- お役立ち記事
- The Japanese Manufacturing Revolution: Unraveling the Secrets Behind its Global Dominance
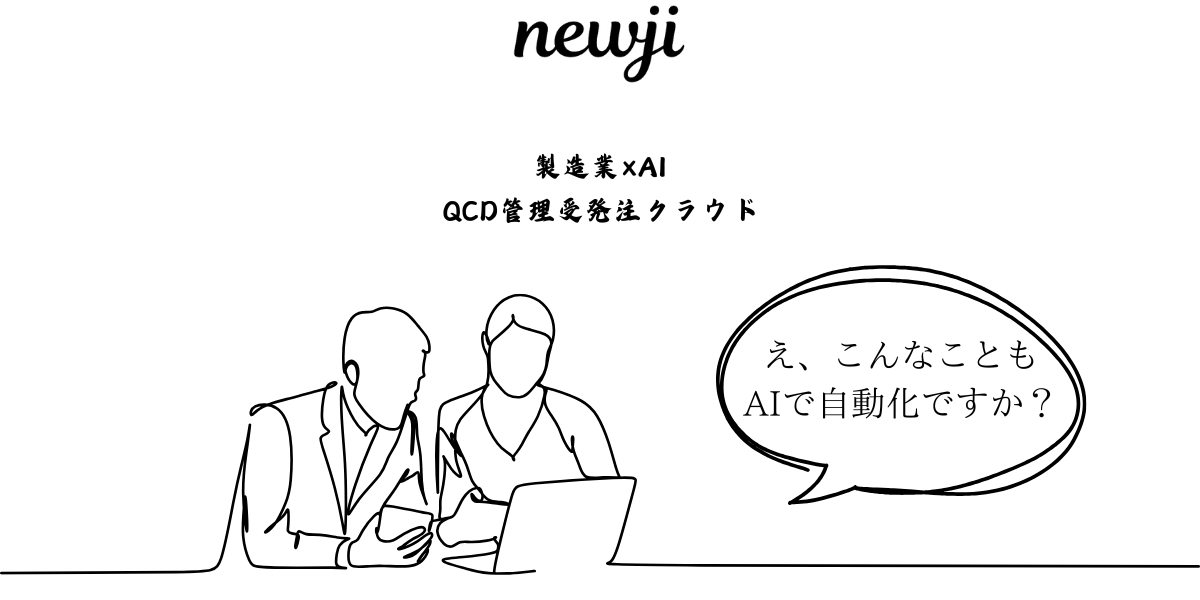
The Japanese Manufacturing Revolution: Unraveling the Secrets Behind its Global Dominance
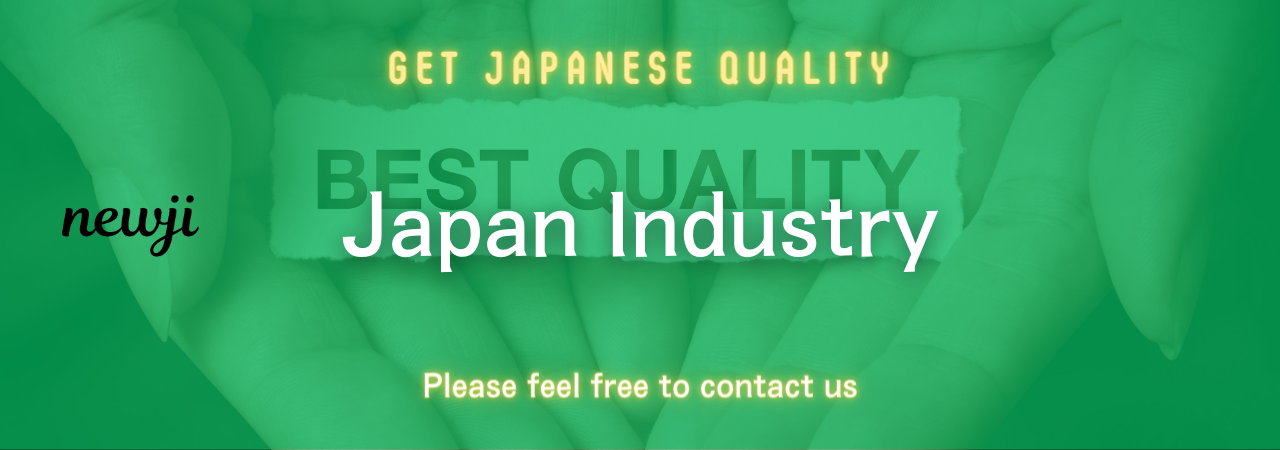
目次
Introduction to the Japanese Manufacturing Revolution
Japan has long been recognized as a powerhouse in the global manufacturing landscape. The country’s ability to innovate, adapt, and maintain high standards has positioned it at the forefront of various industries. This article delves into the strategies and practices that have fueled Japan’s manufacturing dominance, offering insights for companies worldwide seeking to emulate its success.
