- お役立ち記事
- Specific methods for achieving zero errors using poka-yoke techniques that mid-level employees in the equipment maintenance department should master
Specific methods for achieving zero errors using poka-yoke techniques that mid-level employees in the equipment maintenance department should master
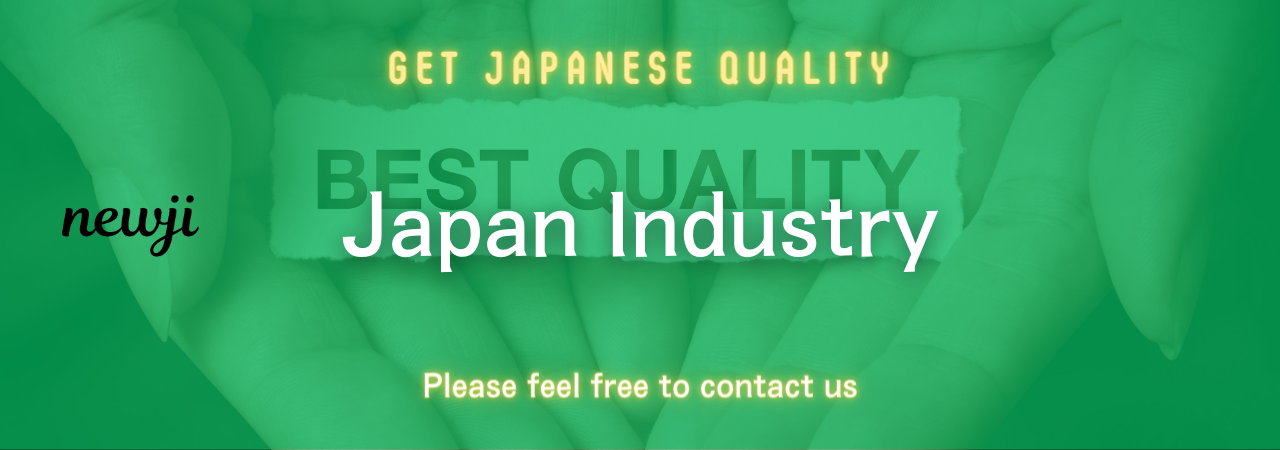
目次
Understanding Poka-Yoke Techniques
Poka-yoke is a Japanese term that means “mistake-proofing” or “error prevention.”
The concept was first introduced by Shigeo Shingo during the implementation of lean manufacturing at Toyota.
Poka-yoke aims to eliminate defects by preventing, correcting, or drawing attention to human errors as they occur.
In an equipment maintenance context, this means creating systems or processes that significantly reduce the likelihood of errors during maintenance tasks.
By applying poka-yoke techniques, mid-level employees in the equipment maintenance department can ensure their work is performed accurately and consistently, leading to increased efficiency and effectiveness.
Types of Poka-Yoke Techniques
There are mainly two types of poka-yoke techniques: prevention and detection.
Prevention
Prevention focuses on avoiding errors entirely before they happen.
This can be achieved by designing tasks in such a way that errors cannot occur.
For example, if a certain component can only be installed in one orientation, the risk of installing it incorrectly is eliminated.
Detection
Detection methods aim to identify errors as soon as they are made, allowing for immediate correction.
This can involve visual indicators, alarms, or other sensory signals that alert workers to a mistake.
Implementing detection methods allows for quick response and prevents further errors in the process.
Practical Poka-Yoke Methods for Maintenance Departments
There are numerous poka-yoke techniques that mid-level employees can master to achieve zero errors in their maintenance tasks.
Here are some specific methods:
1. Color-coding and Labeling
Color-coding and labeling are simple yet effective ways to prevent errors during maintenance work.
By using different colors or labels for various components or tools, employees can easily identify the right parts and proper procedures.
For instance, using red labels for high-voltage equipment or green for eco-friendly tools helps workers quickly recognize important information, reducing the chance of mistakes.
2. Checklists and Standard Operating Procedures (SOPs)
Implementing detailed checklists and SOPs ensures that all steps in a maintenance procedure are followed accurately.
