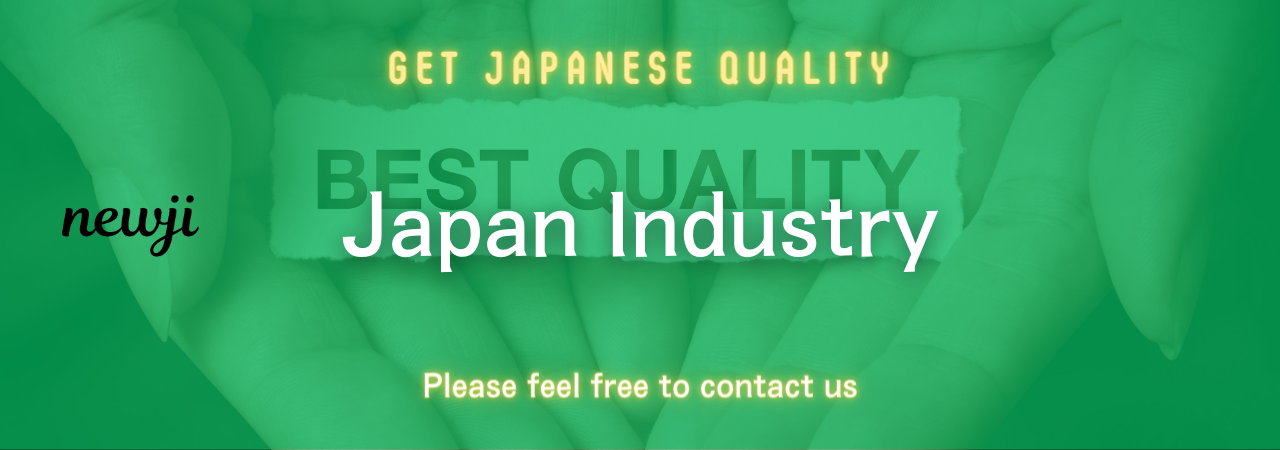
目次
Understanding Single Item Procurement and Multiple Item Procurement
When it comes to procurement, the selection of whether to purchase single items or multiple items can make a significant difference in the efficiency of an organization’s purchasing department.
Each approach has its unique advantages and potential drawbacks that purchasing managers must understand to make informed decisions.
Let’s dive deeper into what these procurement strategies entail and how they can be effectively utilized.
What is Single Item Procurement?
Single item procurement refers to the purchase of a unique or individual item as needed.
This approach is typically used when the demand for a specific product is low or when the product is highly specialized.
Organizations may choose this strategy for several reasons.
First, it reduces the risk of overstocking items that may not sell or be in constant demand.
Since the procurement process focuses on individual needs, it ensures that the resources of a company are used efficiently, thereby preventing waste.
Single item procurement also allows organizations to tailor their purchasing strategies to meet specific or urgent requirements.
For instance, when a rare part is needed for maintenance or repair, single item procurement is the ideal method to ensure timely sourcing without unnecessary inventory expansion.
Advantages of Single Item Procurement
One of the primary benefits of single item procurement is the flexibility it offers.
It allows businesses to adapt quickly to changes in demand, avoiding excess stock that ties up capital and storage space.
Moreover, organizations can benefit from maintaining closer relationships with suppliers, negotiating better terms for unique items, and ensuring quality through careful selection.
Furthermore, single item procurement can contribute to improved cash flow management.
With minimal investment in inventory, companies can allocate financial resources to other areas of operation that might need support or development.
Challenges of Single Item Procurement
Though beneficial in certain situations, single item procurement does present some challenges.
There is a potential for higher per-unit costs, as bulk pricing discounts are usually unavailable.
Sourcing individual items also requires more effort and time in supplier negotiations and logistics management, which can increase the total cost of procurement.
Additionally, relying solely on single item procurement may lead to longer lead times.
If suppliers are not readily available or if items are back-ordered, this could delay operations, impacting productivity.
