- お役立ち記事
- “Improving inventory management” promoted by collaboration between management and the field—optimizing the flow from procurement to shipping
“Improving inventory management” promoted by collaboration between management and the field—optimizing the flow from procurement to shipping
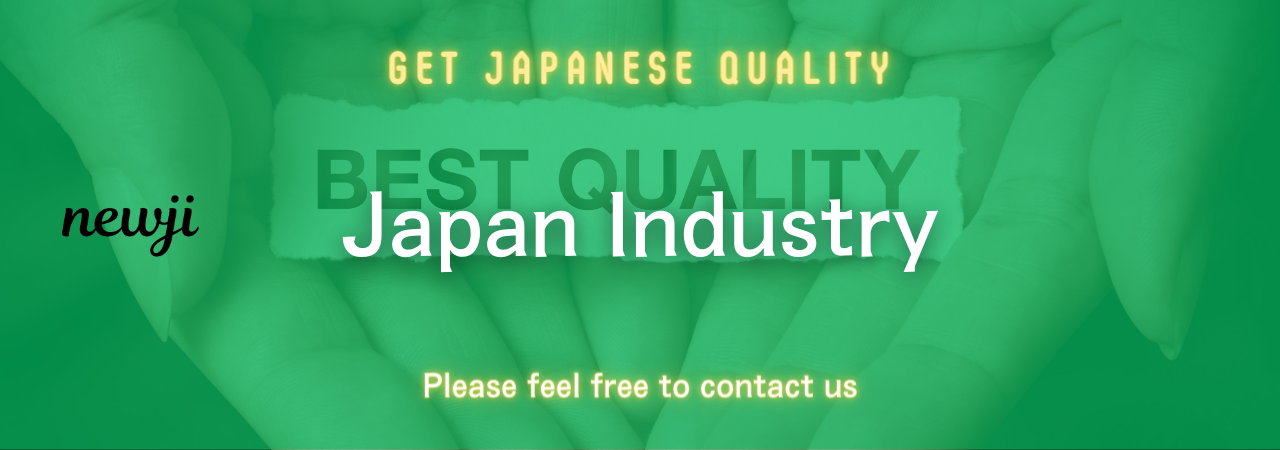
目次
Understanding Inventory Management
Inventory management is a crucial aspect of any business that deals with physical products.
It involves overseeing the flow of goods from the point of procurement to the point of sale.
Effective inventory management ensures that a company can meet customer demand while keeping costs down.
This is why optimizing the inventory management process is essential for business success.
In recent years, collaboration between management and the field has become increasingly important in improving inventory management.
The Importance of Collaboration
Collaboration between management and the field is key to successful inventory management.
Management needs to have a clear understanding of what is happening on the ground to make informed decisions.
On the other hand, field staff needs the support and resources from management to perform their tasks efficiently.
By working together, both management and field staff can identify areas for improvement and develop strategies to optimize the flow of inventory.
Optimizing Procurement
One of the first steps in improving inventory management is optimizing the procurement process.
This involves sourcing the right products at the right price and ensuring a steady supply.
Management can collaborate with procurement teams to negotiate better deals with suppliers and place orders that match demand forecasts.
Field staff can provide valuable insights into the accuracy of these forecasts, allowing management to adjust orders as needed.
This collaboration helps minimize excess inventory and reduce costs associated with overstocking.
Streamlining Inventory Control
Effective inventory control is essential for maintaining the right balance of stock.
Collaboration can help streamline inventory control processes by promoting transparency and communication.
Management can implement inventory management systems that provide real-time data, making it easier to track stock levels and make informed decisions.
Field staff can use this data to ensure that shelves are stocked appropriately and that products are rotated to prevent spoilage or obsolescence.
Enhancing Warehousing and Storage
Proper warehousing and storage are vital to maintaining product quality and accessibility.
Management and field staff can collaborate to design efficient warehouse layouts and storage solutions.
This includes organizing products in a way that facilitates quick retrieval and minimizes movement.
Field personnel, who frequently interact with the stock, can provide feedback about the practicality of the layout.
Their input can lead to adjustments that speed up the picking and packing processes, improving overall efficiency and reducing order fulfillment times.
Improving Order Fulfillment
Efficient order fulfillment is directly linked to customer satisfaction.
By collaborating, management and field teams can ensure that orders are processed accurately and shipped on time.
Management can invest in technologies such as automated picking systems or advanced tracking software that streamline these processes.
Field staff, being the executors of order preparation, can offer insights into the workflow, suggesting improvements to speed up the fulfillment process.
Regular feedback sessions between the two groups can highlight inefficiencies and drive process enhancements.
Leveraging Technology
Incorporating technology into inventory management is essential for staying competitive.
Management can lead the way by adopting inventory management software and technologies like RFID or barcoding systems.
These tools offer better accuracy, reduce manual errors, and provide a comprehensive overview of inventory statuses.
Field teams should be trained to use these technologies effectively, enabling them to provide accurate data that supports decision-making processes.
Collaboration in this area ensures that technology serves its purpose effectively and enhances the overall inventory management strategy.
Developing a Collaborative Culture
Fostering a collaborative culture is crucial for sustainable improvements in inventory management.
Management should encourage open communication and establish regular meetings between management and field teams.
This promotes a sense of unity and shared responsibility for inventory outcomes.
Investing in training programs can empower field teams with knowledge about inventory best practices, making them active participants in the optimization process.
Acknowledging and rewarding contributions from both sides can further bolster this collaborative atmosphere.
Monitoring and Continuous Improvement
Inventory management is not a set-it-and-forget-it task.
It requires continuous monitoring and improvement.
Management and field teams should establish key performance indicators (KPIs) to measure the success of inventory processes.
Regularly reviewing these KPIs through collaborative meetings can help identify trends, issues, and areas for further improvement.
A cycle of feedback and enhancement keeps the inventory process agile and responsive to changing business needs and market conditions.
Conclusion
In the dynamic world of business, improving inventory management through collaboration between management and field teams is no longer optional; it’s a necessity.
Optimizing processes from procurement to shipping ensures that businesses can meet demand efficiently while minimizing costs.
Collaboration fosters a culture of continuous improvement, keeping businesses nimble and responsive to changes in the market landscape.
By embracing collaboration and making use of modern technologies, companies can achieve a streamlined inventory management system that supports overall business growth.
資料ダウンロード
QCD調達購買管理クラウド「newji」は、調達購買部門で必要なQCD管理全てを備えた、現場特化型兼クラウド型の今世紀最高の購買管理システムとなります。
ユーザー登録
調達購買業務の効率化だけでなく、システムを導入することで、コスト削減や製品・資材のステータス可視化のほか、属人化していた購買情報の共有化による内部不正防止や統制にも役立ちます。
NEWJI DX
製造業に特化したデジタルトランスフォーメーション(DX)の実現を目指す請負開発型のコンサルティングサービスです。AI、iPaaS、および先端の技術を駆使して、製造プロセスの効率化、業務効率化、チームワーク強化、コスト削減、品質向上を実現します。このサービスは、製造業の課題を深く理解し、それに対する最適なデジタルソリューションを提供することで、企業が持続的な成長とイノベーションを達成できるようサポートします。
オンライン講座
製造業、主に購買・調達部門にお勤めの方々に向けた情報を配信しております。
新任の方やベテランの方、管理職を対象とした幅広いコンテンツをご用意しております。
お問い合わせ
コストダウンが利益に直結する術だと理解していても、なかなか前に進めることができない状況。そんな時は、newjiのコストダウン自動化機能で大きく利益貢献しよう!
(Β版非公開)