By having a clear and thorough step-by-step guide, employees can prevent omissions and ensure consistency in their work.
Regularly updating these documents to reflect best practices and changing equipment specifications further enhances the effectiveness of this poka-yoke method.
3. Error-proof Tool Design
Designing tools that are difficult to use incorrectly is another effective poka-yoke approach.
For example, creating tools with unique shapes or features can prevent them from being used improperly.
A tool might fit only the specific fastener for which it was designed, thereby preventing mistakes.
Such designs eliminate the chance of human error and ensure precision during maintenance tasks.
4. Limit Switches and Sensors
Incorporating limit switches and sensors can help detect potential errors before they lead to equipment failure.
These devices can monitor various parameters and send alerts when a reading falls outside the acceptable range.
For instance, a sensor might detect abnormal vibrations in machinery and trigger an alarm before any damage occurs, allowing for prompt corrective action.
5. Training and Continuous Improvement
An essential aspect of poka-yoke implementation is training employees to identify potential errors and continuously improve processes.
Providing regular training sessions enables workers to keep up to date with the latest techniques, tools, and technologies.
Moreover, encouraging employees to suggest improvements fosters a culture of continuous enhancement, ultimately leading to a more efficient maintenance department.
Implementing Poka-Yoke Techniques in the Workplace
Successfully implementing poka-yoke techniques involves several key steps:
1. Identify Error-prone Areas
The first step in implementing poka-yoke is identifying areas where errors are most likely to occur.
Analyzing maintenance tasks and processes helps pinpoint potential weak spots or common mistakes.
Collaborating with team members to gather insights can provide a comprehensive understanding of where improvements are needed.
2. Design and Implement Solutions
After identifying error-prone areas, consider which poka-yoke techniques would be most effective in mitigating those risks.
Design and implement solutions, such as color-coded systems, checklists, or error-proof tools, that suit the specific needs of the department.
3. Monitor and Adjust
Once poka-yoke techniques have been implemented, continuously monitor their effectiveness.
Gather feedback from team members and assess whether error rates have decreased.
Make adjustments and improvements as necessary to ensure optimal performance.
4. Foster a Supportive Culture
Cultivate a workplace culture that supports poka-yoke principles by encouraging open communication and collaboration.
Recognize and reward employees who identify and address errors, and make sure to share success stories to inspire others.
Conclusion
By mastering specific poka-yoke techniques, mid-level employees in the equipment maintenance department can significantly reduce the occurrence of errors in their work.
Applying methods such as color-coding, checklists, and error-proof tool designs leads to more reliable and efficient maintenance processes.
Additionally, fostering a supportive culture and prioritizing training helps ensure continuous improvement and adaptability.
Through thoughtful implementation of poka-yoke principles, maintenance teams can achieve the goal of zero errors and enhance overall operational excellence.
資料ダウンロード
QCD調達購買管理クラウド「newji」は、調達購買部門で必要なQCD管理全てを備えた、現場特化型兼クラウド型の今世紀最高の購買管理システムとなります。
ユーザー登録
調達購買業務の効率化だけでなく、システムを導入することで、コスト削減や製品・資材のステータス可視化のほか、属人化していた購買情報の共有化による内部不正防止や統制にも役立ちます。
NEWJI DX
製造業に特化したデジタルトランスフォーメーション(DX)の実現を目指す請負開発型のコンサルティングサービスです。AI、iPaaS、および先端の技術を駆使して、製造プロセスの効率化、業務効率化、チームワーク強化、コスト削減、品質向上を実現します。このサービスは、製造業の課題を深く理解し、それに対する最適なデジタルソリューションを提供することで、企業が持続的な成長とイノベーションを達成できるようサポートします。
オンライン講座
製造業、主に購買・調達部門にお勤めの方々に向けた情報を配信しております。
新任の方やベテランの方、管理職を対象とした幅広いコンテンツをご用意しております。
お問い合わせ
コストダウンが利益に直結する術だと理解していても、なかなか前に進めることができない状況。そんな時は、newjiのコストダウン自動化機能で大きく利益貢献しよう!
(Β版非公開)