- お役立ち記事
- A must-see for design department managers in the tapestry manufacturing industry! Techniques for utilizing texture through weaving and printing
A must-see for design department managers in the tapestry manufacturing industry! Techniques for utilizing texture through weaving and printing
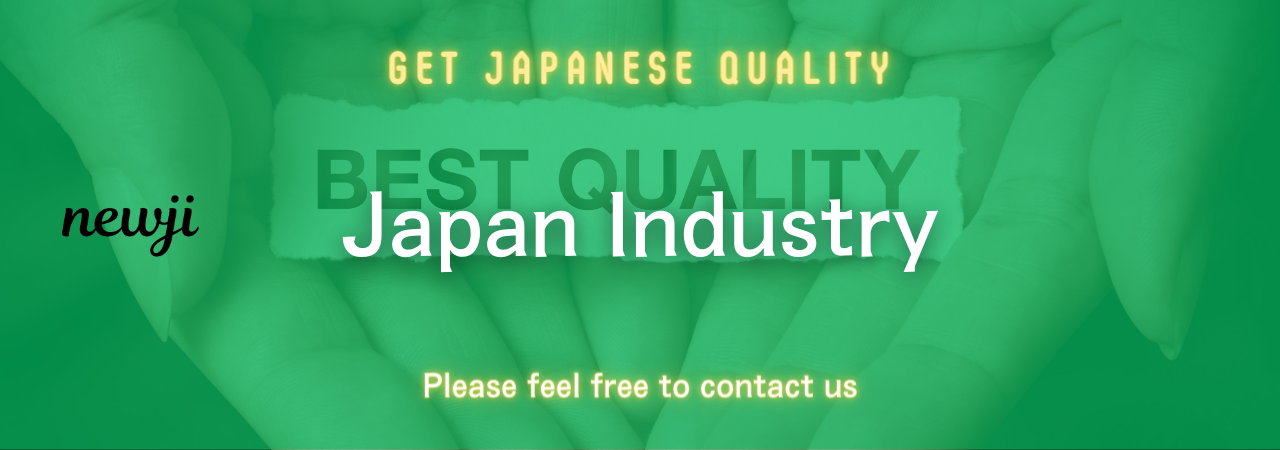
目次
Understanding Texture in Tapestry Manufacturing
In the tapestry manufacturing industry, texture plays a crucial role in the appearance and feel of the final product.
For managers in design departments, mastering techniques to utilize texture effectively can set your tapestries apart from the competition.
Two primary methods for incorporating texture in tapestry manufacturing are weaving and printing, each offering unique opportunities and challenges.
The Importance of Texture in Tapestry Design
Texture is a fundamental element of design that impacts both the aesthetic and tactile qualities of a tapestry.
It can convey visual interest, depth, and richness.
From the rough, tactile sensation of woven fibers to the smooth, printed surfaces, texture adds character to any design.
For customers, the texture of a tapestry can evoke emotions, memories, or simply provide a pleasant touch experience.
Understanding this can help you create products that not only meet functional needs but also connect emotionally with consumers.
Weaving Techniques for Texture
Weaving is a method used to interlace threads to form a fabric.
When creating textures through weaving, the choice of materials and weaving patterns are two critical considerations.
Choosing the Right Materials
The type of yarn and fibers used in weaving can significantly influence the texture of the tapestry.
Natural fibers such as wool, cotton, and silk provide different tactile sensations and appearances.
For example, wool can create a coarse texture, perfect for rustic or traditional designs, while silk provides a smooth and lustrous finish, ideal for luxurious tapestries.
Synthetic fibers, on the other hand, offer durability and resilience, allowing for innovative textural effects.
Exploring Weaving Patterns
Different weaving techniques create distinct textures and patterns.
Twill weaving, for example, is known for its diagonal rib pattern, adding dynamic texture.
On the other hand, jacquard weaving allows for complex patterns and rich textures, offering endless possibilities for custom designs.
Experimenting with various weaves can help you discover unique textures that align with your brand’s aesthetic vision.
Printing Techniques for Texture
While weaving directly incorporates texture through the structure of the material itself, printing offers another dimension of creative possibilities.
Through the use of inks and dyes, printing can add both visual and tactile textures to a tapestry.
Screen Printing
Screen printing is an effective technique to add bold textures to a tapestry.
By pushing ink through a stencil onto the fabric, designers can create raised textures that stand out visually and to the touch.
This technique allows for a high degree of customization, making it possible to incorporate intricate designs and logos into the fabric.
Digital Printing
Digital printing technology has evolved significantly, providing designers with more tools to add texture overlays to their work.
This technique uses sophisticated software to print detailed patterns and textures that may not be possible with traditional methods.
The capability to adjust color gradients and layering effects offers endless options for creating visual interest.
Heat Transfer Printing
Heat transfer printing is another method to add texture, especially for intricate details.
This involves applying heat and pressure to transfer pigments or foils onto the fabric, resulting in a gloss or matte finish.
This technique is particularly effective for creating textures like metallic sheens or raised, embossed designs.
Combining Techniques for Maximum Impact
Understanding how to blend weaving and printing techniques can lead to exceptional results.
By strategically using both methods, you can create tapestries that showcase a harmonious balance of depth and vibrancy.
Layering Textures
Consider layering printed textures over woven designs to add dimension and complexity.
Combining the two can highlight different areas of the tapestry, guiding the viewer’s attention through the piece.
This approach can make even simple designs feel sophisticated and multi-dimensional.
Experimentation and Innovation
Don’t be afraid to experiment with new materials and techniques.
The key to innovation often lies in the willingness to try something different.
Mix materials such as metallic yarns or incorporate unusual fibers into your weave, then highlight these elements with printing to accentuate the texture.
Conclusion
For design department managers in the tapestry manufacturing industry, mastering texture through weaving and printing offers significant potential to enhance product offerings.
By exploring and experimenting with different materials, weaving patterns, and printing techniques, managers can create unique and high-quality tapestries that attract and retain customers.
Remember, the power of texture lies not only in its visual appeal but in its ability to create an emotional connection with the consumer, making your tapestries memorable and desirable.
資料ダウンロード
QCD調達購買管理クラウド「newji」は、調達購買部門で必要なQCD管理全てを備えた、現場特化型兼クラウド型の今世紀最高の購買管理システムとなります。
ユーザー登録
調達購買業務の効率化だけでなく、システムを導入することで、コスト削減や製品・資材のステータス可視化のほか、属人化していた購買情報の共有化による内部不正防止や統制にも役立ちます。
NEWJI DX
製造業に特化したデジタルトランスフォーメーション(DX)の実現を目指す請負開発型のコンサルティングサービスです。AI、iPaaS、および先端の技術を駆使して、製造プロセスの効率化、業務効率化、チームワーク強化、コスト削減、品質向上を実現します。このサービスは、製造業の課題を深く理解し、それに対する最適なデジタルソリューションを提供することで、企業が持続的な成長とイノベーションを達成できるようサポートします。
オンライン講座
製造業、主に購買・調達部門にお勤めの方々に向けた情報を配信しております。
新任の方やベテランの方、管理職を対象とした幅広いコンテンツをご用意しております。
お問い合わせ
コストダウンが利益に直結する術だと理解していても、なかなか前に進めることができない状況。そんな時は、newjiのコストダウン自動化機能で大きく利益貢献しよう!
(Β版非公開)