The Concept of Multiple Item Procurement
Multiple item procurement involves purchasing products in bulk or as a part of a broader order to fulfill larger scale needs.
This method is prevalent among larger organizations or those dealing with high-demand products.
By ordering multiple items at once, companies often benefit from discounted rates, reducing the overall cost per unit and maximizing efficiency.
This procurement strategy is best suited for items that are standard to the company’s operations and required consistently over time.
For example, a retail store may use multiple item procurement to stock common items such as packaging supplies or best-selling products.
By doing so, it maintains inventory levels, ensuring immediate availability and steady operations.
Benefits of Multiple Item Procurement
One of the foremost advantages of multiple item procurement is cost reduction through bulk purchasing.
Volume discounts can significantly decrease the per-unit cost, reducing the expense burden on the company’s budget.
Furthermore, having a larger inventory on hand can mitigate risks associated with supply chain disruptions, market fluctuations, or supplier shortages.
This approach also streamlines the procurement process, reducing the frequency of orders.
With fewer transactions needed, administrative time and costs are minimized, enabling the department to focus on strategic improvements rather than repetitive tasks.
Drawbacks of Multiple Item Procurement
The main disadvantage of multiple item procurement is the potential for overstock.
It requires more storage space and increases the risk of items becoming obsolete or reaching expiration before they are used.
This can result in tied-up capital and excess products taking up valuable warehousing capacity.
Another consideration is the impact on cash flow.
Purchasing in bulk can lead to significant initial expenditures, which might strain financial resources and reduce the flexibility to respond to unforeseen economic or market changes.
Choosing the Right Procurement Strategy
For purchasing departments aiming to enhance efficiency, understanding their operational needs and market dynamics is crucial in choosing between single item procurement and multiple item procurement.
Factors such as product demand variability, storage capacity, and financial resources should inform this decision.
Where demand is predictable, multiple item procurement can offer significant savings and ensure product availability.
Conversely, in industries with rapidly changing trends or specific requirements, single item procurement can provide the necessary agility and focus without risking heavy investments in inventory.
Purchasing managers often find a hybrid approach beneficial, capitalizing on the strengths of both strategies.
By combining single and multiple procurement methods, organizations can tailor their purchasing activities to varying needs, seasons, or market conditions with greater effectiveness.
Conclusion
In summary, the choice between single item procurement and multiple item procurement can substantially impact the purchasing department’s efficiency and the company’s bottom line.
By thoroughly understanding the advantages and drawbacks of each and taking the time to assess organizational requirements, purchasing departments can develop strategic procurement plans that ensure cost-effectiveness, quality, and operational efficiency.
資料ダウンロード
QCD調達購買管理クラウド「newji」は、調達購買部門で必要なQCD管理全てを備えた、現場特化型兼クラウド型の今世紀最高の購買管理システムとなります。
ユーザー登録
調達購買業務の効率化だけでなく、システムを導入することで、コスト削減や製品・資材のステータス可視化のほか、属人化していた購買情報の共有化による内部不正防止や統制にも役立ちます。
NEWJI DX
製造業に特化したデジタルトランスフォーメーション(DX)の実現を目指す請負開発型のコンサルティングサービスです。AI、iPaaS、および先端の技術を駆使して、製造プロセスの効率化、業務効率化、チームワーク強化、コスト削減、品質向上を実現します。このサービスは、製造業の課題を深く理解し、それに対する最適なデジタルソリューションを提供することで、企業が持続的な成長とイノベーションを達成できるようサポートします。
オンライン講座
製造業、主に購買・調達部門にお勤めの方々に向けた情報を配信しております。
新任の方やベテランの方、管理職を対象とした幅広いコンテンツをご用意しております。
お問い合わせ
コストダウンが利益に直結する術だと理解していても、なかなか前に進めることができない状況。そんな時は、newjiのコストダウン自動化機能で大きく利益貢献しよう!
(Β版非公開)