- お役立ち記事
- How to optimize structural design using CAE analysis that mid-level employees in the R&D department of the shipbuilding industry should know
How to optimize structural design using CAE analysis that mid-level employees in the R&D department of the shipbuilding industry should know
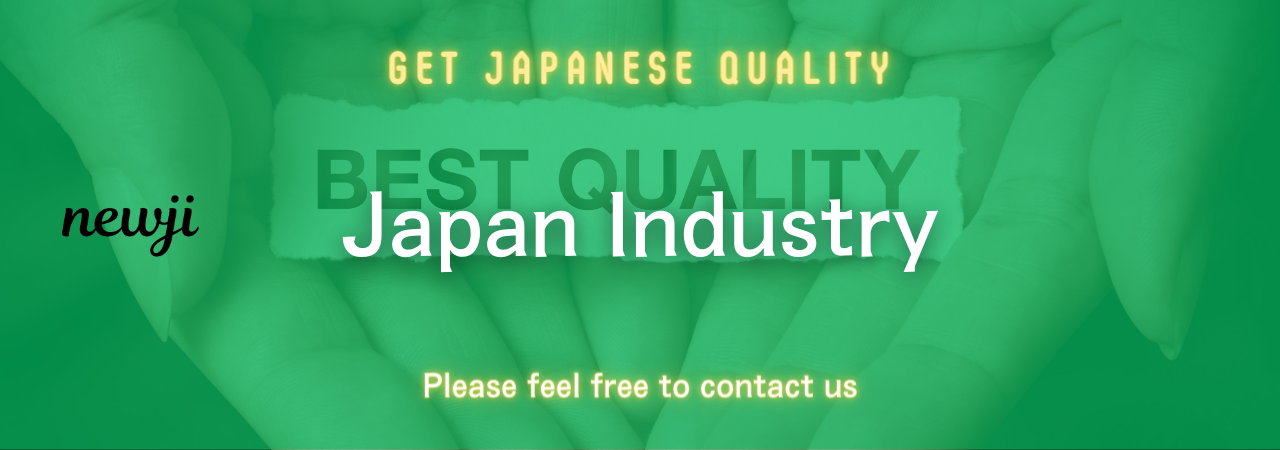
目次
Understanding CAE Analysis in Shipbuilding
In the shipbuilding industry, achieving optimal structural design is essential for building efficient and safe vessels.
Computer-Aided Engineering (CAE) analysis is an advanced method that aids engineers in evaluating the performance of ship structures under various conditions.
Mid-level employees in the R&D department can benefit greatly from understanding how to utilize CAE tools to optimize designs.
CAE encompasses a wide range of software tools that simulate different aspects of engineering, like stress analysis, thermal dynamics, and fluid flow.
In shipbuilding, these simulations help engineers predict how ships will behave under different sea conditions, loads, and speeds.
This predictive capability is crucial for optimizing structural designs, ensuring safety, and improving overall performance.
Why CAE is Important in Shipbuilding
CAE analysis allows ship designers to experiment with various design concepts before physical models are built.
By predicting how structures respond to real-world constraints, engineers can make informed decisions that lead to improved vessel performance and reduced costs.
Moreover, CAE tools are vital in identifying potential issues early in the design process, thereby avoiding costly redesigns.
In the competitive shipbuilding industry, the ability to quickly adapt and innovate is crucial.
CAE tools provide detailed insights into structural dynamics, enabling engineers to test different materials and configurations efficiently.
This agility in design and analysis supports the development of more sustainable and efficient ships, aligning with industry trends towards environmental compliance.
Key Benefits of Using CAE in Ship Design
Mid-level employees should grasp the key benefits of using CAE in ship design to maximize their contributions to the R&D department.
Enhanced Design Accuracy
One of the primary advantages of CAE is its capacity to simulate real-world scenarios with high accuracy.
This allows engineers to identify weak points in a design, assess structural integrity, and ensure compliance with safety standards.
Accurate simulations mean fewer prototypes, which translates to reduced development time and expenses.
Improved Design Flexibility
CAE software provides the flexibility to tweak designs by adjusting parameters easily.
Engineers can test various scenarios and design modifications, such as changing the weight distribution or material properties, to see how they affect the vessel’s performance.
This flexibility aids in optimizing design before moving to the construction phase.
Cost and Time Efficiency
By using CAE tools, shipbuilding companies can significantly cut down on the time required for the design process.
