- お役立ち記事
- For production engineers in the electronic equipment manufacturing industry! Standardize soldering rework and improve work efficiency
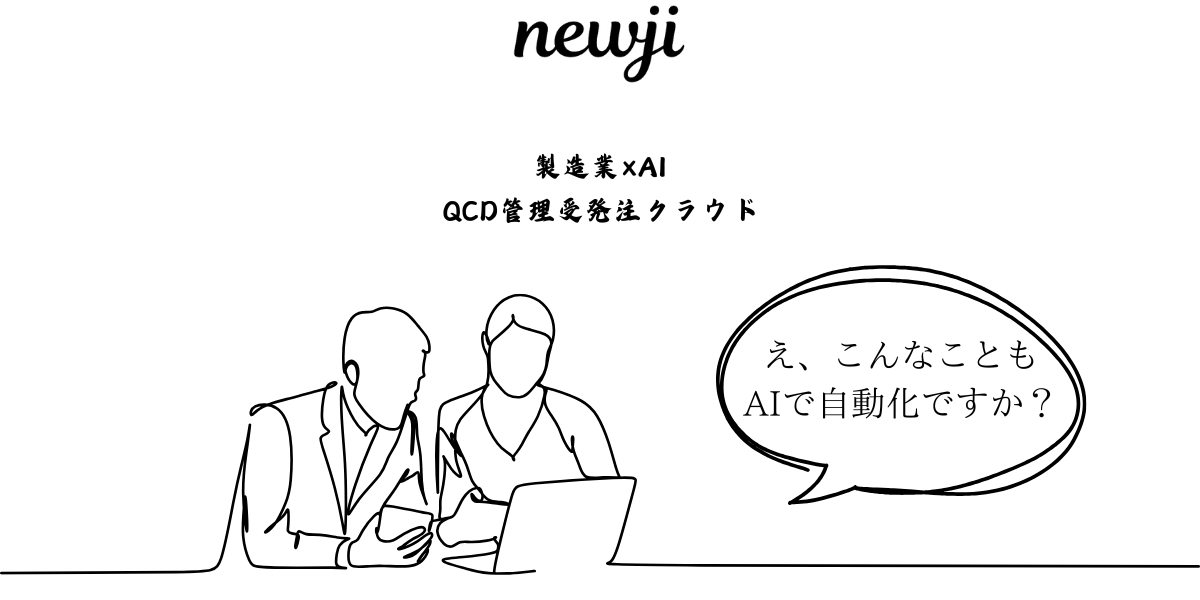
For production engineers in the electronic equipment manufacturing industry! Standardize soldering rework and improve work efficiency
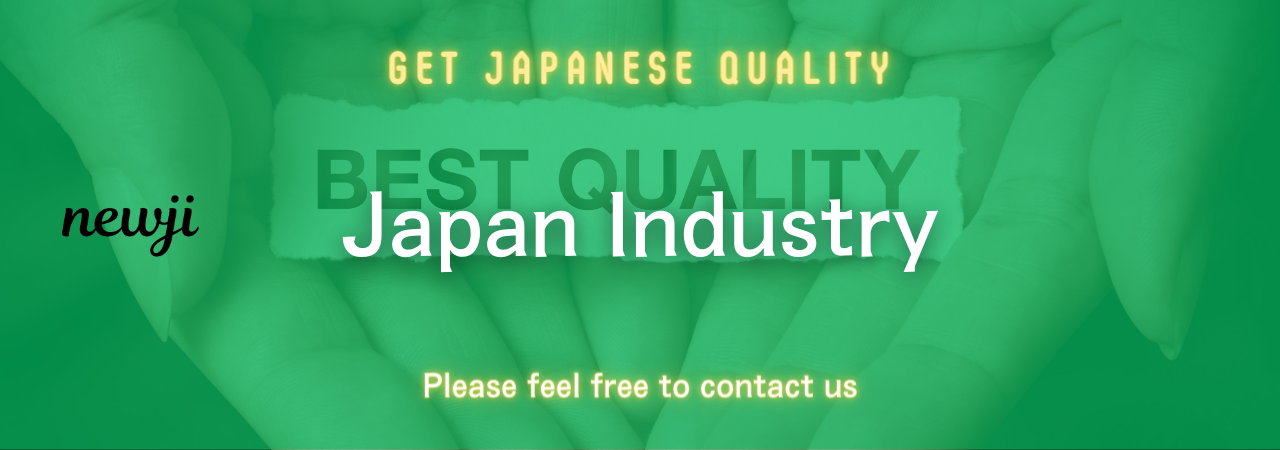
目次
Understanding Soldering Rework in Electronic Equipment Manufacturing
Soldering is a critical process in the electronic equipment manufacturing industry.
It involves joining components together through molten solder to ensure a stable and reliable electrical connection.
However, due to the intricate nature of electronic devices, rework is sometimes necessary.
