- お役立ち記事
- Strengthening quality control as international procurement progresses Basic countermeasures that purchasing departments should take
Strengthening quality control as international procurement progresses Basic countermeasures that purchasing departments should take
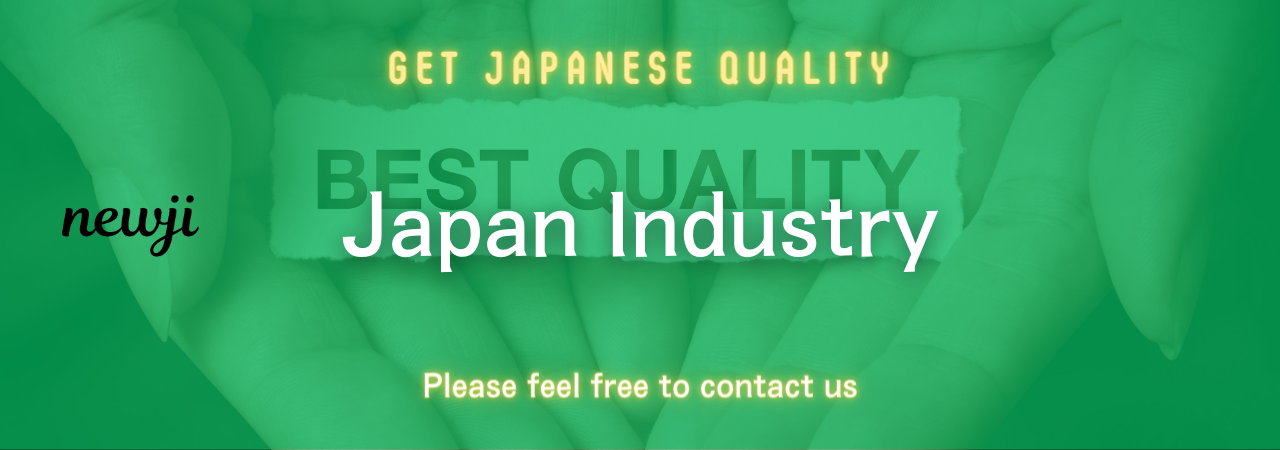
目次
Introduction to International Procurement
International procurement is becoming increasingly prevalent as companies seek to expand their operations globally.
It offers businesses the opportunity to access a wider range of suppliers, often at more competitive prices.
This globalization of supply chains, however, also introduces challenges, particularly in maintaining consistent quality control across diverse regions.
The purchasing departments of companies need to strengthen their quality control measures as they engage in international procurement.
Ensuring the quality of products and services sourced from different countries is crucial for maintaining the overall quality of the final product or service offered to customers.
The Importance of Quality Control
Quality control is an integral part of the procurement process.
It ensures that the goods and services purchased meet predefined standards and fulfill the requirements of the final product.
In international procurement, maintaining quality control is essential because of the diversity of suppliers and potential variations in quality standards.
Poor quality control can lead to increased costs, customer dissatisfaction, and damage to a company’s reputation.
Understanding International Standards
One of the first steps in enhancing quality control is understanding international quality standards.
Different countries may have varying definitions of “quality” and different regulatory requirements.
For purchasing departments, familiarizing themselves with international quality standards such as ISO 9001, can provide a benchmark for evaluating suppliers.
These standards help ensure that processes are in place for consistent quality management across the supply chain.
Establishing Clear Communication Channels
Effective communication is key to successful international procurement.
Misunderstandings due to language barriers, cultural differences, or unclear specifications can lead to quality issues.
Purchasing departments should establish clear and open communication channels with their international suppliers.
This includes setting clear expectations, having regular meetings, and developing detailed product specifications that leave no room for ambiguity.
Utilizing bilingual staff or translation services can further bridge communication gaps.
Developing Robust Supplier Evaluation Processes
Evaluating suppliers thoroughly before engaging in business relationships is crucial for ensuring quality control.
The purchasing department should implement comprehensive supplier evaluation processes to assess the capabilities and reliability of potential international suppliers.
Supplier Audits and Certification
Conducting supplier audits is an effective way to assess the quality control capabilities of suppliers.
These audits can be performed on-site or through virtual assessments.
Purchasing departments should look for suppliers with recognized quality certifications that demonstrate their commitment to quality standards.
Building Long-Term Relationships
Building long-term relationships with suppliers can lead to improved quality control and mutual benefits.
Establishing trust and collaboration allows for better alignment on quality expectations.
Long-term partnerships can also facilitate continuous improvement in quality control processes and encourage suppliers to invest in quality measures.
Implementing Technology in Quality Control
In today’s digital age, technology plays a crucial role in enhancing quality control measures in international procurement.
Purchasing departments can leverage various technological tools to monitor, assess, and maintain product quality.
Data Analytics and Quality Metrics
Using data analytics, companies can track key quality metrics and identify trends that indicate potential quality issues.
Tracking metrics such as defect rates, customer complaints, and returns can help purchasing departments detect problems early and address them promptly.
Quality Management Software
Quality management software systems are powerful tools that help streamline quality control processes.
These systems provide purchasing departments with real-time access to quality data, allowing for quick decision-making and proactive management of quality issues.
They also facilitate documentation of quality processes and compliance with international standards.
Continuous Improvement in Quality Control
Strengthening quality control in international procurement is an ongoing process.
Continuous improvement should be a core focus of the purchasing department’s strategy.
Training and Skill Development
Investing in training and skill development for purchasing department staff is essential for maintaining high-quality standards.
Providing training on the latest quality control practices, international standards, and technologies can empower staff to perform their roles effectively.
Feedback and Adjustment
Encouraging feedback from suppliers, customers, and internal teams is important for identifying areas for improvement.
Purchasing departments should use this feedback to make necessary adjustments to quality control processes and ensure continuous alignment with company goals and market needs.
Conclusion
As international procurement becomes a cornerstone of business strategies, strengthening quality control is more critical than ever.
By understanding international standards, establishing reliable supplier evaluation processes, leveraging technology, and focusing on continuous improvement, purchasing departments can ensure the quality and consistency of products and services sourced globally.
This not only helps maintain a company’s reputation but also contributes to long-term success in the competitive global market.
資料ダウンロード
QCD調達購買管理クラウド「newji」は、調達購買部門で必要なQCD管理全てを備えた、現場特化型兼クラウド型の今世紀最高の購買管理システムとなります。
ユーザー登録
調達購買業務の効率化だけでなく、システムを導入することで、コスト削減や製品・資材のステータス可視化のほか、属人化していた購買情報の共有化による内部不正防止や統制にも役立ちます。
NEWJI DX
製造業に特化したデジタルトランスフォーメーション(DX)の実現を目指す請負開発型のコンサルティングサービスです。AI、iPaaS、および先端の技術を駆使して、製造プロセスの効率化、業務効率化、チームワーク強化、コスト削減、品質向上を実現します。このサービスは、製造業の課題を深く理解し、それに対する最適なデジタルソリューションを提供することで、企業が持続的な成長とイノベーションを達成できるようサポートします。
オンライン講座
製造業、主に購買・調達部門にお勤めの方々に向けた情報を配信しております。
新任の方やベテランの方、管理職を対象とした幅広いコンテンツをご用意しております。
お問い合わせ
コストダウンが利益に直結する術だと理解していても、なかなか前に進めることができない状況。そんな時は、newjiのコストダウン自動化機能で大きく利益貢献しよう!
(Β版非公開)