Virtual models eliminate the need for extensive physical testing, allowing engineers to focus on refining designs instead.
This reduction in physical prototyping and testing translates to cost savings and faster time-to-market.
Risk Mitigation
CAE analysis helps identify potential failure points or design flaws in ship structures.
By addressing these issues early in the design process, companies can minimize the risk of costly failures during or after construction.
This proactive approach safeguards company reputation and financial investments.
Steps for Implementing CAE Analysis
Integrating CAE analysis into the ship design process requires a structured approach.
Understanding these steps can empower mid-level employees to maximize the utility of CAE tools in their projects.
Define the Design Objectives
The first step is to clearly define the design objectives.
These objectives usually stem from project requirements, which include safety standards, performance goals, and budget constraints.
Having a well-defined set of goals helps in setting a clear direction for the analysis.
Create a Detailed CAD Model
A precise computer-aided design (CAD) model forms the basis for CAE analysis.
This digital representation of the ship includes all critical components and dimensions.
The accuracy of this model is paramount as it sets the foundation for subsequent simulations.
Perform Structural Analysis
With the CAD model in place, engineers perform structural analysis using CAE software.
This involves running simulations under various conditions such as weight loads, wind pressure, and sea states.
The analysis helps predict stress points, structural deformations, and potential areas of failure.
Iterate and Optimize
The insights gained from the simulations are used to iterate and optimize the design.
Changes are implemented in the CAD model, followed by re-analysis to confirm improvements.
This iterative process continues until the optimal design is achieved.
Validate the Design
Once the design has been refined, it undergoes validation to ensure its reliability and compliance with industry standards.
Validation may involve comparing the CAE analysis results with physical test data if available.
This step is crucial for verifying the integrity of the final design.
Challenges in CAE Implementation
Although CAE tools offer numerous benefits, their implementation presents certain challenges.
Mid-level employees should be aware of these to effectively navigate their use in design projects.
Technical Expertise
Effective utilization of CAE software requires a strong technical foundation.
Employees need to be well-versed in both the theoretical and practical aspects of CAE methods.
Continuous training and upskilling are necessary to keep pace with software advancements and industry requirements.
Data Management
CAE analyses generate large volumes of data that need to be managed efficiently.
Organizing and interpreting this data requires robust data management systems and practices to ensure accuracy and accessibility.
Integration with Other Systems
Ensuring seamless integration of CAE tools with other company systems is essential for a streamlined workflow.
This integration can be technically challenging and may require bespoke solutions, especially in legacy systems.
Conclusion: Embracing CAE for Better Outcomes
For mid-level employees in the R&D departments of the shipbuilding industry, harnessing the power of CAE analysis is key to optimizing structural design.
By understanding and applying CAE methodologies, they can significantly enhance design accuracy, flexible iteration, cost efficiency, and risk mitigation.
Despite the challenges, a strategic approach to integrating CAE into the design process promises better performance and innovation in shipbuilding projects.
As the industry advances, staying proficient with CAE tools will be indispensable for career growth and organizational success.
資料ダウンロード
QCD調達購買管理クラウド「newji」は、調達購買部門で必要なQCD管理全てを備えた、現場特化型兼クラウド型の今世紀最高の購買管理システムとなります。
ユーザー登録
調達購買業務の効率化だけでなく、システムを導入することで、コスト削減や製品・資材のステータス可視化のほか、属人化していた購買情報の共有化による内部不正防止や統制にも役立ちます。
NEWJI DX
製造業に特化したデジタルトランスフォーメーション(DX)の実現を目指す請負開発型のコンサルティングサービスです。AI、iPaaS、および先端の技術を駆使して、製造プロセスの効率化、業務効率化、チームワーク強化、コスト削減、品質向上を実現します。このサービスは、製造業の課題を深く理解し、それに対する最適なデジタルソリューションを提供することで、企業が持続的な成長とイノベーションを達成できるようサポートします。
オンライン講座
製造業、主に購買・調達部門にお勤めの方々に向けた情報を配信しております。
新任の方やベテランの方、管理職を対象とした幅広いコンテンツをご用意しております。
お問い合わせ
コストダウンが利益に直結する術だと理解していても、なかなか前に進めることができない状況。そんな時は、newjiのコストダウン自動化機能で大きく利益貢献しよう!
(Β版非公開)