Rework refers to the process of correcting defects or making adjustments to soldered components.
While rework is often unavoidable, managing it efficiently can result in improved work performance and product quality.
The key to achieving this lies in standardizing the soldering rework processes.
The Importance of Standardizing Soldering Rework
A standardized approach to soldering rework ensures consistency, quality, and efficiency across the manufacturing process.
With a standardized system in place, production engineers can reduce the variability in rework outcomes, which is crucial to maintaining high standards in the final products.
Standardization aids in minimizing errors and ensuring that each technician follows the same procedures.
This consistency results in reduced time spent on rework, lower costs, and a decrease in material waste.
Another benefit of standardizing soldering rework is that it facilitates training and supervision of the workforce.
Standard guidelines mean that new engineers and technicians can be trained more quickly and effectively.
Their performance can be measured and improved against a known benchmark, ultimately reducing the learning curve and increasing productivity.
Steps to Standardize Soldering Rework
1. Develop a Workflow and Documentation
The first step in standardizing soldering rework is to develop a detailed workflow that outlines each stage of the process.
This includes the initial assessment of defects, selection of tools and materials, execution of rework, and final inspection.
All procedures should be meticulously documented to ensure that every aspect is captured.
Clear documentation helps in providing a reference point for production engineers and technicians, ensuring that everyone follows the same practices.
2. Choose the Right Tools and Materials
Standardization involves selecting the right tools and soldering materials for rework tasks.
This can include choosing the appropriate soldering iron, soldering wire, flux, and desoldering equipment.
Standardizing these elements helps in reducing variability in the soldered joints and ensures a consistent quality in the reworked components.
Ensuring that all team members are trained to use these selected tools effectively is critical.
Regular checks and maintenance of equipment can also help in maintaining the consistency and quality of rework.
3. Implement Quality Control Measures
Quality control is a cornerstone of standardization.
It involves consistent and thorough checks at each stage of the soldering rework process.
Set up a checklist or inspection criteria that must be followed for each rework job.
This includes visual inspections, testing for functional performance, and checking for defects.
Feedback loops should be established to continuously refine and adjust the rework process to improve outcomes.
This iterative process ensures that any discovered inefficiencies or errors can be corrected swiftly.
4. Establish Training and Continuous Improvement Programs
Continuous training programs should be instituted to keep the workforce updated on the latest soldering techniques and reworking standards.
Training not only includes practical skills but also covers safety protocols to ensure a safe working environment.
Encourage feedback from production engineers and technicians who are actively involved in the reworking process.
Their insights can be invaluable in identifying areas that need improvement and in refining the standard procedures further.
Enhancing Efficiency through Standardization
Once processes are standardized, production engineers can expect improved efficiency in their operations.
The time taken for rework will decrease as technicians will be familiar and confident with the consistent procedures in place.
Reduced rework time translates to increased throughput.
Fewer bottlenecks and delays mean the production line runs smoothly, and customers can get their products faster.
This improvement in efficiency directly correlates to a healthier bottom line for manufacturers.
Additionally, standardized processes help in maintaining a steady supply chain, as the predictability of tasks ensures better planning and resource allocation.
Conclusion
For production engineers in the electronic equipment manufacturing industry, standardizing soldering rework is vital to achieving improved efficiency and higher quality products.
Through detailed workflow documentation, choosing the right tools and materials, implementing quality control measures, and providing thorough training, the rework process can be optimized.
By doing so, manufacturers can not only increase productivity but also ensure that their products meet the highest quality standards.
This holds significant potential for competitive advantages in today’s fast-paced technological landscape.
資料ダウンロード
QCD調達購買管理クラウド「newji」は、調達購買部門で必要なQCD管理全てを備えた、現場特化型兼クラウド型の今世紀最高の購買管理システムとなります。
ユーザー登録
調達購買業務の効率化だけでなく、システムを導入することで、コスト削減や製品・資材のステータス可視化のほか、属人化していた購買情報の共有化による内部不正防止や統制にも役立ちます。
NEWJI DX
製造業に特化したデジタルトランスフォーメーション(DX)の実現を目指す請負開発型のコンサルティングサービスです。AI、iPaaS、および先端の技術を駆使して、製造プロセスの効率化、業務効率化、チームワーク強化、コスト削減、品質向上を実現します。このサービスは、製造業の課題を深く理解し、それに対する最適なデジタルソリューションを提供することで、企業が持続的な成長とイノベーションを達成できるようサポートします。
オンライン講座
製造業、主に購買・調達部門にお勤めの方々に向けた情報を配信しております。
新任の方やベテランの方、管理職を対象とした幅広いコンテンツをご用意しております。
お問い合わせ
コストダウンが利益に直結する術だと理解していても、なかなか前に進めることができない状況。そんな時は、newjiのコストダウン自動化機能で大きく利益貢献しよう!
(Β版非公開)