Historical Context and Evolution
Post-War Industrial Growth
After World War II, Japan embarked on a path of rapid industrialization. The government played a pivotal role in rebuilding the economy, focusing on sectors like automotive and electronics. This period saw the emergence of key players who would later become global giants.
Adoption of Lean Manufacturing
In the latter half of the 20th century, Japan pioneered lean manufacturing principles. Emphasizing waste reduction, efficiency, and quality, these practices revolutionized production processes. The Toyota Production System became a benchmark for excellence, influencing manufacturing worldwide.
Key Factors Behind Japan’s Manufacturing Success
Quality Control and Continuous Improvement
Japanese manufacturers prioritize quality at every stage of production. The philosophy of Kaizen, or continuous improvement, encourages incremental enhancements. This focus ensures that products meet stringent standards and consistently satisfy consumer expectations.
Efficient Procurement and Purchasing Practices
Effective procurement strategies are central to Japan’s manufacturing efficiency. Building strong relationships with suppliers ensures reliable sourcing of high-quality materials. Just-in-time inventory systems minimize waste and reduce storage costs, enhancing overall operational efficiency.
Advanced Production Engineering and Automation
Japan leads in the integration of advanced technologies and automation in manufacturing. Robotics and smart manufacturing systems increase precision and reduce human error. This technological prowess allows for scalable production and adaptability to changing market demands.
Advantages of Japanese Manufacturing Practices
Japanese manufacturing offers several advantages that contribute to its global success. First, the emphasis on quality ensures that products are reliable and durable, fostering customer trust. Second, the lean approach reduces costs and increases efficiency, making Japanese products competitive in price-sensitive markets. Additionally, strong supplier relationships and efficient logistics contribute to a smooth and responsive supply chain, enabling timely delivery and flexibility.
Challenges and Disadvantages
Despite its strengths, Japanese manufacturing faces challenges. High labor costs can impact competitiveness, especially in industries where cost is a critical factor. Additionally, the rigorous focus on quality and continuous improvement can sometimes lead to slower decision-making processes. Balancing innovation with traditional practices is another hurdle, as companies must adapt to rapidly changing global markets while maintaining their established standards.
Supplier Negotiation Techniques
Japanese companies excel in supplier negotiations through trust-building and long-term partnerships. Open communication and mutual respect are fundamental, fostering collaboration rather than competition. Techniques such as total cost of ownership analysis ensure that both parties consider all aspects of the transaction, leading to more sustainable and beneficial agreements.
Market Conditions and Adaptability
Japan’s ability to adapt to market conditions is a key factor in its manufacturing success. Companies invest heavily in market research and trend analysis, allowing them to anticipate and respond to changes promptly. Flexibility in production processes enables swift adjustments to product lines, ensuring that Japanese manufacturers remain relevant and competitive in diverse markets.
Best Practices for Adopting Japanese Manufacturing Principles
Organizations looking to adopt Japanese manufacturing principles should focus on several best practices. First, implement a culture of continuous improvement by encouraging employee feedback and regularly reviewing processes. Second, establish strong relationships with suppliers based on trust and collaboration. Third, invest in training and development to ensure that employees are skilled in the latest technologies and methodologies. Finally, prioritize quality control at every stage of production to maintain high standards and customer satisfaction.
Conclusion
The Japanese manufacturing revolution offers valuable lessons in efficiency, quality, and adaptability. By understanding and implementing the strategies that have driven Japan’s global dominance, companies can enhance their own manufacturing processes. Embracing continuous improvement, fostering strong supplier relationships, and integrating advanced technologies are essential steps towards achieving manufacturing excellence in today’s competitive landscape.
資料ダウンロード
QCD調達購買管理クラウド「newji」は、調達購買部門で必要なQCD管理全てを備えた、現場特化型兼クラウド型の今世紀最高の購買管理システムとなります。
ユーザー登録
調達購買業務の効率化だけでなく、システムを導入することで、コスト削減や製品・資材のステータス可視化のほか、属人化していた購買情報の共有化による内部不正防止や統制にも役立ちます。
NEWJI DX
製造業に特化したデジタルトランスフォーメーション(DX)の実現を目指す請負開発型のコンサルティングサービスです。AI、iPaaS、および先端の技術を駆使して、製造プロセスの効率化、業務効率化、チームワーク強化、コスト削減、品質向上を実現します。このサービスは、製造業の課題を深く理解し、それに対する最適なデジタルソリューションを提供することで、企業が持続的な成長とイノベーションを達成できるようサポートします。
オンライン講座
製造業、主に購買・調達部門にお勤めの方々に向けた情報を配信しております。
新任の方やベテランの方、管理職を対象とした幅広いコンテンツをご用意しております。
お問い合わせ
コストダウンが利益に直結する術だと理解していても、なかなか前に進めることができない状況。そんな時は、newjiのコストダウン自動化機能で大きく利益貢献しよう!
(Β版非公開)